My Grandma was right!! Idle hands are the Devils workshop!!! This week, I've been pretty darned idle. To the point where I have started building those tools that you only need "Once in a blue moon!!" I occasionally have to put snap ring grooves in small shafts, ranging from 3/16" up to 3/8". Up until now, I have "made do" by clamping a hacksaw blade to my toolpost in the lathe. Yesterday afternoon, I designed one which will fit into my AXA toolholder, which is a lot more secure and a lot safer. Hacksaw blades seem to be just the right width for this. I know I could have ground down an HSS toolbit and accomplished the same thing, however I have a lifetime supply of hacksaw blades so thought I would do it this way. Note that on the drawing there are a couple of dimensions with ### or *** after them. They are to remind you to measure your own hacksaw blade to use in this rig. My hacksaw blades are .027" thick x 0.458" wide--yours might be different.
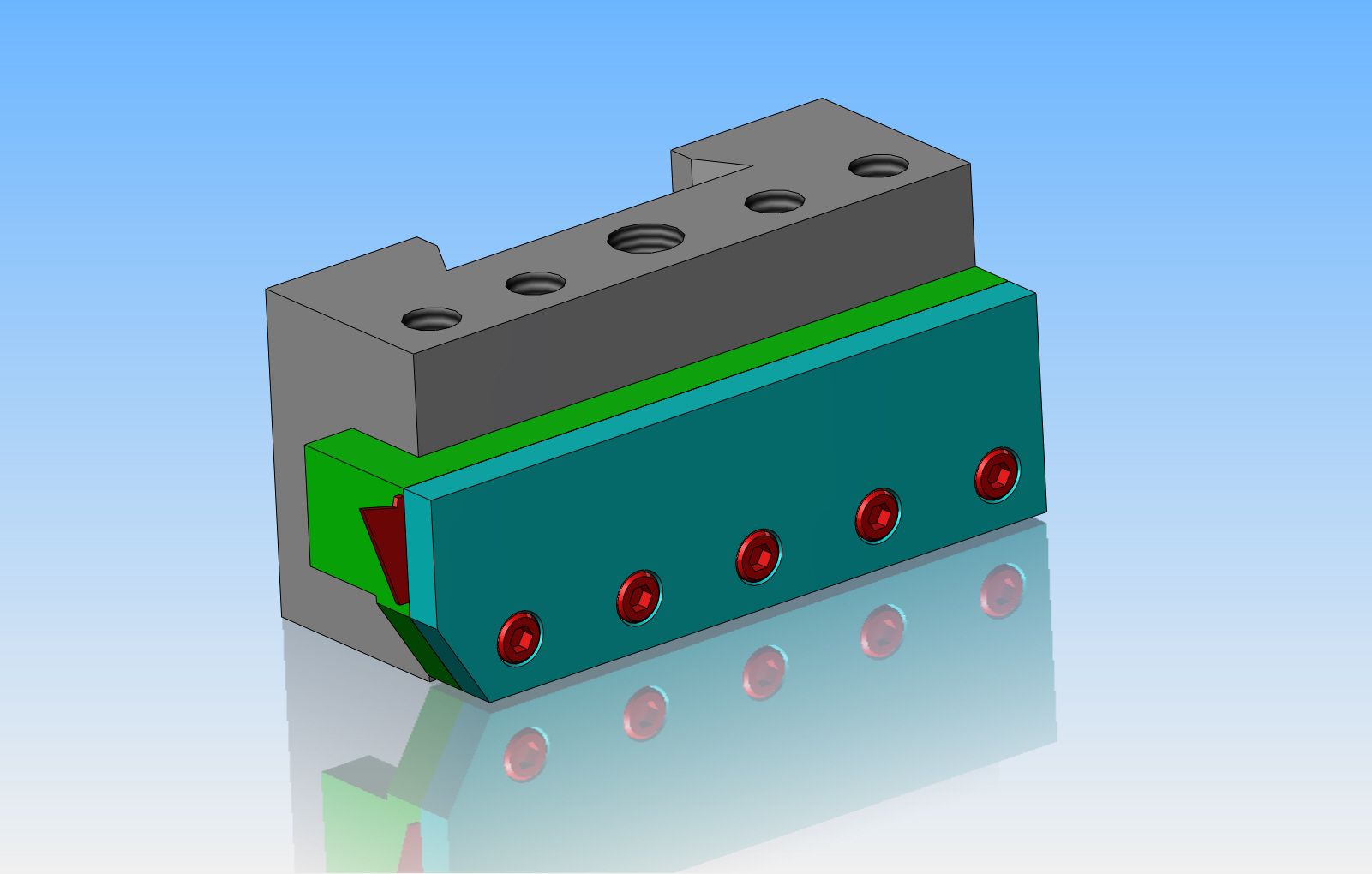
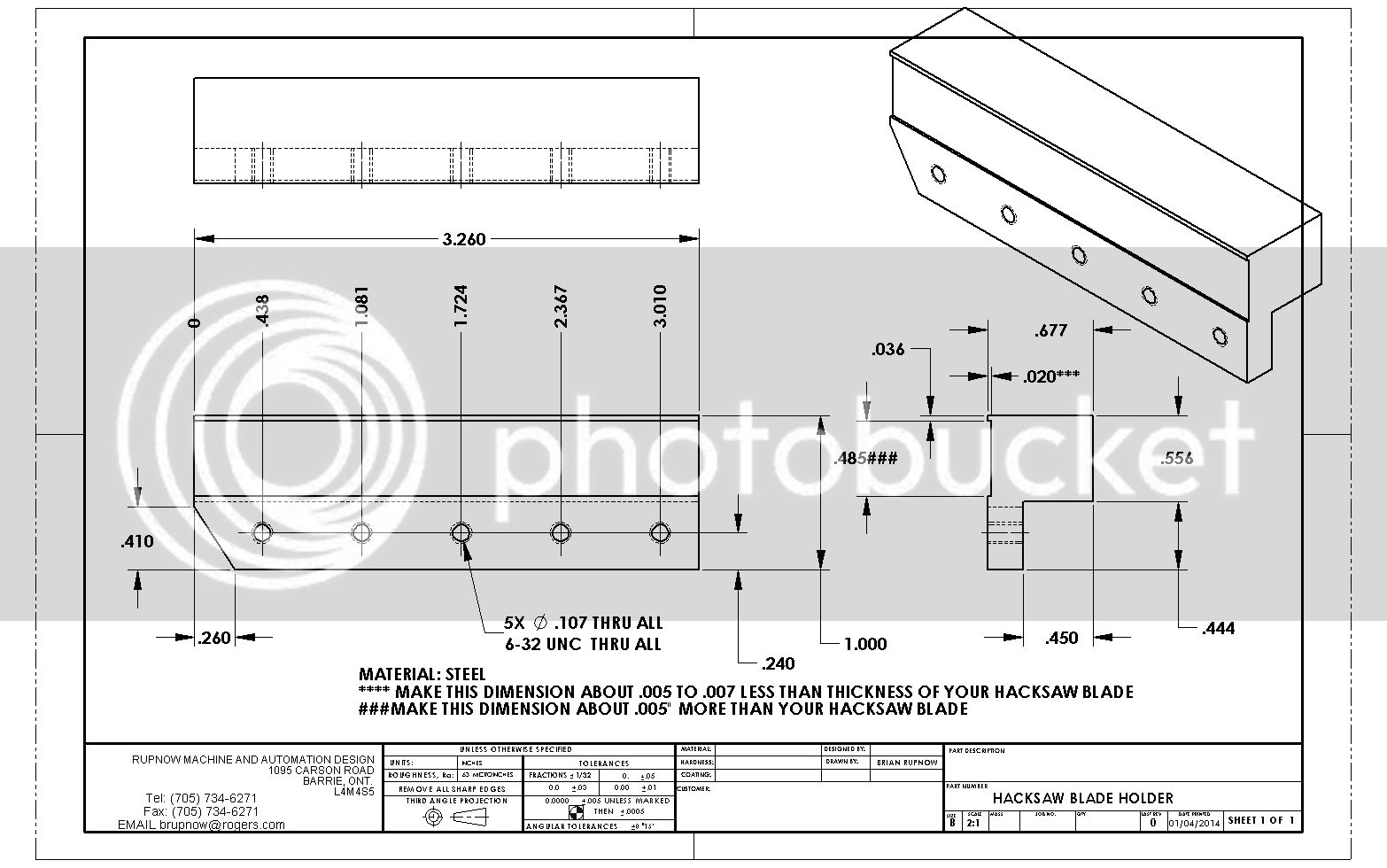
