Artie said:*** Shes clutched, 2 speed with an 8 inch stroke (I was told it was 6) with auto feeds on both axis. ***
She's a beauty Artie. I have a Sweedish made machine called a "Torpex" currently undergoing a restoration which is very similar to yours. It also seems to have the two-axis auto-feed capability. Would you mind sharing some more detailed images or videos of how yours operates?
Congratulations on the great tool find!
Bob Farr
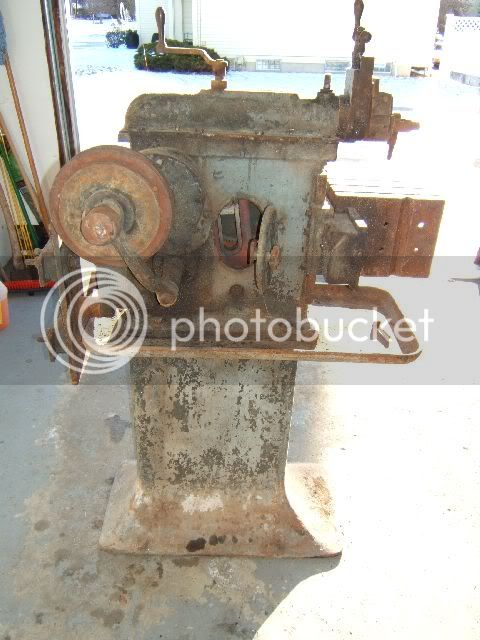
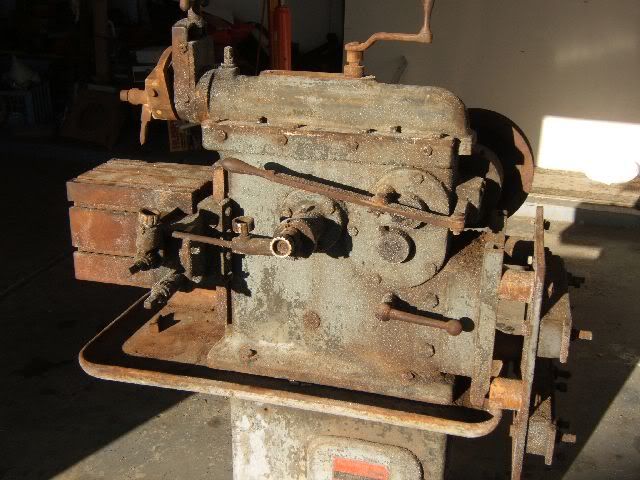
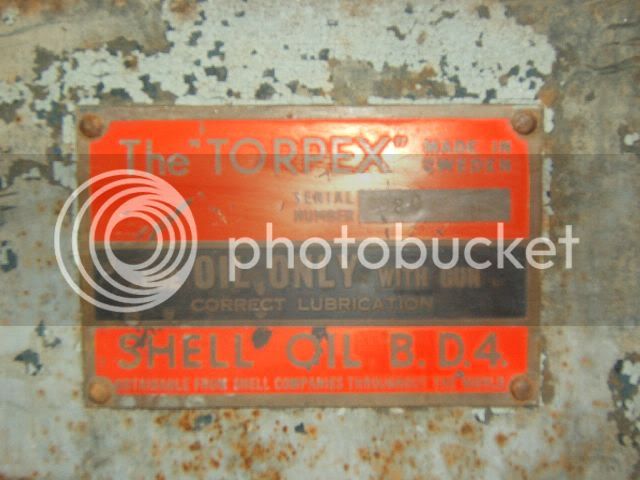