This morning I'm setting around with some free time, and I've been thinking for a while now about an overhead cam air cooled engine. There are a lot of horizontal and vertical cylinder engines out there, but I haven't seen very many single cylinder engines like the old "Iron Horse" washing machine engines with the cylinder on a 45 degree angle. My thoughts of course, were that if you could hang the entire camshaft off the cylinder head, then it would give you the freedom to run the cylinder on just about any angle you wanted. By using a cogged belt drive to the camshaft instead of a gear train, that opens up even more freedom with placement of components. I looked through all of the engines I have built over the past few years, and ended up leaning heavily on my Atkinson for some of this, so if it looks a bit familiar, then that is why. I'm not saying I'll actually build this, but you know how it is------Brian
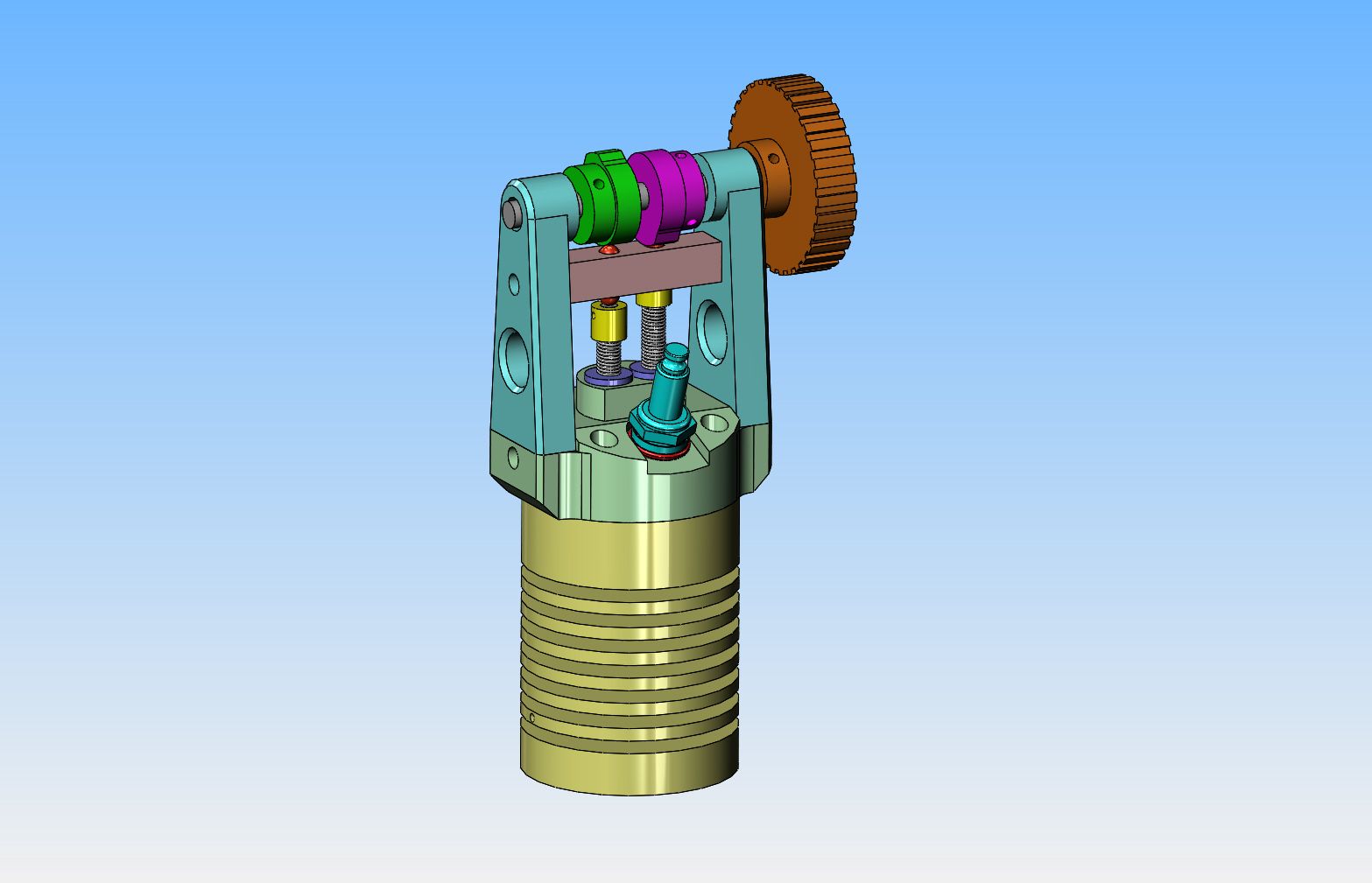