digiex-chris
Well-Known Member
- Joined
- Dec 6, 2010
- Messages
- 263
- Reaction score
- 58
I've got a Craftex (Busy Bee) B2227L that's got a nice geared head, but not a quick change threading gearbox or anything, just the usual changable gear train for threading. Soon I'm going to need to cut a left hand acme thread, so I decided it was time to get going on making this thing move the lead screw the opposite direction.
I couldn't use the methods many people use on the Grizzly lathes, I don't have the space for it and the gearing is setup a little differently. There's a 4:1 reduction inside the headstock to another spindle that's used for the output for the threading gears. This has a nice effect of reducing the error doing metric threads to so small no one cares except if you need an entire foot of thread engagement or are making metric leadscrews or something.
I picked a location for the extra gear so I could use almost any gear in the box as the idler/reverse gear and make it fit allowing me to make reverse threads of anything that's on the chart for my machine.
I needed two bolts, one to pivot the bracket on, and one to lock the pivoting. I popped the top open and measured the thickenss of the headstock casting, and found I had 0.375" to work with on the edge where I wouldn't break into the oil filled cavity inside. That let me use M6 bolts for everything and match the machine's metric fasteners. It's a funny machine, imperial leadscrews and threading capability, and metric fasteners holding it together.
Here's a photo of me milling the curved slot on my lathe using an old Taig headstock mounted to an angle plate. Worked pretty well, though it would have been a lot better if I had a faceplate to clamp the work to instead. Dear Santa, please send me a rotary table for Christmas. There's 3 holes in the bracket (well, 2 holes and a slot). The bottom hole I screwed a post into and made a bushing to go between the gear and the post.
And here's the finished result.
I couldn't use the methods many people use on the Grizzly lathes, I don't have the space for it and the gearing is setup a little differently. There's a 4:1 reduction inside the headstock to another spindle that's used for the output for the threading gears. This has a nice effect of reducing the error doing metric threads to so small no one cares except if you need an entire foot of thread engagement or are making metric leadscrews or something.
I picked a location for the extra gear so I could use almost any gear in the box as the idler/reverse gear and make it fit allowing me to make reverse threads of anything that's on the chart for my machine.
I needed two bolts, one to pivot the bracket on, and one to lock the pivoting. I popped the top open and measured the thickenss of the headstock casting, and found I had 0.375" to work with on the edge where I wouldn't break into the oil filled cavity inside. That let me use M6 bolts for everything and match the machine's metric fasteners. It's a funny machine, imperial leadscrews and threading capability, and metric fasteners holding it together.
Here's a photo of me milling the curved slot on my lathe using an old Taig headstock mounted to an angle plate. Worked pretty well, though it would have been a lot better if I had a faceplate to clamp the work to instead. Dear Santa, please send me a rotary table for Christmas. There's 3 holes in the bracket (well, 2 holes and a slot). The bottom hole I screwed a post into and made a bushing to go between the gear and the post.
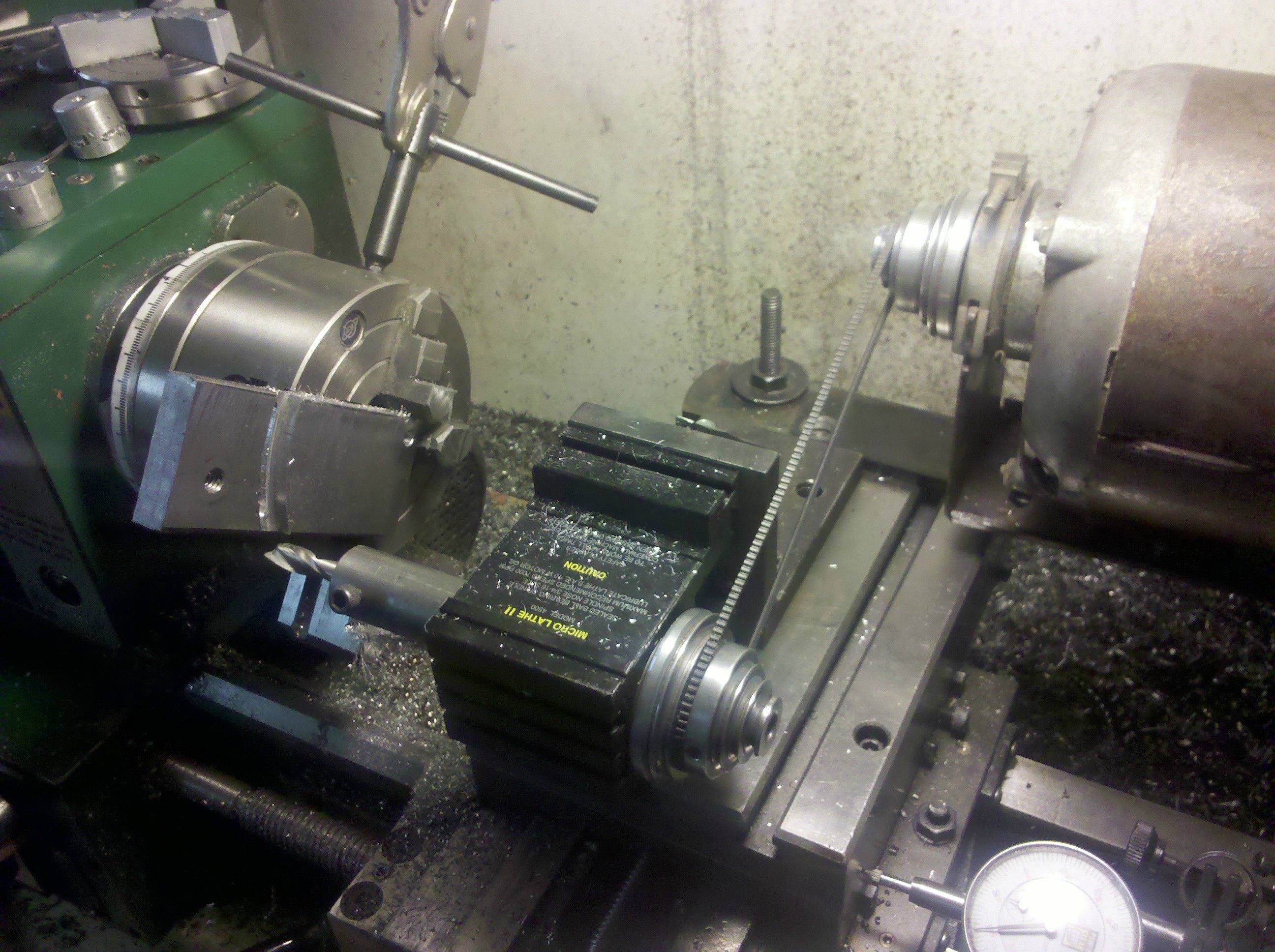
And here's the finished result.
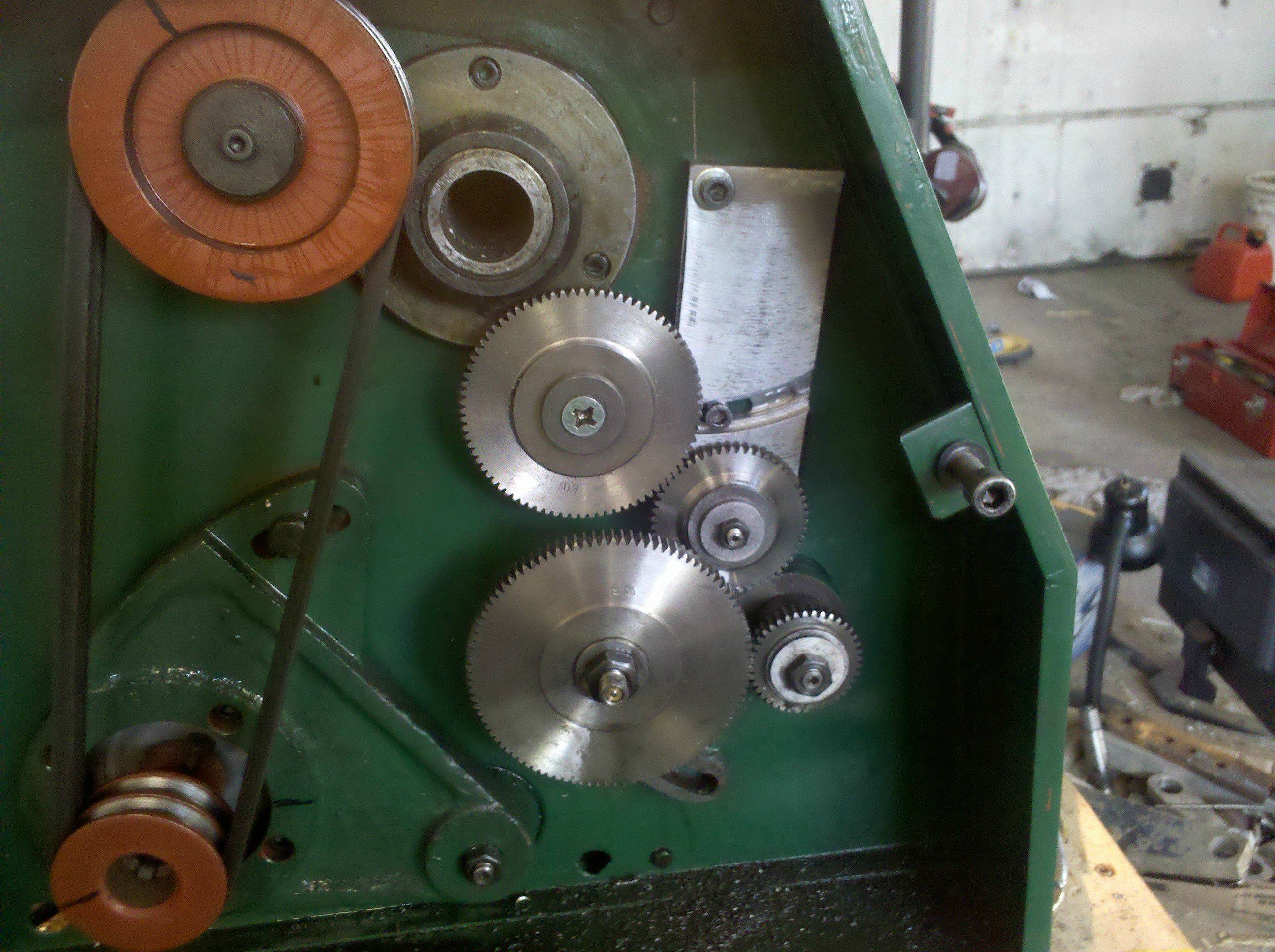