vlmarshall
Well-Known Member
- Joined
- Dec 28, 2008
- Messages
- 1,138
- Reaction score
- 1
Have any of you reduced the ID of copper tubing by rolling it? I'd like to try to reduce some 1/8" copper tube (.062" ID) down to around .012". A coworker suggested the idea, so I tried it first at work, with a bearing mounted in a knurling tool holder. It seemed to be working, until the copper work-hardened and snapped off at the collet.
Later I tried something similar at home, forcing the copper tubing between two bearings at angles. That didn't work either, the end of the copper cone i was forming work hardened and developed radial cracks.
Later I tried something similar at home, forcing the copper tubing between two bearings at angles. That didn't work either, the end of the copper cone i was forming work hardened and developed radial cracks.
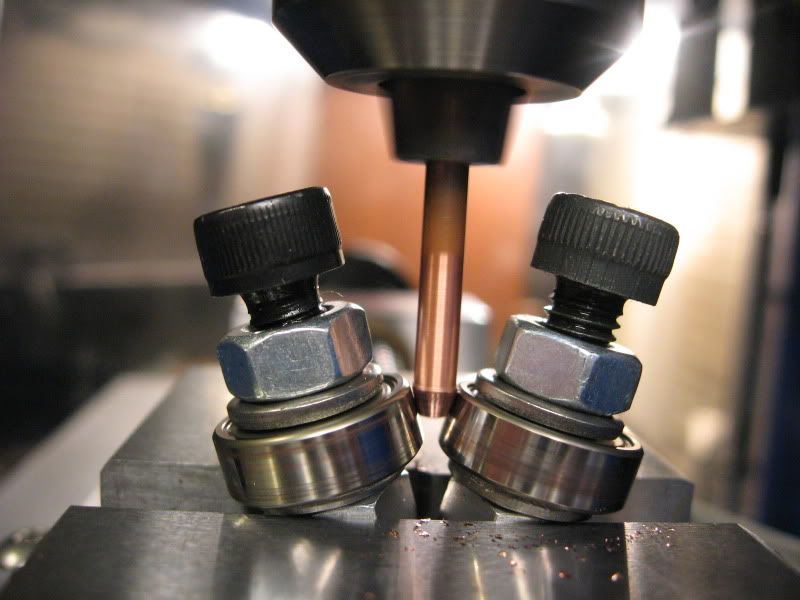