Well, this project has been one of those on again off again deals that gets picked up when I have time. It has been on going for about eight months. I had some time today and went out and got a few things done on it today.
I should be able to cut convex and concave radii from tiny to about 4 inches. I have a few more things to make for it, but it is coming along nicely. It isn't pretty, but I am not really going for pretty, either. Rigid is what the desired result is with this one.
The turret is some sort of unknown steel that really is not very fun to machine. I call it scrapatanium. It seems to have a tendency to work harden if the feeds aren't aggressive (it's certainly not stainless), and the surface looks as if the metal is being pulled off rather than cut. Rake angle changes didn't seem to help any.
There are also some spots that are soft compared to other areas, and that makes for some interesting effects on the surface as well. I have used carbide tooling to machine it because high speed steel didn't seem to be up to the task and wouldn't hold an edge.
Threading it is an exercise in patience with this mystery metal. I haven't broke a tap in it yet, and hope to not start that now! The taps will cut certain areas easilly, and other areas it is like tapping a file. Oh well, what does one expect for free!!
I should be able to cut convex and concave radii from tiny to about 4 inches. I have a few more things to make for it, but it is coming along nicely. It isn't pretty, but I am not really going for pretty, either. Rigid is what the desired result is with this one.
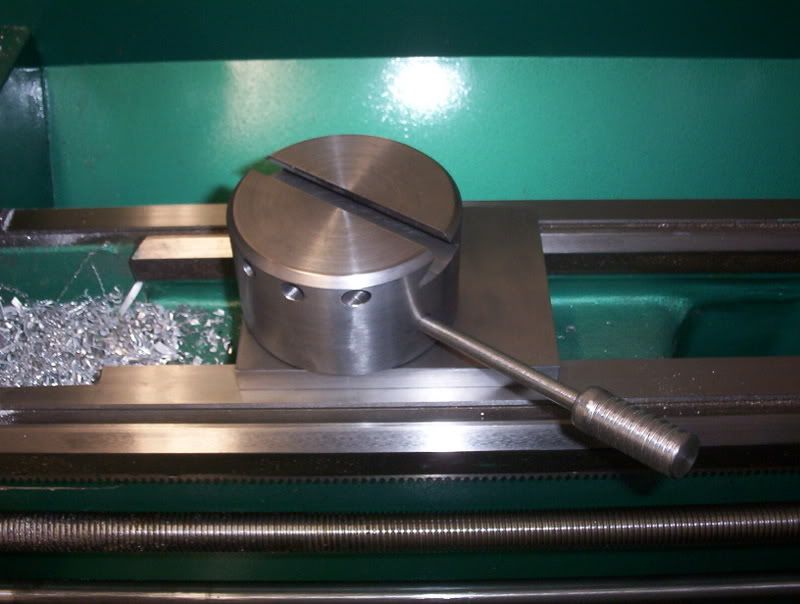
The turret is some sort of unknown steel that really is not very fun to machine. I call it scrapatanium. It seems to have a tendency to work harden if the feeds aren't aggressive (it's certainly not stainless), and the surface looks as if the metal is being pulled off rather than cut. Rake angle changes didn't seem to help any.
There are also some spots that are soft compared to other areas, and that makes for some interesting effects on the surface as well. I have used carbide tooling to machine it because high speed steel didn't seem to be up to the task and wouldn't hold an edge.
Threading it is an exercise in patience with this mystery metal. I haven't broke a tap in it yet, and hope to not start that now! The taps will cut certain areas easilly, and other areas it is like tapping a file. Oh well, what does one expect for free!!