Powder keg
Well-Known Member
- Joined
- Oct 10, 2007
- Messages
- 1,091
- Reaction score
- 3
Here is a quick picture of some of the patterns I'm trying to finish up. I just drew the layout the lines so I can drill them for the pins that will locate the two half's of my split patterns. I'll try and get some more photos of me doing this step.
I got a new camera and I need the practice
)
Later, Wes
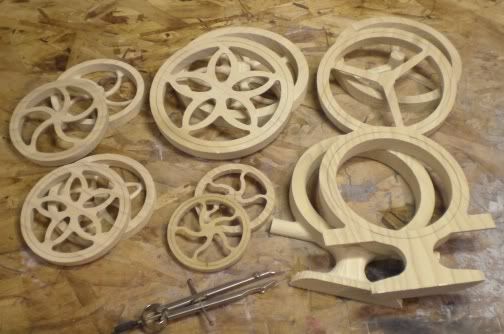
I got a new camera and I need the practice
Later, Wes