I seem to have clutches on the brain this last couple of months. This design incorporates a cone seating into a cone shaped recess to transmit torque from the left hand shaft to the right hand shaft. There is a very powerful coil spring that holds the clutch in the engaged position. When the handle is swung to the left it allows the powerful spring to seat the cone firmly into the cup and transmit torque. When the handle is swung to the right it separates the cone and cup and compresses the spring. The fact that the spring will be compressed by this action will make the linkage lock into an "over center" condition and stay there until it is changed by someone manually swinging the red handle.
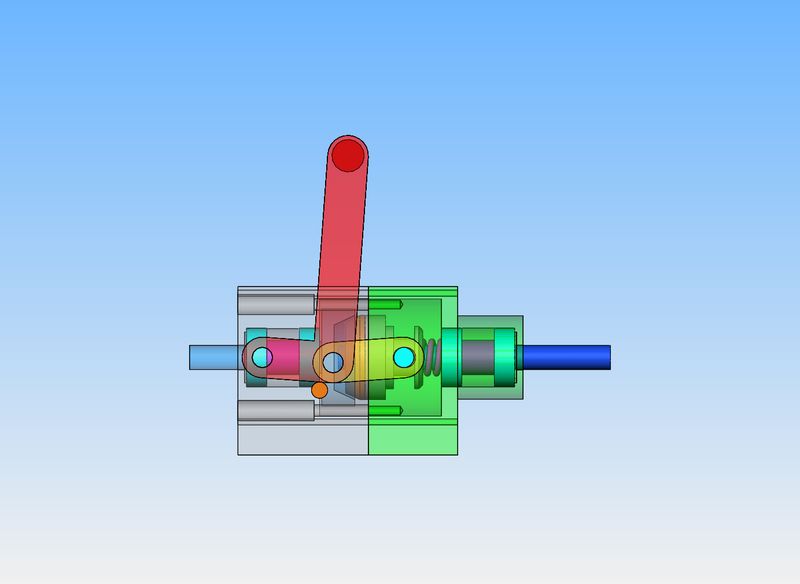
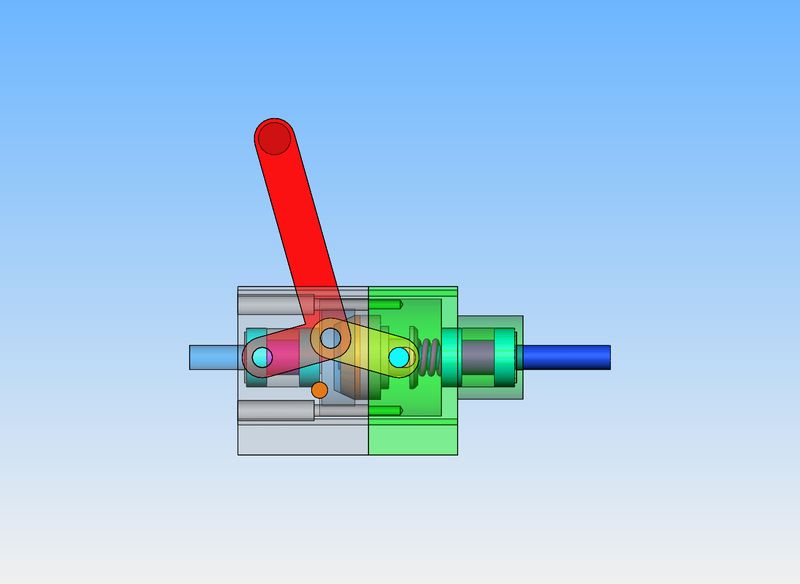