zeeprogrammer
Well-Known Member
- Joined
- Mar 14, 2009
- Messages
- 3,362
- Reaction score
- 13
Finally able to get to my shop and turn some metal...but as usual...I get stumped when things aren't clear as crystal.
Making two identical hose couplings. Drawing shows to turn the diameter to 0.175 and then thread the end for 3/16-40.
Stump 1: Drawing doesn't show how far to thread. I looked at the parts where the couplings are attached. Looks like one shouldn't be more than 0.125. The other is not so critical and can be longer. I would cut a thread relief using a bit of hack saw blade that's about 0.025 thick. So the threaded bit is really 0.1.
Does that seem sufficient? 40 TPI would result in just 4 threads.
Stump 2: 3/16-40 means to me a 0.187 outer diameter which is the diameter of the brass I'm using. As a test...I threaded the rod anyway...it cut easily and the coupling fit (loosely) in a hole tapped for 3/16-40. 0.187 to 0.175 seems a lot.
Is there a rule for what you cut the diameter down to when making a thread?
Further, as a hose coupling, why would I turn it down from 3/16? Seems like a standard size to fit hose to.
So I'm thinking I won't turn the rod down. I'll simply cut the relief and thread and then polish the rod. Comments?
Sorry for what has to be a pretty fundamental question...but you all know me...very new to all this.
On a happy note...I have improved my ability to measure incorrectly. Here's a pic of a thread relief cut...
Thanks.
Making two identical hose couplings. Drawing shows to turn the diameter to 0.175 and then thread the end for 3/16-40.
Stump 1: Drawing doesn't show how far to thread. I looked at the parts where the couplings are attached. Looks like one shouldn't be more than 0.125. The other is not so critical and can be longer. I would cut a thread relief using a bit of hack saw blade that's about 0.025 thick. So the threaded bit is really 0.1.
Does that seem sufficient? 40 TPI would result in just 4 threads.
Stump 2: 3/16-40 means to me a 0.187 outer diameter which is the diameter of the brass I'm using. As a test...I threaded the rod anyway...it cut easily and the coupling fit (loosely) in a hole tapped for 3/16-40. 0.187 to 0.175 seems a lot.
Is there a rule for what you cut the diameter down to when making a thread?
Further, as a hose coupling, why would I turn it down from 3/16? Seems like a standard size to fit hose to.
So I'm thinking I won't turn the rod down. I'll simply cut the relief and thread and then polish the rod. Comments?
Sorry for what has to be a pretty fundamental question...but you all know me...very new to all this.
On a happy note...I have improved my ability to measure incorrectly. Here's a pic of a thread relief cut...
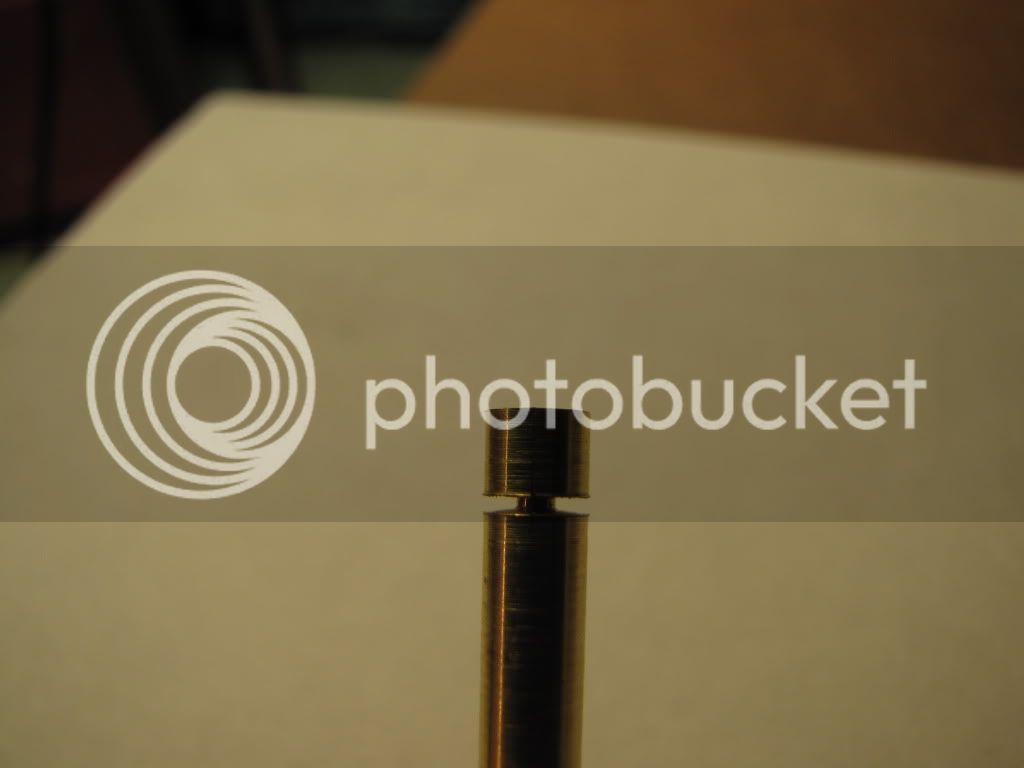
Thanks.