- Joined
- Jun 4, 2008
- Messages
- 3,285
- Reaction score
- 630
It's a Novakon NM-200. Details can be found at the Novakon website:
http://www.novakon.net/nm200.html
It was shipped last Wednesday, so one week end to end. The truck delivered 2 wooden palletized crates:
The smaller contains the stand:
I set it up to lift off the pallet with my auto lift. The base was attached to the pallet with a single bolt.
With the stand in the air, attaching the 6 feet was easy.
I adjusted the corner feet to be equal with the two centers a little short. Once the mill is in position I can level it more precisely. In any case, measuring with an electronic level after it was on the floor showed 1 degree off crosswise and 3 degrees lengthwise.
The chip pan is banded to one side of the mill crate.
With the sides and top of the crate removed, here's the mill as packed:
And with the packaging removed. Notice the steel bar that's protruding from the sides of the column. That's one I placed through the holes provided and that I will use to lift the mill off the pallet.
Here's the mill as seen from the rear:
I'm going to hold off until Friday for the assembly, as a friend will be available to lend a hand. I suspect the mill will tilt when lifted off the pallet. There are two eyebolts on the front of the base casting that can be used to level it off. Once in the air, I'll maneuver the stand and chip pan underneath and lower it down.
http://www.novakon.net/nm200.html
It was shipped last Wednesday, so one week end to end. The truck delivered 2 wooden palletized crates:
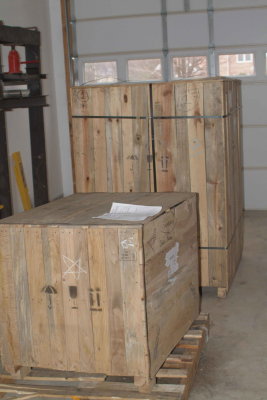
The smaller contains the stand:
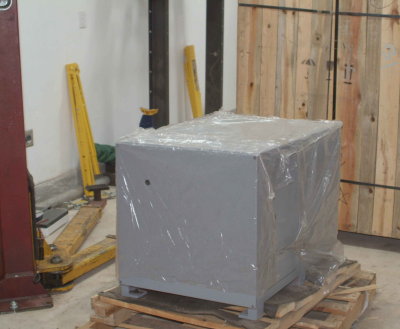
I set it up to lift off the pallet with my auto lift. The base was attached to the pallet with a single bolt.
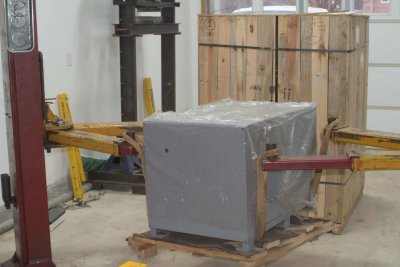
With the stand in the air, attaching the 6 feet was easy.
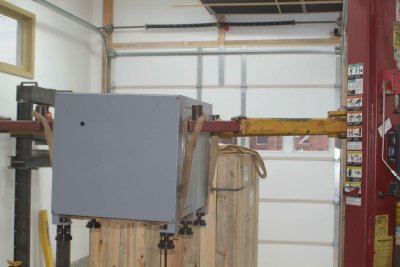
I adjusted the corner feet to be equal with the two centers a little short. Once the mill is in position I can level it more precisely. In any case, measuring with an electronic level after it was on the floor showed 1 degree off crosswise and 3 degrees lengthwise.
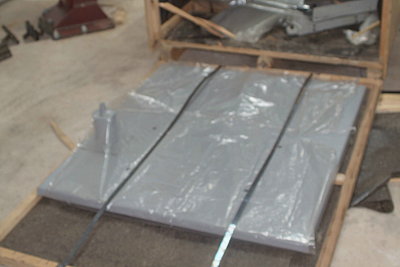
The chip pan is banded to one side of the mill crate.
With the sides and top of the crate removed, here's the mill as packed:
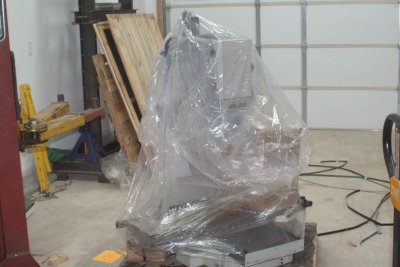
And with the packaging removed. Notice the steel bar that's protruding from the sides of the column. That's one I placed through the holes provided and that I will use to lift the mill off the pallet.
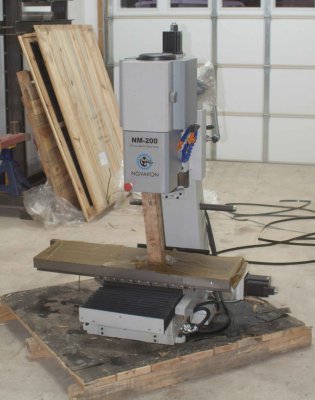
Here's the mill as seen from the rear:
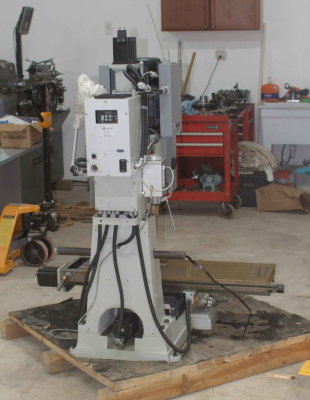
I'm going to hold off until Friday for the assembly, as a friend will be available to lend a hand. I suspect the mill will tilt when lifted off the pallet. There are two eyebolts on the front of the base casting that can be used to level it off. Once in the air, I'll maneuver the stand and chip pan underneath and lower it down.