Hi all,
Well, I've finally got my butt back in the workshop and started my next project. I am on leave all week so the plan was to spend 2 hours in the morning and 2 hours in the evening each day, the aim being a completed project.
After a bit of deliberation I've decided what I'm making.
Here are some of the materials:
Any ideas? This pic might give a better clue:
The wheel was an old casting I got many years ago and machined quite badly but never used it on anything. I thought I could probably put it to some use now so I set about trueing it up in the lathe.
Not quite finished, it'll need drilling and tapping for a grub screw.
That's all I got done today, I couldn't do the morning session due to other things getting in the way. I am going to do my best to make sure nothing else gets in the way as otherwise I definitely won't achieve my goal.
Nick
Well, I've finally got my butt back in the workshop and started my next project. I am on leave all week so the plan was to spend 2 hours in the morning and 2 hours in the evening each day, the aim being a completed project.
After a bit of deliberation I've decided what I'm making.
Here are some of the materials:
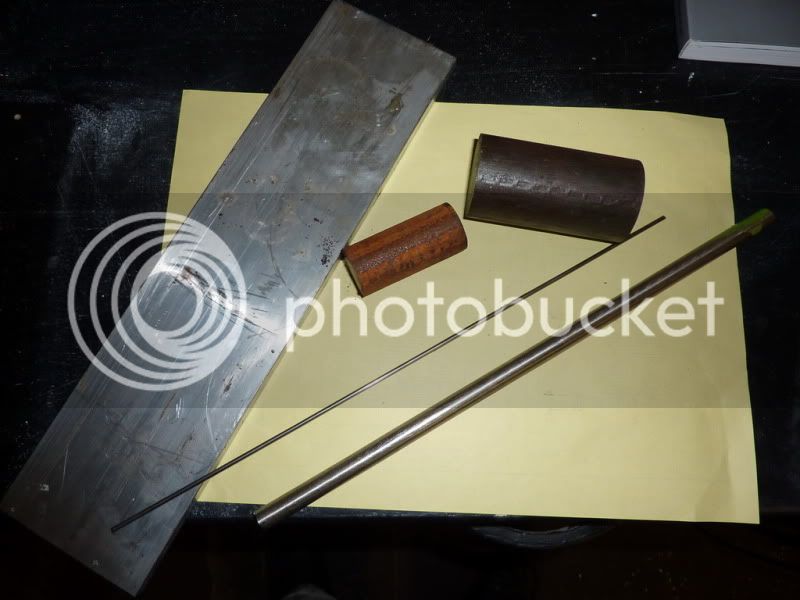
Any ideas? This pic might give a better clue:
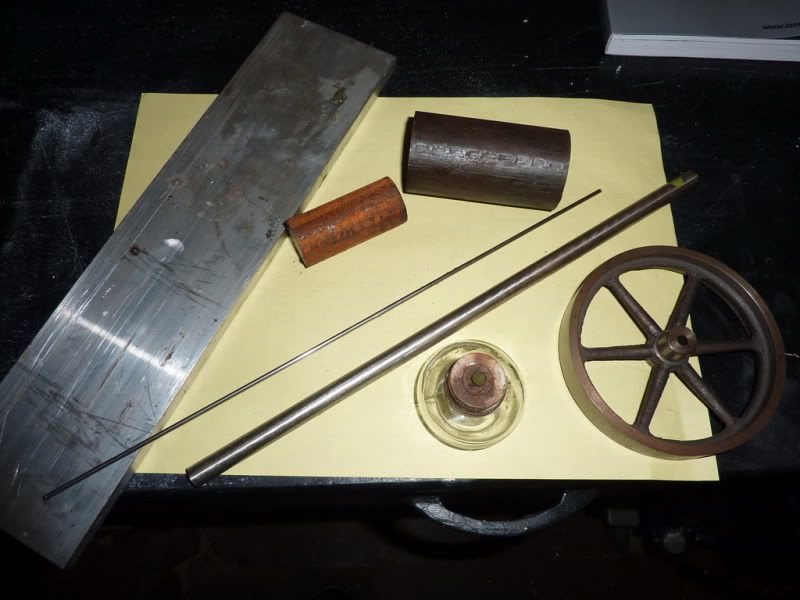
The wheel was an old casting I got many years ago and machined quite badly but never used it on anything. I thought I could probably put it to some use now so I set about trueing it up in the lathe.
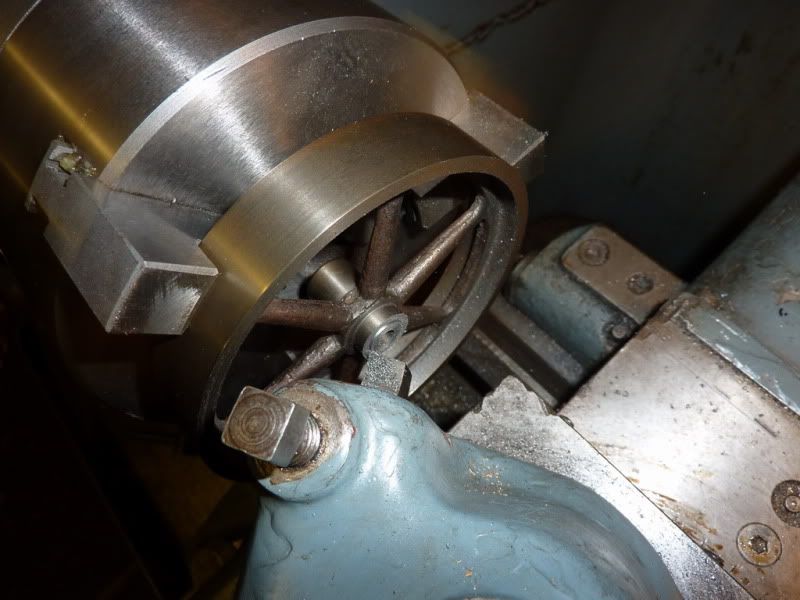
Not quite finished, it'll need drilling and tapping for a grub screw.
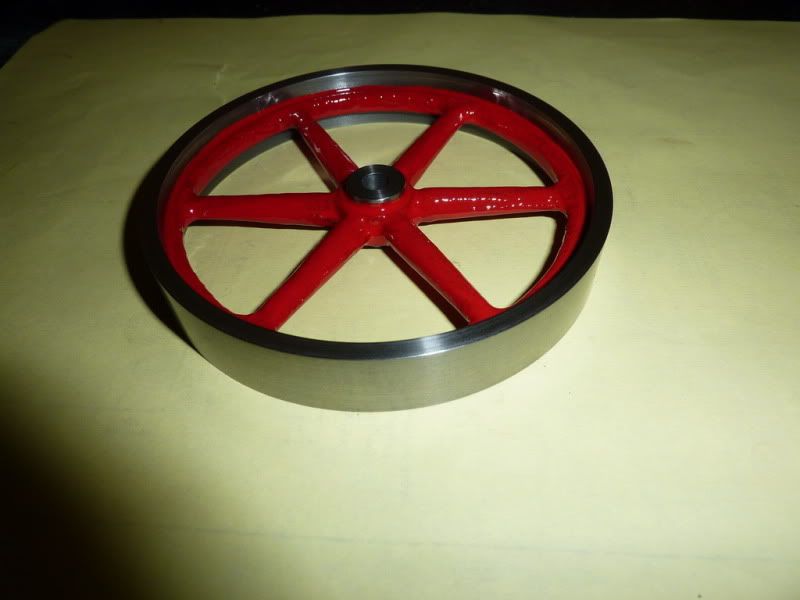
That's all I got done today, I couldn't do the morning session due to other things getting in the way. I am going to do my best to make sure nothing else gets in the way as otherwise I definitely won't achieve my goal.
Nick