As I've never used a milling machine before I wanted to do something simple and cheap in case I messed it up so I settled on making myself some T-Nuts.
All marked out.
First pass done.
First pass with the swarf brushed off.
Half way through the final pass.
Finished surface.
My thoughts after my first attempt at milling.
It's not as noisy or scary as I thought it would be. :big:
Preparation is everything.
I can see me fitting a DRO to this soon.
I now fully understand why people motorise the X axis, winding is tedious to say the least.
Unfortunately bolstered with my success I started on the other side and on the second pass I wound too fast and the endmill bit in and broke, as this is the only endmill I have that's my milling finished for the long weekend.
Not how I wanted it to end but it was a good learning experience anyway.
All marked out.
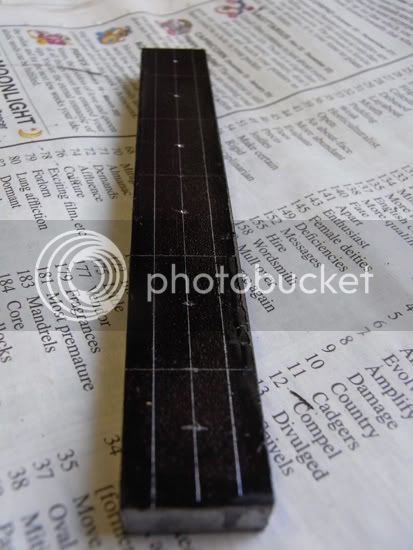
First pass done.
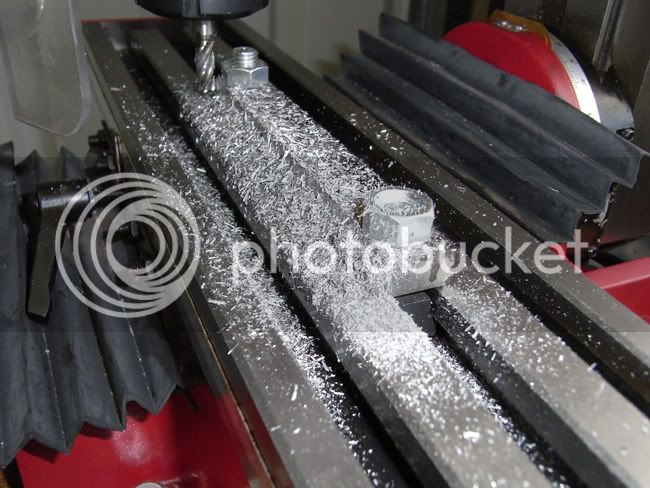
First pass with the swarf brushed off.
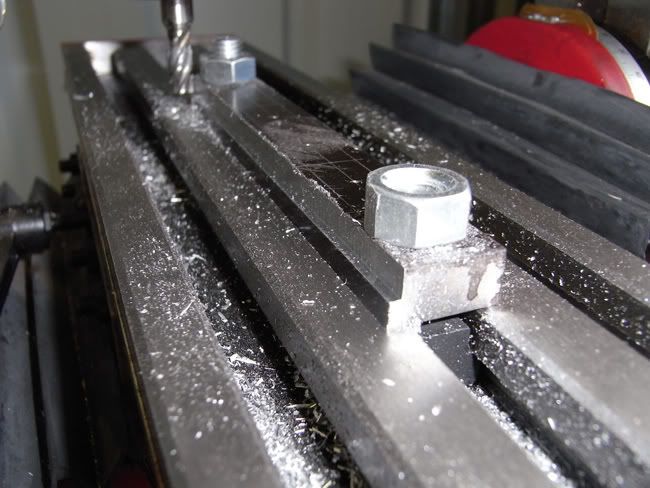
Half way through the final pass.
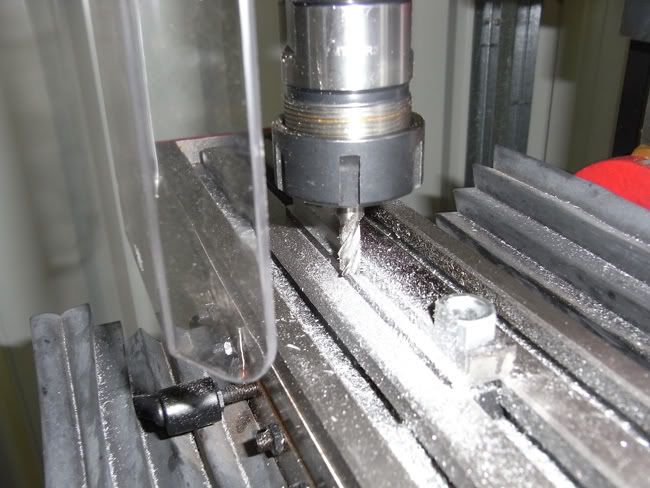
Finished surface.
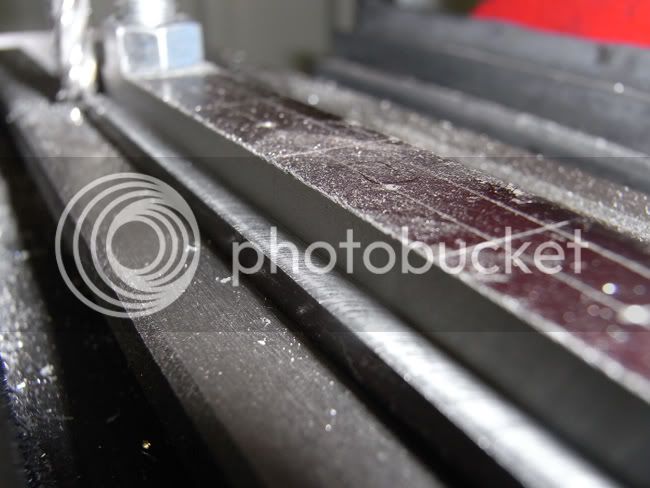
My thoughts after my first attempt at milling.
It's not as noisy or scary as I thought it would be. :big:
Preparation is everything.
I can see me fitting a DRO to this soon.
I now fully understand why people motorise the X axis, winding is tedious to say the least.
Unfortunately bolstered with my success I started on the other side and on the second pass I wound too fast and the endmill bit in and broke, as this is the only endmill I have that's my milling finished for the long weekend.
Not how I wanted it to end but it was a good learning experience anyway.