This is not a model engine stator (unless you ride a Harley) that went bad on me after 13,000 miles.
All the information I need for rewinding it is noted because this project may take a while to complete. I ordered a new Stator from the manufacturer through the dealer I purchased it from. Considering the quality of the made in China burned up stator I'm sure I'll be replacing it in about another 13,000 miles. I'll have a quality stator ready to go when that happens. A visual inspection shows a burned up coil and another in the process of burning up.
This is a 3 phase stator so when reading output voltage you must check across each of the 3 lines and note the voltage produced. In this case phase 1 reading was 30 volts, Phase 2 was 5 volts, and phase 3 was 21 volts. All the coils on phase 1 looked fine and had the correct voltage according to the manual. Phase 2 is obviously bad. The coil in the process of burning up was having an effect on the voltage output on phase 2.
As I was removing the wire I noted how many turns of wire were wrapped on each pole which was 35 and after removing the wire measured it length which came out to 36 feet.
During the unwinding process I carefully watched for anything that would have caused the stator to burn up. I found it. The plastic material was missing causing the coils nearest the output wires to burn up. Don't ask me why the shorted coils did not burn up! I've rewound many motors and alternators over the years and most burn up coils at the output connections. This is the reason you never rewind a single burned up pole or attempt to partially rewind any motor or alternator.
This is the stator core all cleaned up and ready for rewinding. I'll stop by the local motor rewind shop and purchase the necessary wire and insulting material to replace the cheap plastic crap they used. I've purchased stuff from them before. As long as it's something they would not do (and they would refuse to rewind this stator) they will sell the wire and insulating material necessary to do the job.
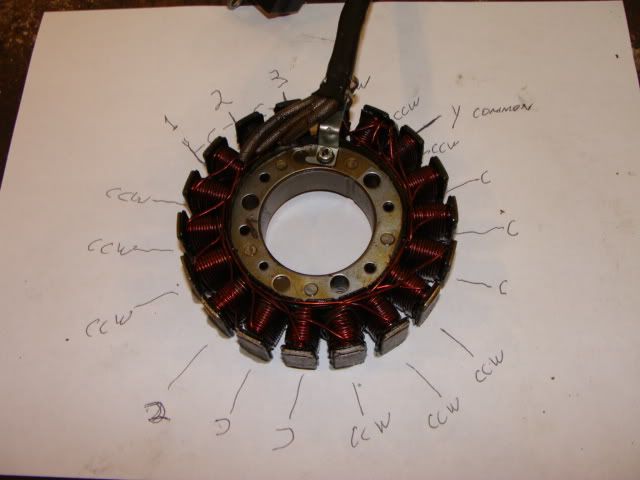
All the information I need for rewinding it is noted because this project may take a while to complete. I ordered a new Stator from the manufacturer through the dealer I purchased it from. Considering the quality of the made in China burned up stator I'm sure I'll be replacing it in about another 13,000 miles. I'll have a quality stator ready to go when that happens. A visual inspection shows a burned up coil and another in the process of burning up.
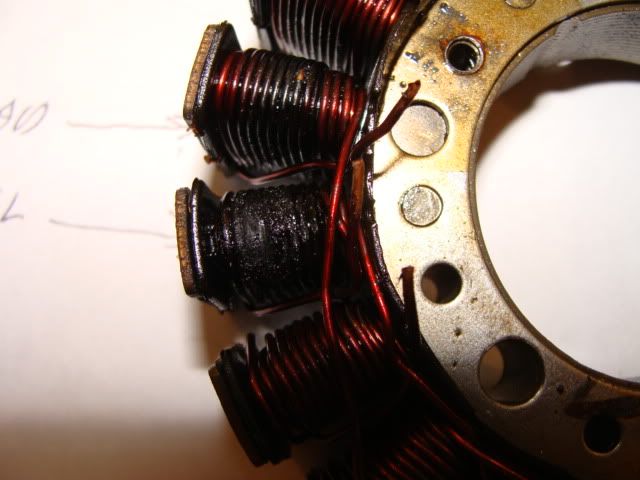
This is a 3 phase stator so when reading output voltage you must check across each of the 3 lines and note the voltage produced. In this case phase 1 reading was 30 volts, Phase 2 was 5 volts, and phase 3 was 21 volts. All the coils on phase 1 looked fine and had the correct voltage according to the manual. Phase 2 is obviously bad. The coil in the process of burning up was having an effect on the voltage output on phase 2.
As I was removing the wire I noted how many turns of wire were wrapped on each pole which was 35 and after removing the wire measured it length which came out to 36 feet.
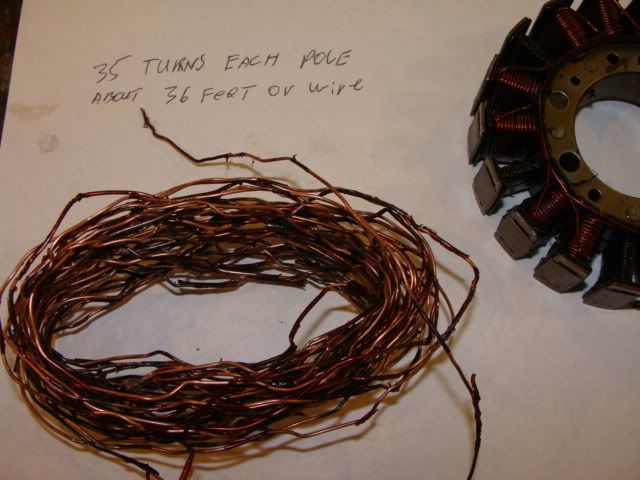
During the unwinding process I carefully watched for anything that would have caused the stator to burn up. I found it. The plastic material was missing causing the coils nearest the output wires to burn up. Don't ask me why the shorted coils did not burn up! I've rewound many motors and alternators over the years and most burn up coils at the output connections. This is the reason you never rewind a single burned up pole or attempt to partially rewind any motor or alternator.
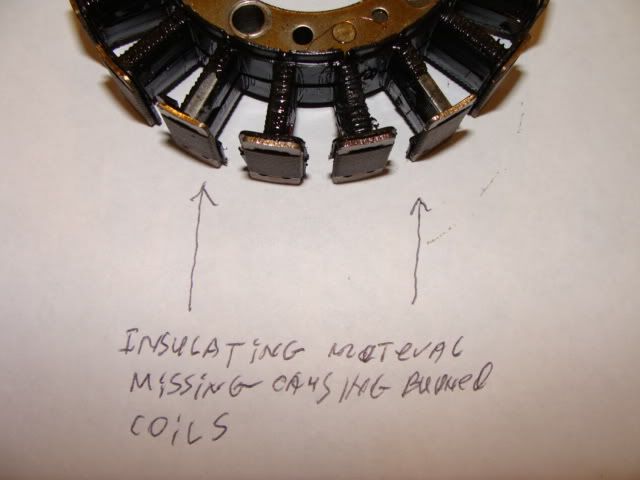
This is the stator core all cleaned up and ready for rewinding. I'll stop by the local motor rewind shop and purchase the necessary wire and insulting material to replace the cheap plastic crap they used. I've purchased stuff from them before. As long as it's something they would not do (and they would refuse to rewind this stator) they will sell the wire and insulating material necessary to do the job.
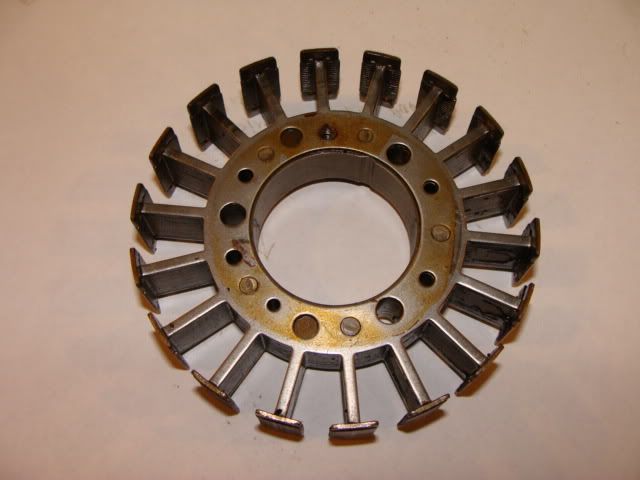