BobWarfield
Well-Known Member
- Joined
- Dec 27, 2007
- Messages
- 1,151
- Reaction score
- 1
It's not quite done yet, but I thought I'd get started posting since Divided He ad is trying to do something similar. I won't post everything here, it would be two long. The gory detail can be had on my web site here:
http://www.cnccookbook.com/CCColletChuck.htm
What follows are some highlights.
Since it's a collet chuck, I wanted to take extra care around accuracy. 5C collets can be really slick and accurate. We'll see how it turns out.
We start with a lump of sawn cast iron and the chuck:
One of the great difficulties is holding a big workpiece like that in a small lathe. Many have followed Steve Bedair's method of using a bolt as an arbor. I tried that on my first backplate and it chattered and misbehaved like heck, so I resolved to make use of my mill to enable me to machine a passable but (I expected) not nearly accurate enough mounting to enable it to be held securely for more precise machining on the lathe itself.
Job 1 is therefore to face the cast iron on both sides with my indexable face mill:
This iron was a little tougher to machine than other cast iron I've dealt with. Not sure why, but all's well that ends well.
Next, I made a set of M10 transfer screws (process described elsewhere here and on my web site):
What goes in those 3 holes is sort of a faux cam lock as I call it. It's a set of barrels with nuts that are tightened. I quite like the system as I don't have to worry about the drawbacks of a threaded spindle and it is very rigid and accurate.
With the aid of the transfer screws, I was able to get a set of punch marks in place:
<continued>
http://www.cnccookbook.com/CCColletChuck.htm
What follows are some highlights.
Since it's a collet chuck, I wanted to take extra care around accuracy. 5C collets can be really slick and accurate. We'll see how it turns out.
We start with a lump of sawn cast iron and the chuck:

One of the great difficulties is holding a big workpiece like that in a small lathe. Many have followed Steve Bedair's method of using a bolt as an arbor. I tried that on my first backplate and it chattered and misbehaved like heck, so I resolved to make use of my mill to enable me to machine a passable but (I expected) not nearly accurate enough mounting to enable it to be held securely for more precise machining on the lathe itself.
Job 1 is therefore to face the cast iron on both sides with my indexable face mill:
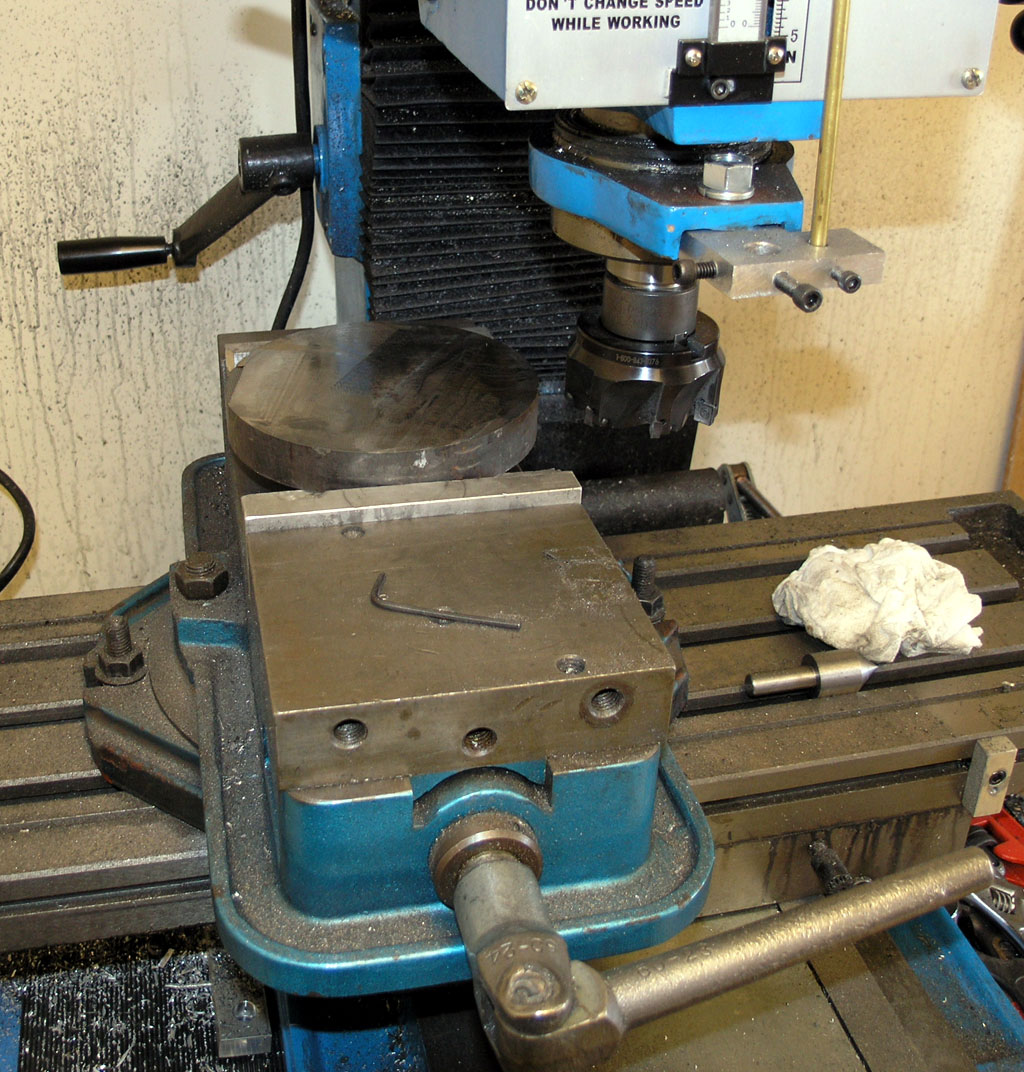
This iron was a little tougher to machine than other cast iron I've dealt with. Not sure why, but all's well that ends well.
Next, I made a set of M10 transfer screws (process described elsewhere here and on my web site):
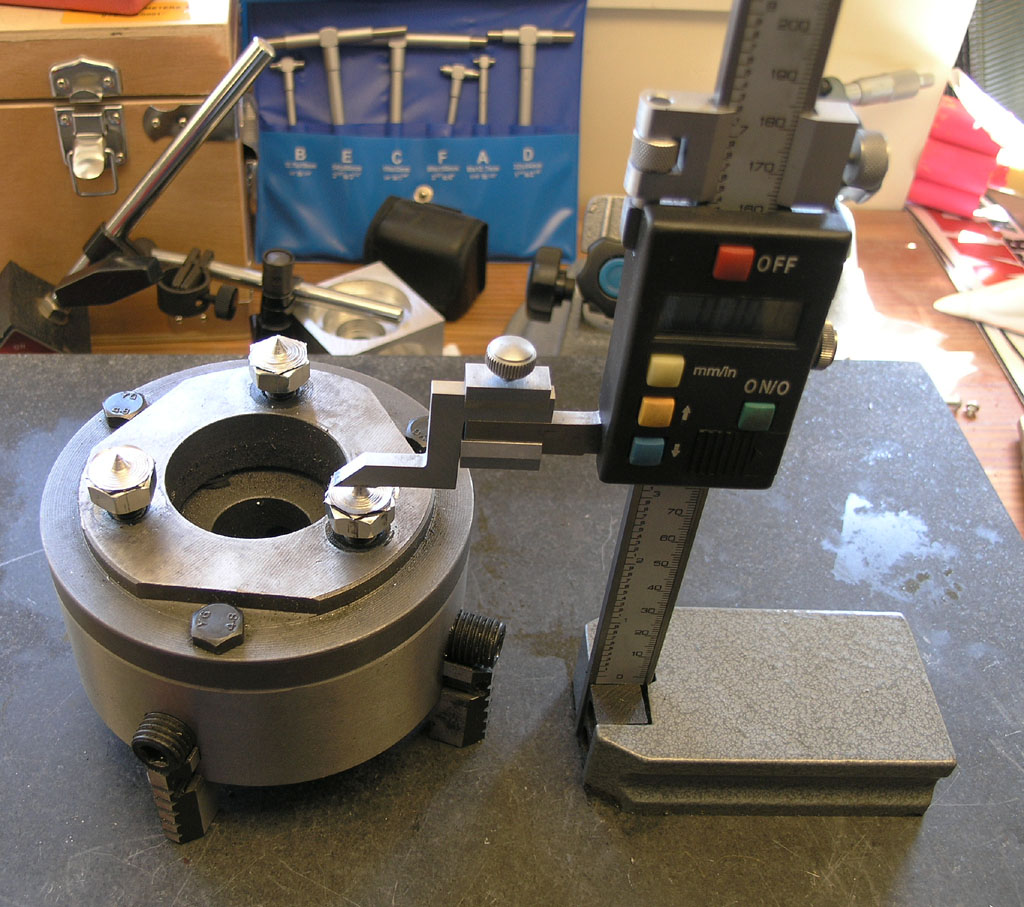
What goes in those 3 holes is sort of a faux cam lock as I call it. It's a set of barrels with nuts that are tightened. I quite like the system as I don't have to worry about the drawbacks of a threaded spindle and it is very rigid and accurate.
With the aid of the transfer screws, I was able to get a set of punch marks in place:
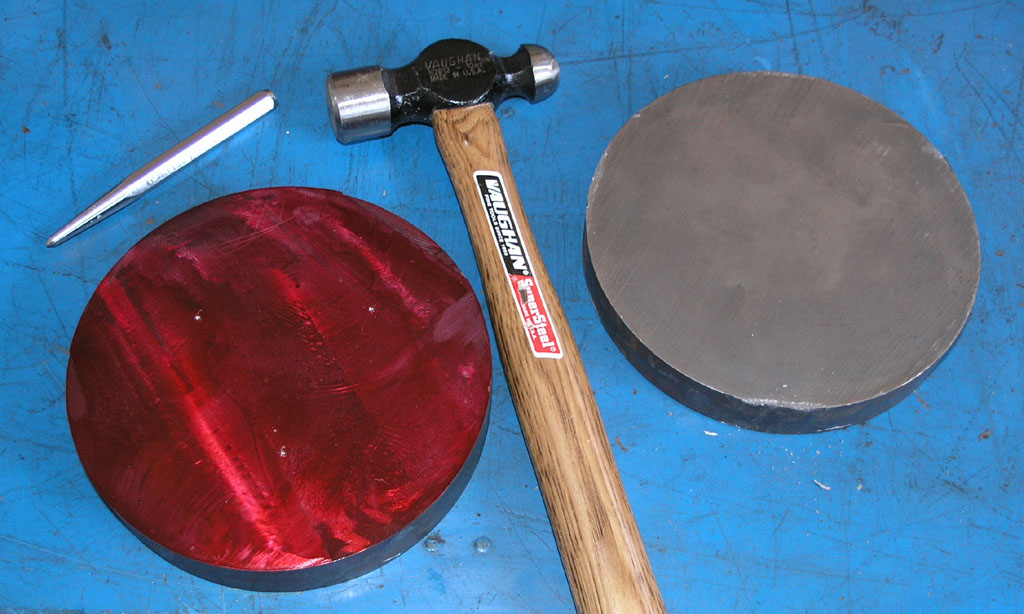
<continued>