imagineering
Well-Known Member
- Joined
- Dec 6, 2010
- Messages
- 96
- Reaction score
- 14
Hi Guys.
I've decided to separate my Loco and Beam Engine threads & copy over the text from my original Thread.
Peter, (Doubletop), has persuade me to put up a few photos of my version of Gerry Dykstra's Beam Engine.
Double Sized, in Metric, (thanks Ken), with Frames timbered in Jarrah.
The Brasses were drilled & profiled on my Sieg CNC'd SX3 Mill.
The Brass Braces are 'nailed' on using cut down HO-Rail Track Pins.
This will be a long work in progress, as I have now got a 7 1/4 Gauge Live Steam Loco sitting in parts in the Workshop needing some TLC. (refer the other 'Imagineering's Stuff' Thread).
Murray
I've decided to separate my Loco and Beam Engine threads & copy over the text from my original Thread.
Peter, (Doubletop), has persuade me to put up a few photos of my version of Gerry Dykstra's Beam Engine.
Double Sized, in Metric, (thanks Ken), with Frames timbered in Jarrah.
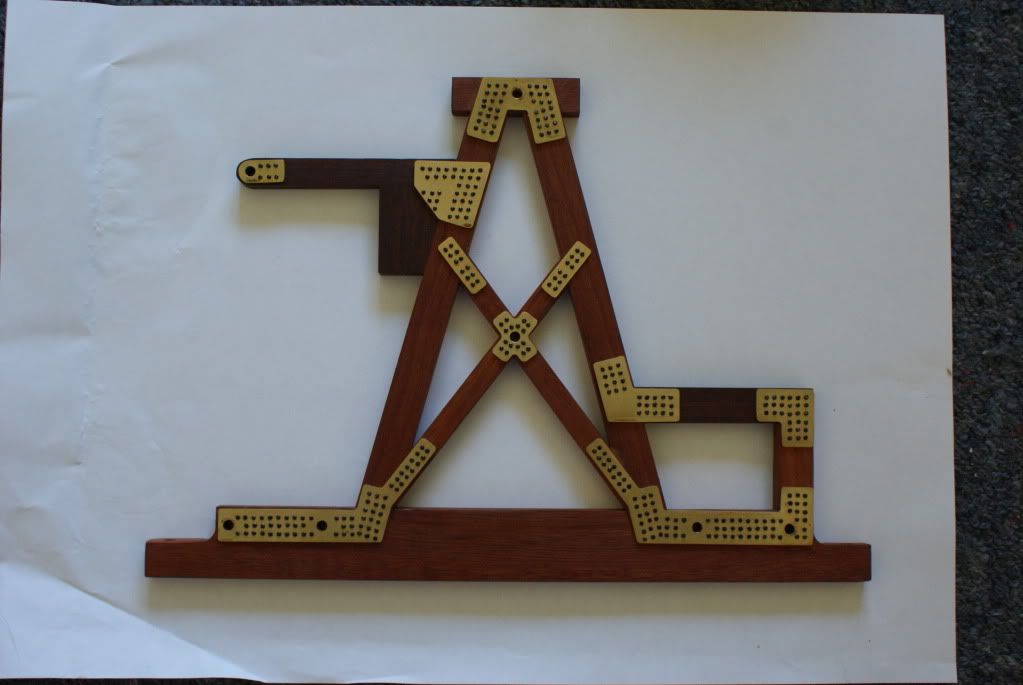
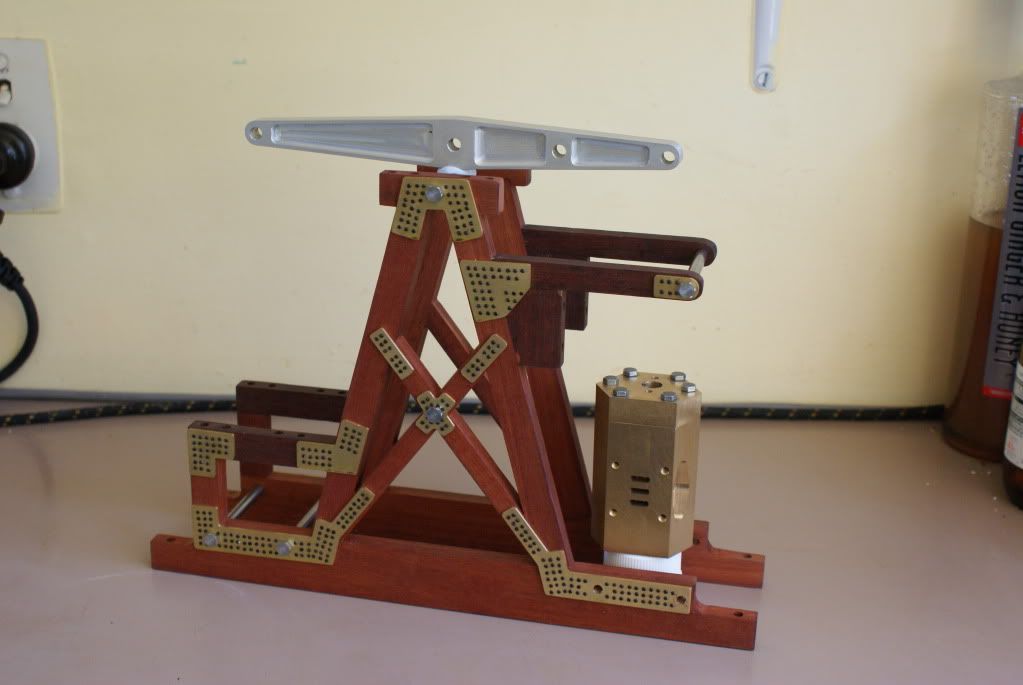
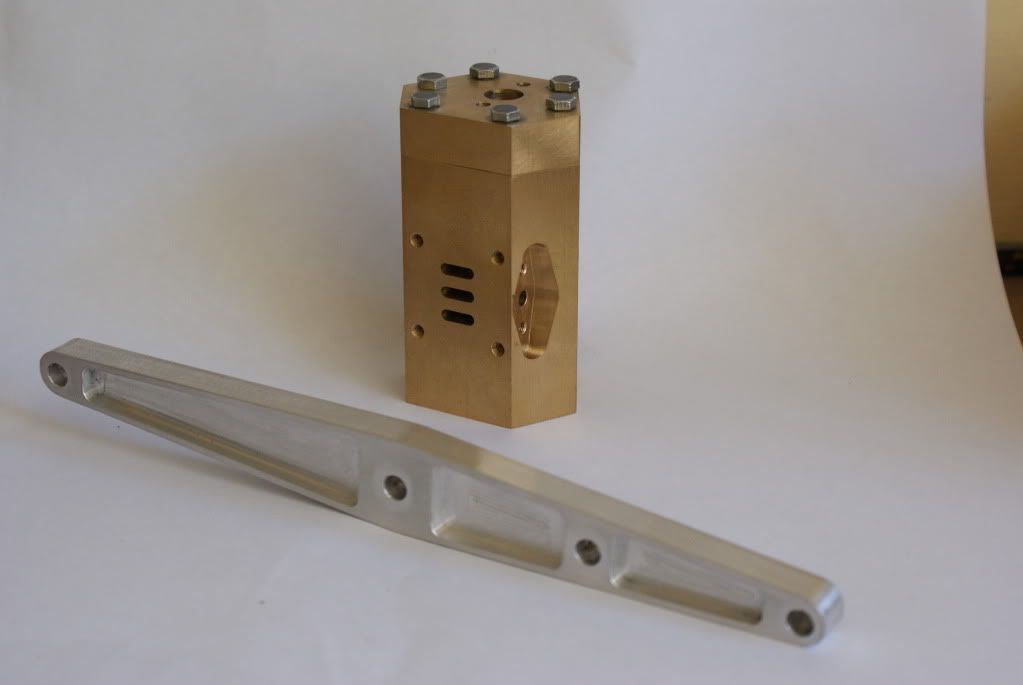
The Brasses were drilled & profiled on my Sieg CNC'd SX3 Mill.
The Brass Braces are 'nailed' on using cut down HO-Rail Track Pins.
This will be a long work in progress, as I have now got a 7 1/4 Gauge Live Steam Loco sitting in parts in the Workshop needing some TLC. (refer the other 'Imagineering's Stuff' Thread).
Murray