BobWarfield
Well-Known Member
- Joined
- Dec 27, 2007
- Messages
- 1,151
- Reaction score
- 1
I still remember when Frank Ford showed that huge lathe tool that he just cut a dovetail in and dropped it on his QCTP. What a clever idea!
Now here is a guy that built the biggest darned boring bar I've ever seen using a similar notion:
I love this kind of thing! I don't know why, easily amused I guess.
The original thread is over on PM: http://www.practicalmachinist.com/vb/showthread.php?t=153603
Cheers,
BW
Now here is a guy that built the biggest darned boring bar I've ever seen using a similar notion:
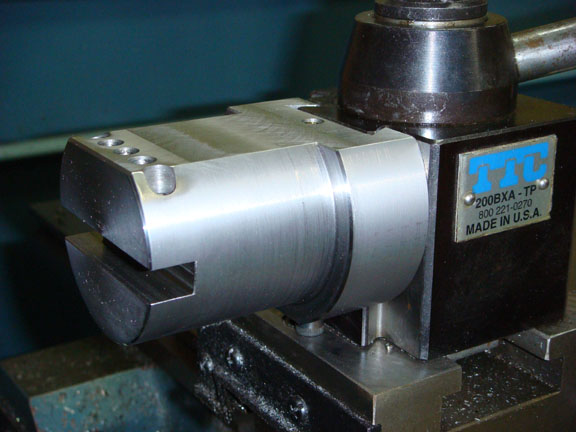
I love this kind of thing! I don't know why, easily amused I guess.
The original thread is over on PM: http://www.practicalmachinist.com/vb/showthread.php?t=153603
Cheers,
BW