Hello Everyone.
As a first time poster I'd like to say thanks to everyone for such a great message board. I'm really enjoying reading and seeing everyones machining related stuff.
I'd like to ask for a little help if you don't mind ?
I've got a 9x19 lathe that I've been using to make a few odds and sods. Nothing special. I'm limited to space/budget at the moment so decided to purchase a milling head (for a very reasonable sum) that i can use on the lathe. It's a 3phase unit so I'm going to need an inverter, but first i need to get the damn thing mounted.
This is where I'd like a little advise. As you can see from the picture I've got the milling head mocked up onto the lathe. Things look OK so far. It's the alignment of the mill spindle axis perpendicular to the cross slide that I'm thinking about. Maybe i could mount a large disc on a 2mt arbour for the mill head. insert the disc/2mt arbour into the mill head and lower the head till the disc is on the cross slide. Bolt the disc to the slide, allow the mill head column to "float" whilst doing this, so that when completed i can then mark and drill the mounting holes in the correct position.
Here is a pic of the milling head mocked up on the lathe
Here you can see the angle bracket (faces flycut to be 90deg ) that will tie the milling head/lathe/support plate together
Can anyone think of a better/simpler/more accurate way of doing this ?
I'll be making a spigot for the base of the column to sit on its will be clamped by the column locking bolts thus securing the mill column to the base plate, and the plate is secured to the lathe via the angle bracket.
Comments ?
Cheers
Pete.
As a first time poster I'd like to say thanks to everyone for such a great message board. I'm really enjoying reading and seeing everyones machining related stuff.
I'd like to ask for a little help if you don't mind ?
I've got a 9x19 lathe that I've been using to make a few odds and sods. Nothing special. I'm limited to space/budget at the moment so decided to purchase a milling head (for a very reasonable sum) that i can use on the lathe. It's a 3phase unit so I'm going to need an inverter, but first i need to get the damn thing mounted.
This is where I'd like a little advise. As you can see from the picture I've got the milling head mocked up onto the lathe. Things look OK so far. It's the alignment of the mill spindle axis perpendicular to the cross slide that I'm thinking about. Maybe i could mount a large disc on a 2mt arbour for the mill head. insert the disc/2mt arbour into the mill head and lower the head till the disc is on the cross slide. Bolt the disc to the slide, allow the mill head column to "float" whilst doing this, so that when completed i can then mark and drill the mounting holes in the correct position.
Here is a pic of the milling head mocked up on the lathe
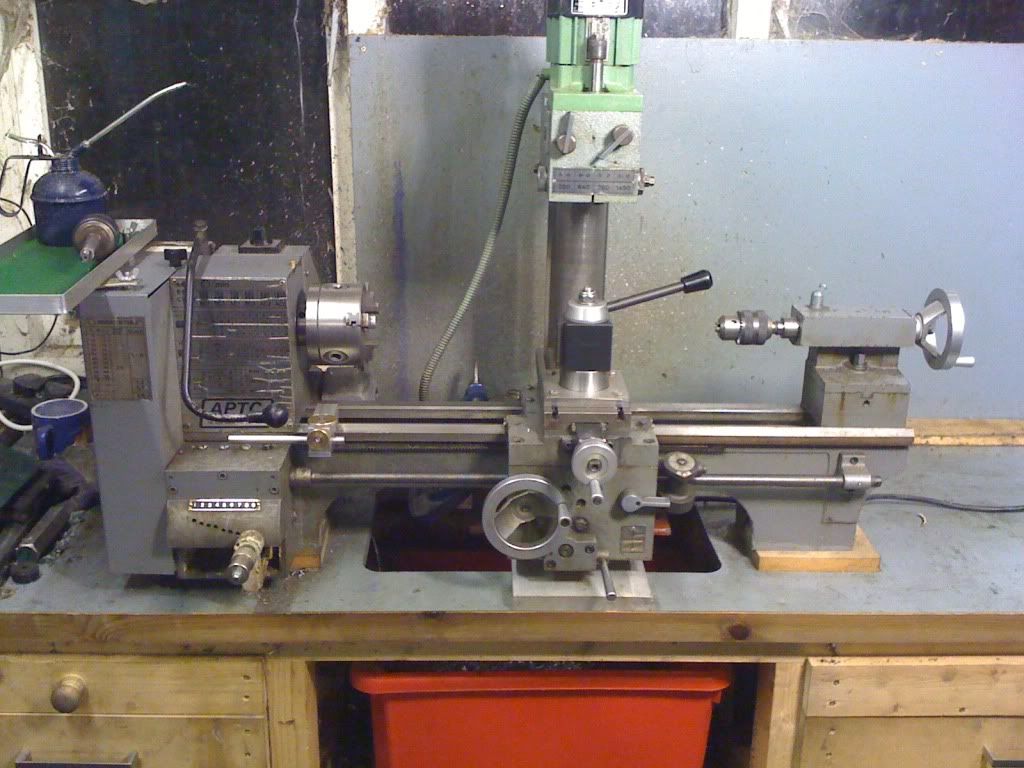
Here you can see the angle bracket (faces flycut to be 90deg ) that will tie the milling head/lathe/support plate together
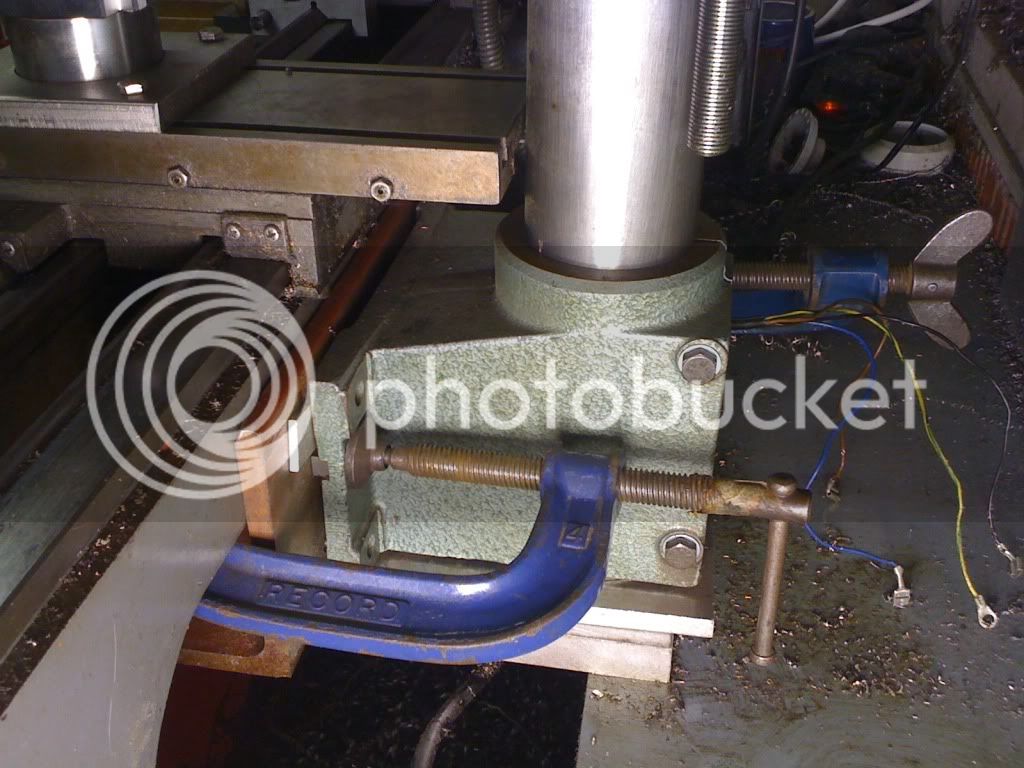
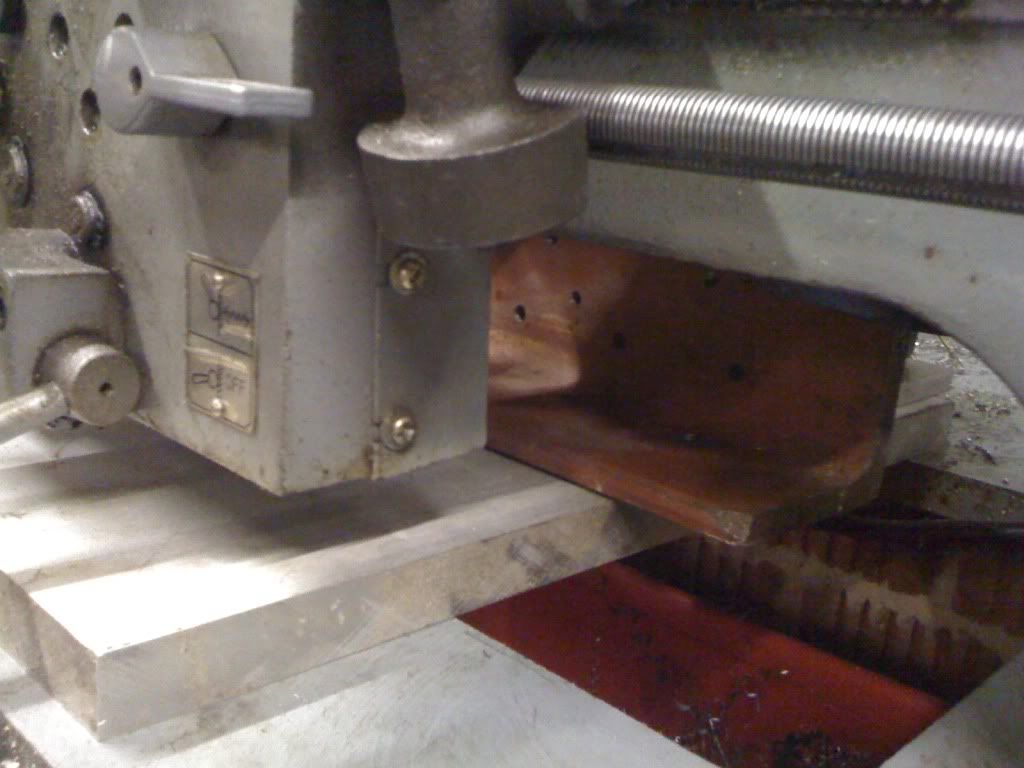
Can anyone think of a better/simpler/more accurate way of doing this ?
I'll be making a spigot for the base of the column to sit on its will be clamped by the column locking bolts thus securing the mill column to the base plate, and the plate is secured to the lathe via the angle bracket.
Comments ?
Cheers
Pete.