im about to start rebuilding my 12x36" lathe cabinet stand and i want to fit a foot brake and coolant pump has anyone had any luck doing this? i was thinking of using a disc brake from a push bike the cable type and a simple pivoting foot leaver
i have my stock all cut up it just needs some cleaning up with a grinder then the lathe is coming down and ill start work hopefully by the end it should look like this
i have my stock all cut up it just needs some cleaning up with a grinder then the lathe is coming down and ill start work hopefully by the end it should look like this
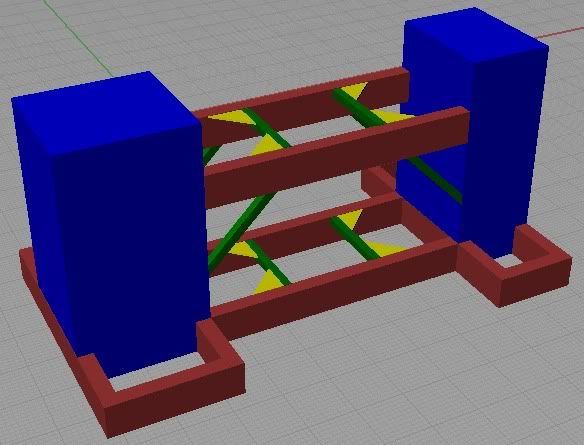
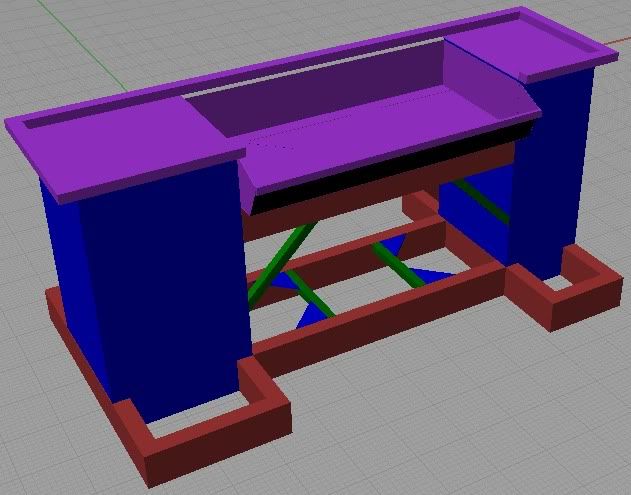