Well it has finally happened - I have started my first attempt at a model after only 30yrs of being involved with steam (I started driving a traction engine with my grandfather at the age of 5).
Actually I have several models in my collection - all of which were purchased as either not complete or run down & I have completed/restored them over the years. The only other engine I can claim to be my own is one built for odd and ends many years ago (with the assistance of my Grandfather).
However, since buying my new Hare-Forbes AL60/HM10 lathe/mill combo prior to xmas (Grizzly 0516/Seig C6 equivalent) I have been keen to start something from scratch & try to work to drawings rather than the trial and error approach.
Originally I was going to attempt Elmers wooden Grashopper engine as I though wood could be easier/cheaper to work with but I am still unable to find a source of the 7/8" brass tubing required for the cylinder. However, scrounging around my boxes of odd & ends I found enough material for the beam engine.
Below are photos from the first days work. Yes it's not a lot of progress for a day but milling the 1-1/4" x 3/4" alluminium bar to 5/8" x 5/8" given my complete lack of experience on a mill did prove to be a learning exercise on possible feed rates, cut depths, etc (plus why you need a proper mill vice and not a modified drill vice).
I have made some minor changes already - I have replace threads where possible with 1/8" Whitworth as I can get plenty of 1/8 stainless bolts from the local hardware stores (even though Australia has been metric for how long???) but UNF threads aren't so easy.
It may be some time before I get back into the shop & at this rate of progress the complete engine may take quite a while to finish, but at least it has moved from my "Projects to do list" to the marginally shorter "projects to finish" list.
Tony
Actually I have several models in my collection - all of which were purchased as either not complete or run down & I have completed/restored them over the years. The only other engine I can claim to be my own is one built for odd and ends many years ago (with the assistance of my Grandfather).
However, since buying my new Hare-Forbes AL60/HM10 lathe/mill combo prior to xmas (Grizzly 0516/Seig C6 equivalent) I have been keen to start something from scratch & try to work to drawings rather than the trial and error approach.
Originally I was going to attempt Elmers wooden Grashopper engine as I though wood could be easier/cheaper to work with but I am still unable to find a source of the 7/8" brass tubing required for the cylinder. However, scrounging around my boxes of odd & ends I found enough material for the beam engine.
Below are photos from the first days work. Yes it's not a lot of progress for a day but milling the 1-1/4" x 3/4" alluminium bar to 5/8" x 5/8" given my complete lack of experience on a mill did prove to be a learning exercise on possible feed rates, cut depths, etc (plus why you need a proper mill vice and not a modified drill vice).
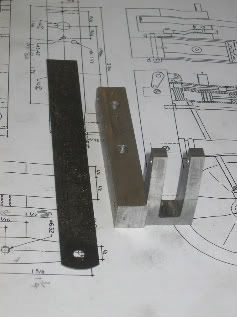
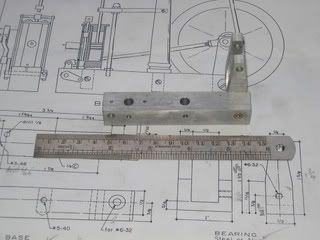
I have made some minor changes already - I have replace threads where possible with 1/8" Whitworth as I can get plenty of 1/8 stainless bolts from the local hardware stores (even though Australia has been metric for how long???) but UNF threads aren't so easy.
It may be some time before I get back into the shop & at this rate of progress the complete engine may take quite a while to finish, but at least it has moved from my "Projects to do list" to the marginally shorter "projects to finish" list.
Tony