- Joined
- Aug 25, 2007
- Messages
- 3,890
- Reaction score
- 715
Yet another improvement for my mini lathe. I have a number of ER20 collets and decided a collet chuck for my mini lathe would be nice. I would have preferred an ER32, but ER20 was what I had.
I started with a 3" diameter piece of 12L14.
I used my Logan 12" lathe so I could remove the metal faster. I left the nose about .050" oversize so I could finish it in place on my minilathe.
Next I parted off the piece turned it around and chucked it by the nose so I could cut the recess in the back. Then I drilled and tapped the mounting holes 1/4-28. I used my rotary table to locate and drill the holes.
Next I mounted the blank on the mini lathe so I could cut the threads. I had never used the min lathe to cut threads, so had to go through some setup and make some bushings to hold the banjo. Here is the change gear set up. I was able to approximate the 1.5mm thread pitch by using a 60 tooth gear on the lead screw and a 57 tooth as the driving gear. These two gears just happened to be in the gears included with the lathe and gave me a ratio of .945 : 1 with a 16 tooth per inch lead screw.
Here's the threaded nose piece.
I bored a half inch hole through the center of the chuck, then set up the compound to cut an 8 degree tape in the nose piece. Here is the lash up I used to set the angle...
And here I'm ready to start boring...
Here's the finished taper bored...
And here's the finished chuck with a 1/2" rod chucked in it.
I made the nose a little longer than need be, but it turns out I can't get the carriage any closer to the head stock so it turned out good. I also want to replace the hex head bolts with button head socket head screws... should be a little less dangerous.
Chuck
I started with a 3" diameter piece of 12L14.
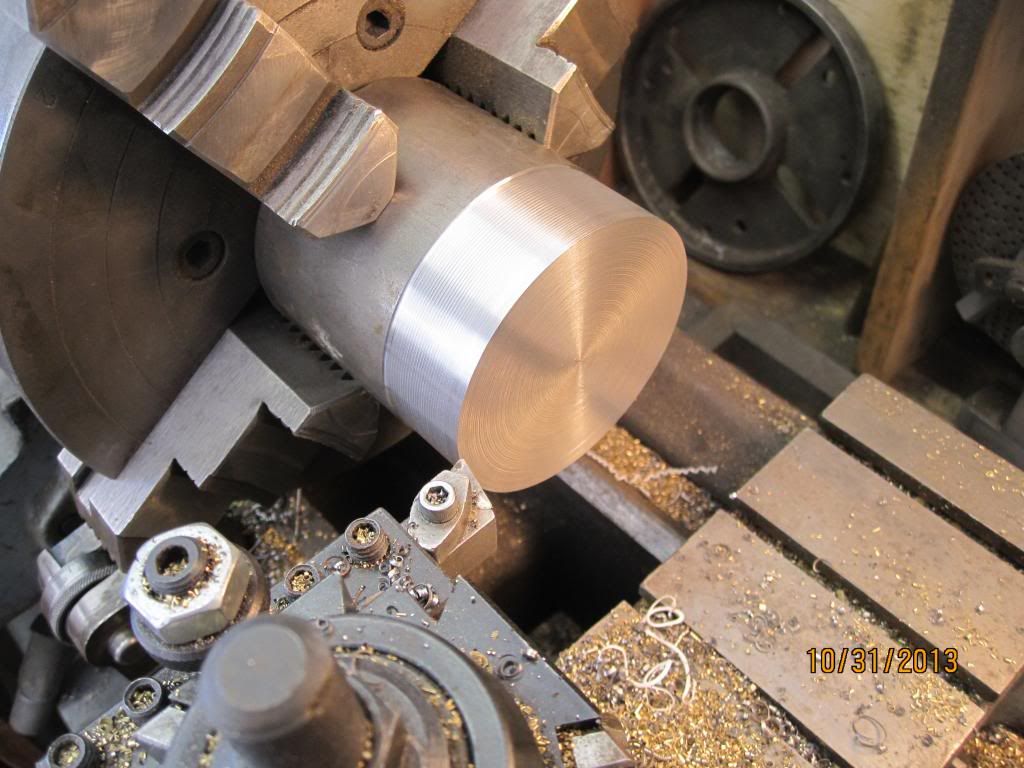
I used my Logan 12" lathe so I could remove the metal faster. I left the nose about .050" oversize so I could finish it in place on my minilathe.
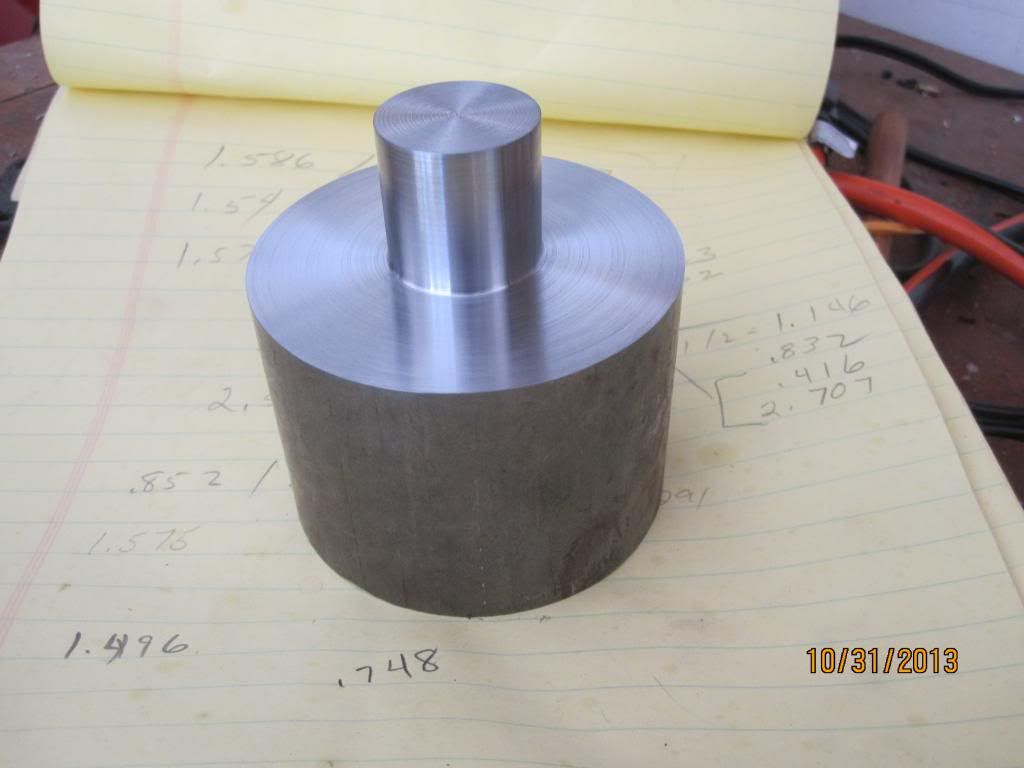
Next I parted off the piece turned it around and chucked it by the nose so I could cut the recess in the back. Then I drilled and tapped the mounting holes 1/4-28. I used my rotary table to locate and drill the holes.

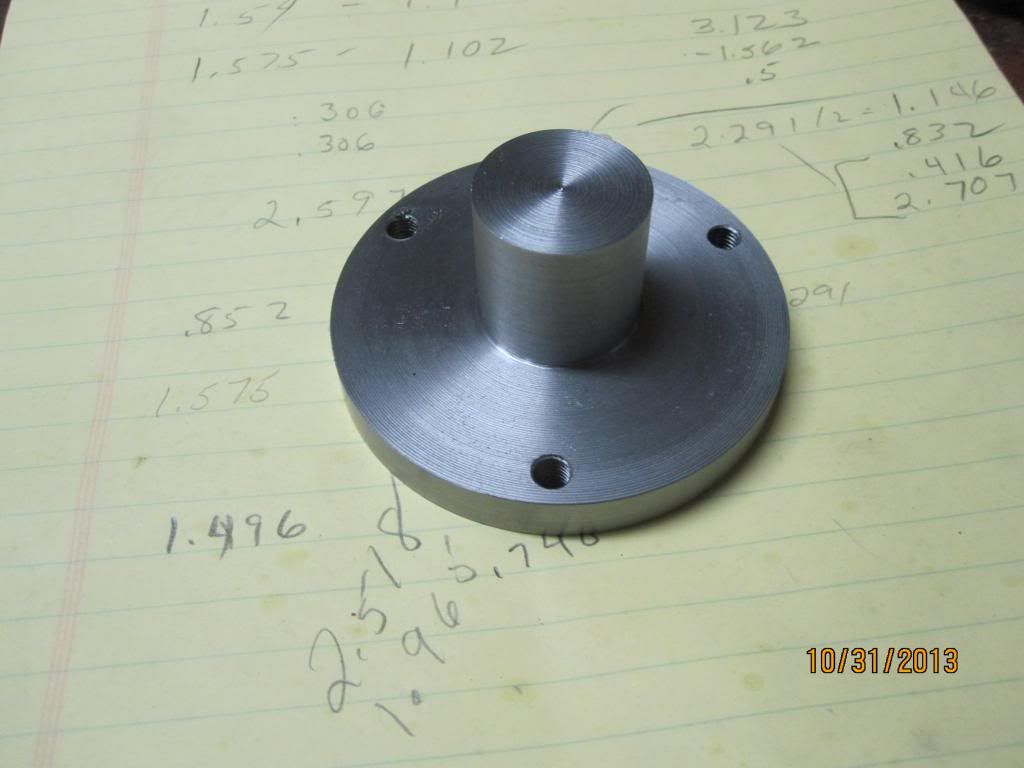
Next I mounted the blank on the mini lathe so I could cut the threads. I had never used the min lathe to cut threads, so had to go through some setup and make some bushings to hold the banjo. Here is the change gear set up. I was able to approximate the 1.5mm thread pitch by using a 60 tooth gear on the lead screw and a 57 tooth as the driving gear. These two gears just happened to be in the gears included with the lathe and gave me a ratio of .945 : 1 with a 16 tooth per inch lead screw.

Here's the threaded nose piece.

I bored a half inch hole through the center of the chuck, then set up the compound to cut an 8 degree tape in the nose piece. Here is the lash up I used to set the angle...

And here I'm ready to start boring...

Here's the finished taper bored...

And here's the finished chuck with a 1/2" rod chucked in it.
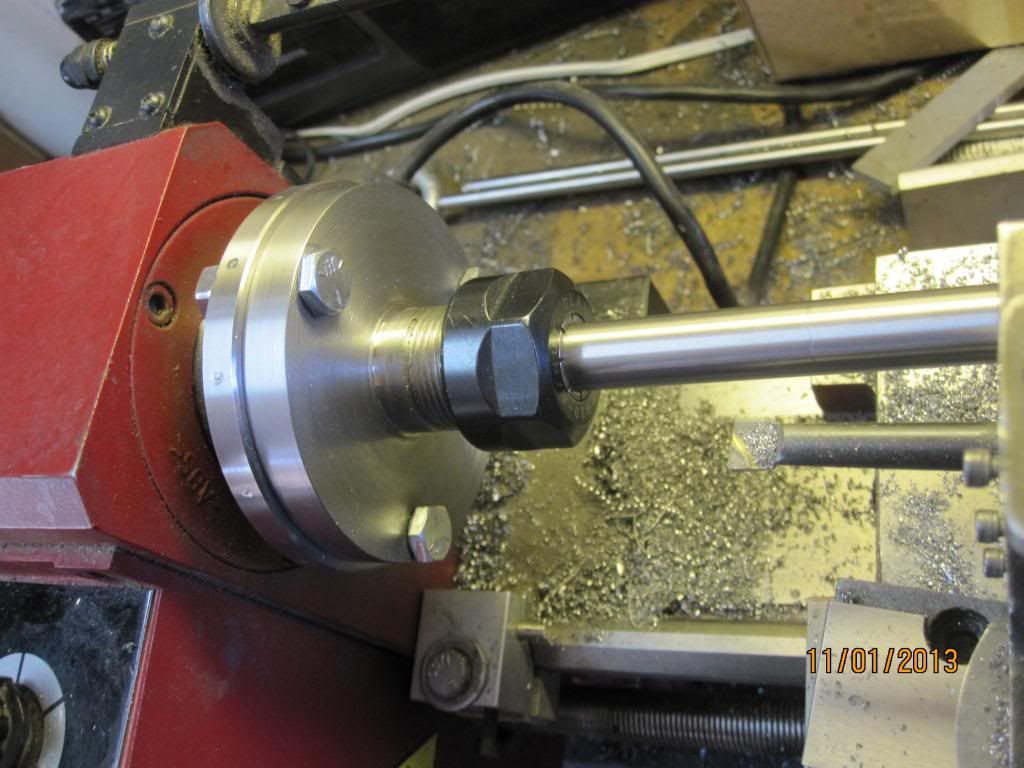
I made the nose a little longer than need be, but it turns out I can't get the carriage any closer to the head stock so it turned out good. I also want to replace the hex head bolts with button head socket head screws... should be a little less dangerous.
Chuck