- Joined
- Feb 25, 2008
- Messages
- 464
- Reaction score
- 5
Hi & help please.
I'm attempting to drill copper and having less than satisfactory results. Note the mushroomed entry and the stretched out exit.
I don't know what the alloy is, but it's from a 4" copper sweat coupling. The holes are 3/32" and were drilled with a standard HSS jobbers bit (brand new). Speed was 4250 rpm with Tapmatic Gold fluid brushed on for cooling. I kind of peck drilled (about four pecks to get through the 1/8" wall) and applied coolant between each peck. If I didn't peck, the bit just quit cutting.
I don't have much extra material to experiment on and I have a lot more holes to drill, so I'm hoping someone can point me in the right direction.
Regards,
Dennis
I'm attempting to drill copper and having less than satisfactory results. Note the mushroomed entry and the stretched out exit.
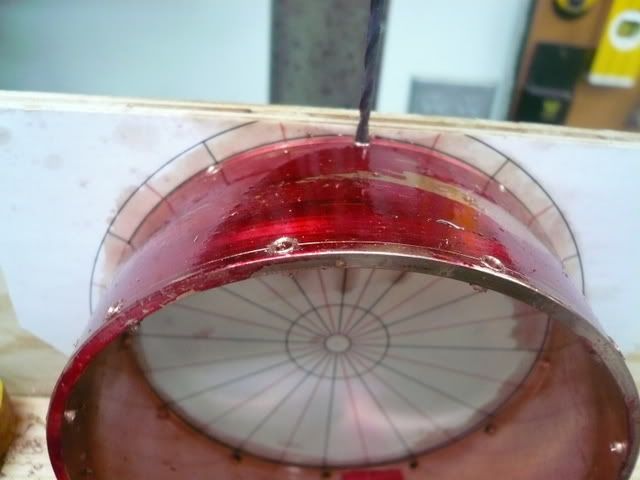
I don't know what the alloy is, but it's from a 4" copper sweat coupling. The holes are 3/32" and were drilled with a standard HSS jobbers bit (brand new). Speed was 4250 rpm with Tapmatic Gold fluid brushed on for cooling. I kind of peck drilled (about four pecks to get through the 1/8" wall) and applied coolant between each peck. If I didn't peck, the bit just quit cutting.
I don't have much extra material to experiment on and I have a lot more holes to drill, so I'm hoping someone can point me in the right direction.
Regards,
Dennis