DICKEYBIRD
Well-Known Member
- Joined
- Sep 27, 2007
- Messages
- 653
- Reaction score
- 46
Here's a shop-made gauge for accurately setting lathe tools on center made from scrap aluminum, ½ drill rod & an ebay dial indicator. It helps to quickly & easily set the tool on center within a thou (or less) on any lathe. I used a short travel, small dial indicator so it would be compact enough to clear the ways on my 8 swing lathes.
Its calibrated with a .250 dowel pin that slides in & out of a close fitting reamed hole in the center of the shaft. The indicator dial is set & locked so that the needle sits on zero with the dial tip extended exactly .125 It works great and is very consistent. The only variable is making sure its set at 90 degrees to the carriage but thats pretty easy using an accurate square. I thought about adding a level but I think the square is more accurate.
Its calibrated with a .250 dowel pin that slides in & out of a close fitting reamed hole in the center of the shaft. The indicator dial is set & locked so that the needle sits on zero with the dial tip extended exactly .125 It works great and is very consistent. The only variable is making sure its set at 90 degrees to the carriage but thats pretty easy using an accurate square. I thought about adding a level but I think the square is more accurate.
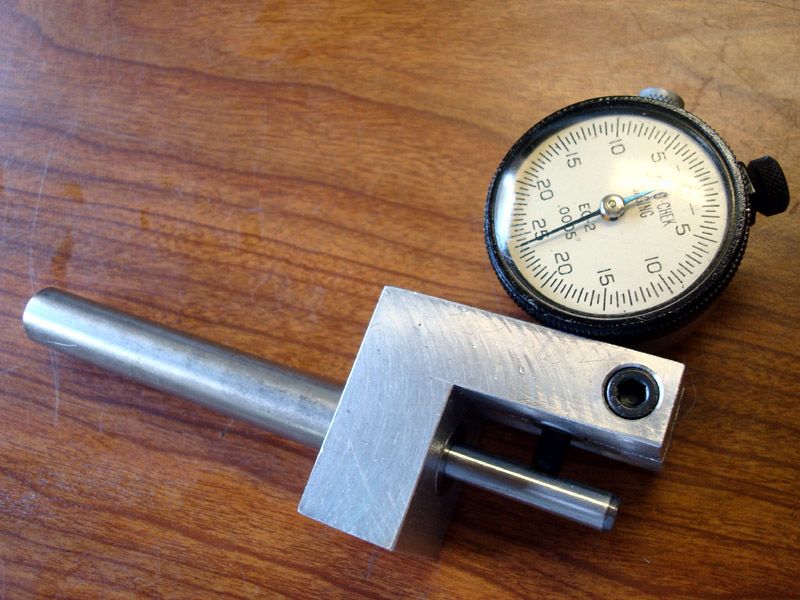
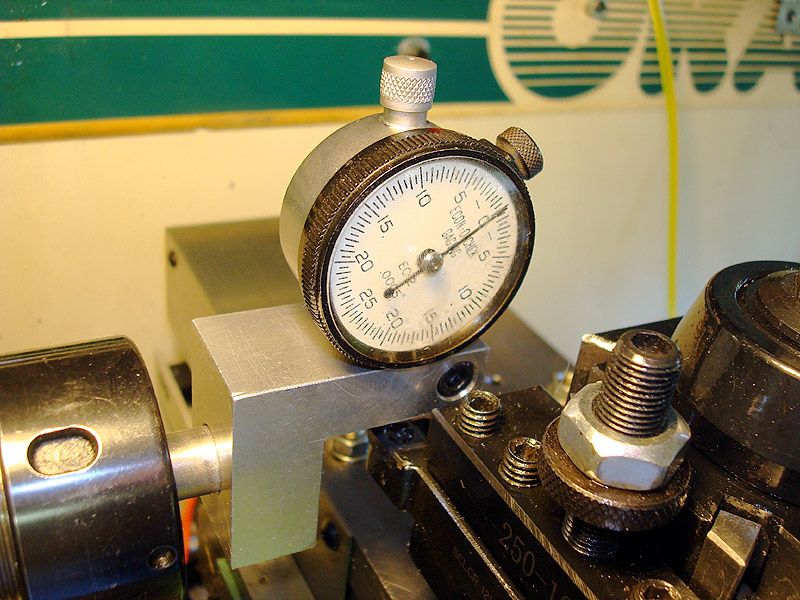