The task is to cut some custom spur gears in the home shop. If the gears work out they will go into a little live steam project. The gears are 48 diameteral pitch. Diameteral Pitch or DP is the relation between the number of teeth on the gear and its pitch diameter. For 48 DP, a 1 inch pitch diameter gear will have 48 teeth. We will cut 2 sizes of 48 DP gears, one with 16 teeth and three with 52 teeth.
The reference for this job is the Workshop Practice Series book #17, Gears and Gear Cutting by Ivan Law:
The book is available from Amazon.com or you can download it. Do a Google search for Workshop Practice Series PDF Gears. There will be a number of sites that have the PDF download. I followed Mr. Laws procedures without deviation.
First step is to make the cutter tools. The first cutter is a forming tool, used to make the actual gear cutter. The tables in Chapter 12 show all the dimensions. I used that table for 20-degree pressure angle. I also used the single button form tool, Fig 94 on page 117. The final gear cutters are 3/4" diameter. Here are cutters I made:
The steel for the cutters is alloy O1. O1 is the most widely used tool steel and is available from McMaster Carr and other suppliers. O1 is very easy to work with and harden. Shape and form the tool to the desired size. Heat with a torch to 1400 degrees F, which is cherry red heat in room light. Plunge in oil to quench. I used some leftover salad oil from the kitchen. Leave in the oil quench about 30 seconds, it cools down slowly. Quenched tool steel is too brittle at this point and needs tempering. To temper, suspend the tool in a small pot of salad oil on the kitchen stove. Heat to 350 degrees F using a candy thermometer to check the temperature. Leave it in about 10 minutes, pull out and let air dry. The O1 steel comes out very hard and will cut just about anything.
Lets cut the 52-tooth gear first. These are from 1/8 thick flat brass bar. Chuck a length of 1/2" diameter steel in the lathe cut and turn a 5/16 diameter boss. Thread the end to accept a nut.
Make sure the 1/2" is centered perfectly in the lathe to turn the boss. If your 3 jaw is not accurate enough, dial it in on the 4 jaw.
Gang up three pieces of brass stock on the shank and turn them to the final stock diameter for the gear.
Time to cut some gears. You will need a dividing head or rotary table mounted vertically. This is my little homemade Harold Hall dividing head.
It is a direct indexing head that uses the change gears from the Atlas 6 lathe for indexing.
The spindle hole is tapered with #2 Morse Taper (2MT). A 2MT collet holds cinches stock tightly in the dividing head be means of a draw bar.
Secure the 52-tooth lathe change gear to the spindle of the dividing head. Mount the dividing head to the mill table. Use a 1/2" 2MT collet to chuck the gear blanks
Bolt the gear cutter on the shank and chuck up in the mill spindle. Use a height measure device to set the gear cutter height.
Adjust the depth of cut and start cutting. 48DP gears are shallow tooth, so one pass per cut. Advance the dividing head spindle one notch on the indexing gear. Repeat 52 times.
Turned out just right.
Next time we will cut the 16 tooth gear and do something with the results.
The reference for this job is the Workshop Practice Series book #17, Gears and Gear Cutting by Ivan Law:

The book is available from Amazon.com or you can download it. Do a Google search for Workshop Practice Series PDF Gears. There will be a number of sites that have the PDF download. I followed Mr. Laws procedures without deviation.
First step is to make the cutter tools. The first cutter is a forming tool, used to make the actual gear cutter. The tables in Chapter 12 show all the dimensions. I used that table for 20-degree pressure angle. I also used the single button form tool, Fig 94 on page 117. The final gear cutters are 3/4" diameter. Here are cutters I made:

The steel for the cutters is alloy O1. O1 is the most widely used tool steel and is available from McMaster Carr and other suppliers. O1 is very easy to work with and harden. Shape and form the tool to the desired size. Heat with a torch to 1400 degrees F, which is cherry red heat in room light. Plunge in oil to quench. I used some leftover salad oil from the kitchen. Leave in the oil quench about 30 seconds, it cools down slowly. Quenched tool steel is too brittle at this point and needs tempering. To temper, suspend the tool in a small pot of salad oil on the kitchen stove. Heat to 350 degrees F using a candy thermometer to check the temperature. Leave it in about 10 minutes, pull out and let air dry. The O1 steel comes out very hard and will cut just about anything.
Lets cut the 52-tooth gear first. These are from 1/8 thick flat brass bar. Chuck a length of 1/2" diameter steel in the lathe cut and turn a 5/16 diameter boss. Thread the end to accept a nut.

Make sure the 1/2" is centered perfectly in the lathe to turn the boss. If your 3 jaw is not accurate enough, dial it in on the 4 jaw.
Gang up three pieces of brass stock on the shank and turn them to the final stock diameter for the gear.

Time to cut some gears. You will need a dividing head or rotary table mounted vertically. This is my little homemade Harold Hall dividing head.
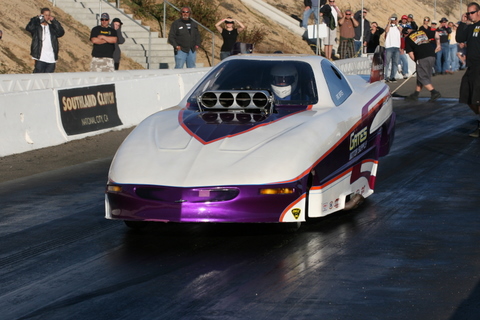
It is a direct indexing head that uses the change gears from the Atlas 6 lathe for indexing.
The spindle hole is tapered with #2 Morse Taper (2MT). A 2MT collet holds cinches stock tightly in the dividing head be means of a draw bar.

Secure the 52-tooth lathe change gear to the spindle of the dividing head. Mount the dividing head to the mill table. Use a 1/2" 2MT collet to chuck the gear blanks

Bolt the gear cutter on the shank and chuck up in the mill spindle. Use a height measure device to set the gear cutter height.

Adjust the depth of cut and start cutting. 48DP gears are shallow tooth, so one pass per cut. Advance the dividing head spindle one notch on the indexing gear. Repeat 52 times.

Turned out just right.

Next time we will cut the 16 tooth gear and do something with the results.