I have a collet chuck that I feel is not entirely up to snuff.
First, I checked that the main spindle is running true, the dial barely moves when clocking it, around 0,005 mm.
But when clocking the bore of the collet chuck I get a runout of around 0,1 mm (0,004"). Isn't this a bit high for a collet chuck of supposedly good quality?
Checking the bore of the spindle:
checking the bore of the collet chuck spindle:
Max. runout as indicated:
First, I checked that the main spindle is running true, the dial barely moves when clocking it, around 0,005 mm.
But when clocking the bore of the collet chuck I get a runout of around 0,1 mm (0,004"). Isn't this a bit high for a collet chuck of supposedly good quality?
Checking the bore of the spindle:
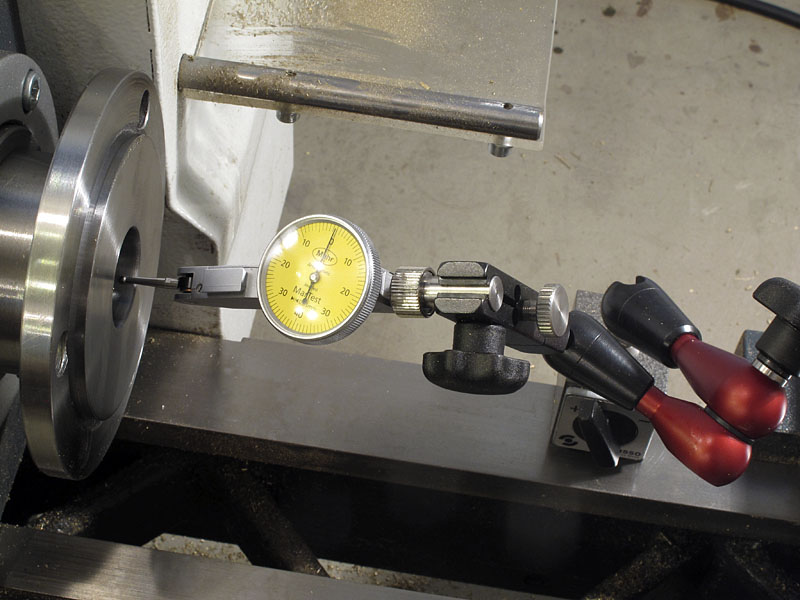
checking the bore of the collet chuck spindle:
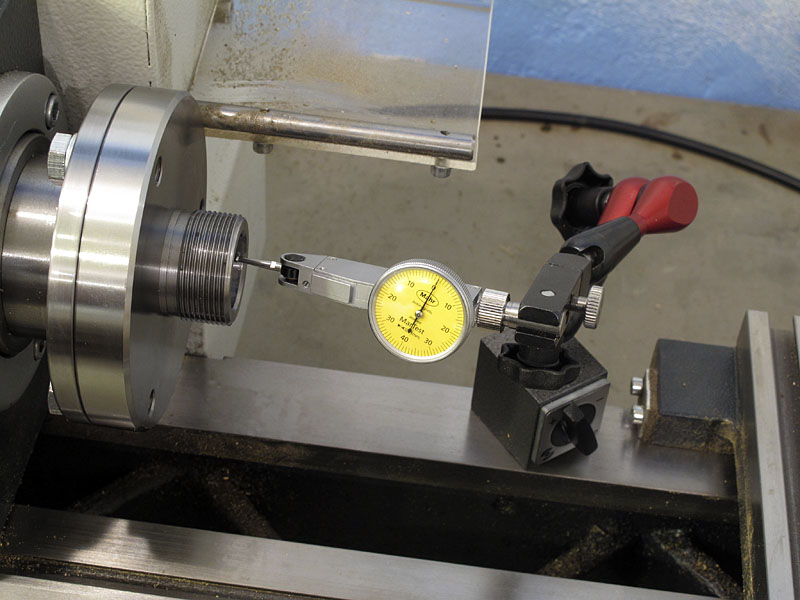
Max. runout as indicated:
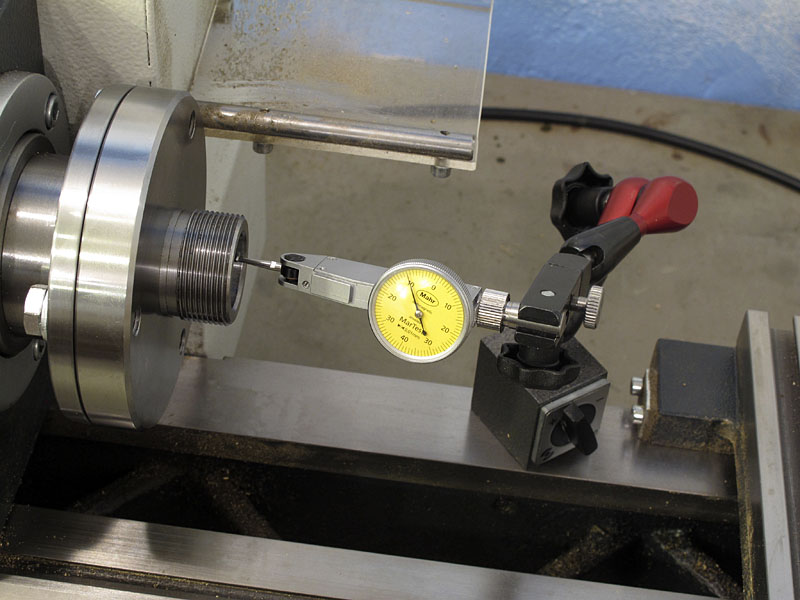