On my current build there are a number of 2-56 blind holes. I was having difficulty getting all of the swarf form the holes. Compressed air did not work well. Repeated running the in, withdrawing it and brushing off the swarf was time consuming. I came up with a simple tool that I find helpful.
The tool is simply a small sewing needle, some cotton thread and a piece of wood dowel for a handle. Simply wrap the thread around the needle and insert into the hole to be cleaned. Move the needle around in the hole and withdraw. Swarf tends to get caught in the thread and tapping fluid will be soaked up. Wibe of the swarf and repeat. It may take several insertions but I find it quicker that other methods I have tried. When the thread gets saturated with tapping fluid simply move to a fresh section of thread.
The needle I have been using worked well for 2-26 holes but was too large for 0-80 and M1.6 tapped holes. I will have to find a smaller needle for the very small holes.
The photos below should make this clear.
I would be interested in seeing other methods for cleaning small holes.
Eric
The tool is simply a small sewing needle, some cotton thread and a piece of wood dowel for a handle. Simply wrap the thread around the needle and insert into the hole to be cleaned. Move the needle around in the hole and withdraw. Swarf tends to get caught in the thread and tapping fluid will be soaked up. Wibe of the swarf and repeat. It may take several insertions but I find it quicker that other methods I have tried. When the thread gets saturated with tapping fluid simply move to a fresh section of thread.
The needle I have been using worked well for 2-26 holes but was too large for 0-80 and M1.6 tapped holes. I will have to find a smaller needle for the very small holes.
The photos below should make this clear.
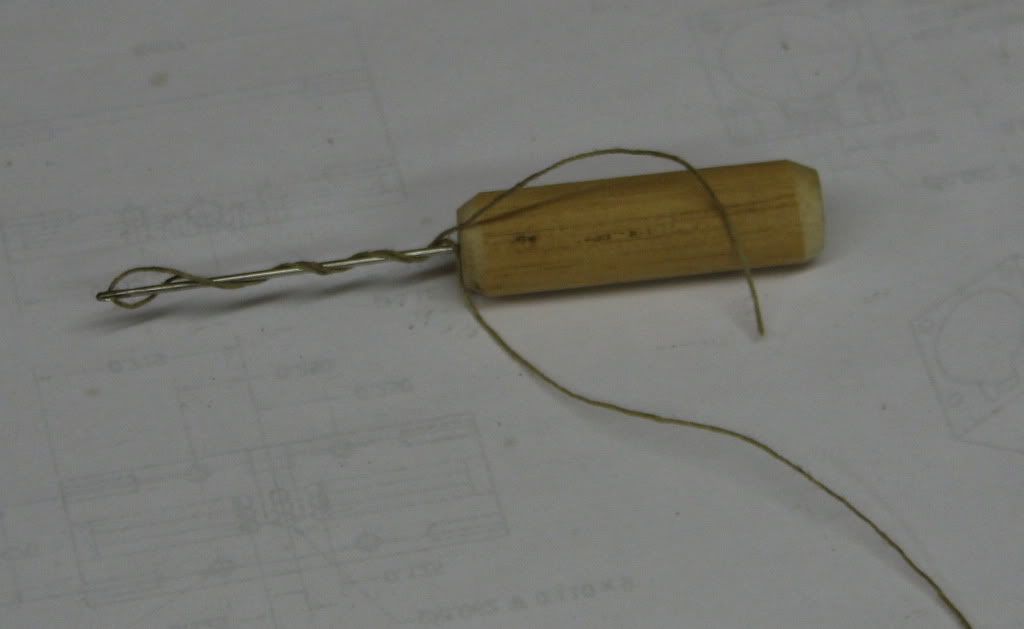

I would be interested in seeing other methods for cleaning small holes.
Eric