Some of you may have seen my intention to build this engine mentioned in other posts over the last couple of years, well Ive now got round to doing some as a bit of light relief from the Fowler and IHC that I have on the go.
The engine is based on one of a range of vertical pillar engines made by W.Benson in or around 1862 and this is a contemporary engraving showing the engine. More about W.Benson can be found here
I have always liked Anthony Mounts (AM from now on) models and this engine is shown in Vol 2 of his Historic Engines Worth Modeling but at 1/12th scale is a little small for my liking so I have scaled it up to 1/9th scale giving a flywheel of around 10 which is within my lathes capacity. The book is really a series of reprints of the various build series that have appeared in either ME or EIM and includes almost all the drawings. You can also buy the drawings or drawings & castings from Bruce Engineering
Ive been making odd bits when I had a moment over the last couple of months but will try to describe things in the order they appear in the book. Some photos are not upto my usual standard having been snapped with the phone between machining.
Starting with the rather organically shaped base which would come as a casting. I had been tossing around a few options for making this such as building up from 3 separate layers or carving from the solid (probably aluminium as I only intend to run on air) but the idea of getting all the curves to flow into one another was a bit off putting.
In the end I decide to use Corian as I had some left over from work and knew I could shape it with my usual woodworking tools. As with most corian jobs I started with a template of 6mm MR MDF as its easier to do any blending of curves in the soft thin MDF. The main centre holes for the cylinder, column and pump were co-ordinate drilled and then these were used to locate the curves centrally on the rotary table.
I then drilled the same 3 centres into the corian and at the same setting did all the bolt hole PCDs using the function on the DRO before rough cutting to shape on my smaller bandsaw.
Next the router table was set up with a replaceable tip flush trimmer, the template pinned to the Corian using the centre holes and routed to the shape of the template.
The trimming bit was then changed to a 1/8 rad roundover bit with small bearing to give a 1/16 quirk and the moulded edge run.
The only downside with routing Corian is that the swarf comes off like confetti and being a plastic sticks to everything due to static even when using dust extraction
And here it is done together with from left to right the cylinder base, column base and another section from the bottom of the column.
Next up is the column, AM has this drilled right through and uses a M8 stud to hold it to the base and keep the entablature in place but I opted to make it from 4 sections held together with CSK socket screws and then use the actual flange bolts to hold things together. By having the top and bottoms as separate parts the main column could come out of a 6 length of 1 .75 steel. Here it is having one end drilled & tapped for the CSK screws
And with it all assembled the flat for the piston rod guide milled and tapped, the base was still rectangular at this stage so I could clock the whole thing true. The toolmakers clamps are just to take out any flex, there are two hold downs on the back left angle plate that take the load.
And a view from above showing the screws and how I used a spigot/hole on all parts to keep things concentric
Next up its the Entablature
Jason
The engine is based on one of a range of vertical pillar engines made by W.Benson in or around 1862 and this is a contemporary engraving showing the engine. More about W.Benson can be found here

I have always liked Anthony Mounts (AM from now on) models and this engine is shown in Vol 2 of his Historic Engines Worth Modeling but at 1/12th scale is a little small for my liking so I have scaled it up to 1/9th scale giving a flywheel of around 10 which is within my lathes capacity. The book is really a series of reprints of the various build series that have appeared in either ME or EIM and includes almost all the drawings. You can also buy the drawings or drawings & castings from Bruce Engineering
Ive been making odd bits when I had a moment over the last couple of months but will try to describe things in the order they appear in the book. Some photos are not upto my usual standard having been snapped with the phone between machining.
Starting with the rather organically shaped base which would come as a casting. I had been tossing around a few options for making this such as building up from 3 separate layers or carving from the solid (probably aluminium as I only intend to run on air) but the idea of getting all the curves to flow into one another was a bit off putting.
In the end I decide to use Corian as I had some left over from work and knew I could shape it with my usual woodworking tools. As with most corian jobs I started with a template of 6mm MR MDF as its easier to do any blending of curves in the soft thin MDF. The main centre holes for the cylinder, column and pump were co-ordinate drilled and then these were used to locate the curves centrally on the rotary table.
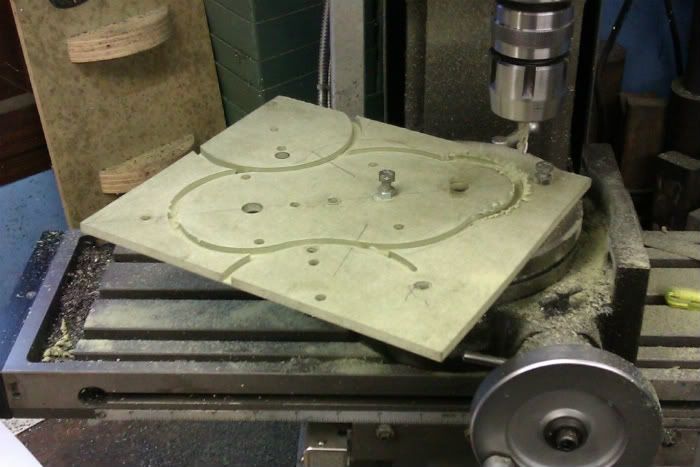
I then drilled the same 3 centres into the corian and at the same setting did all the bolt hole PCDs using the function on the DRO before rough cutting to shape on my smaller bandsaw.
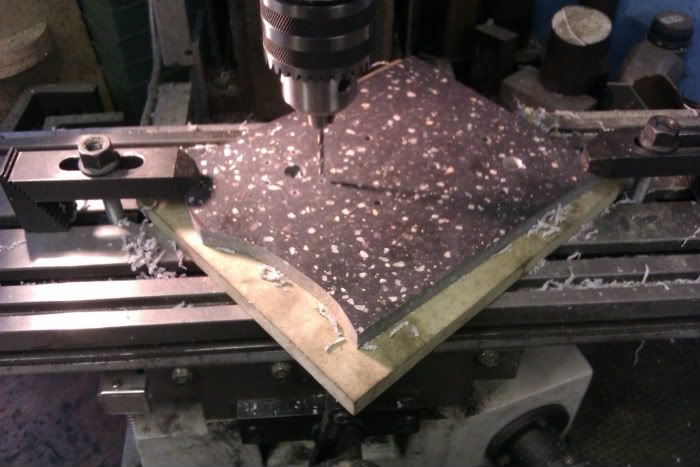
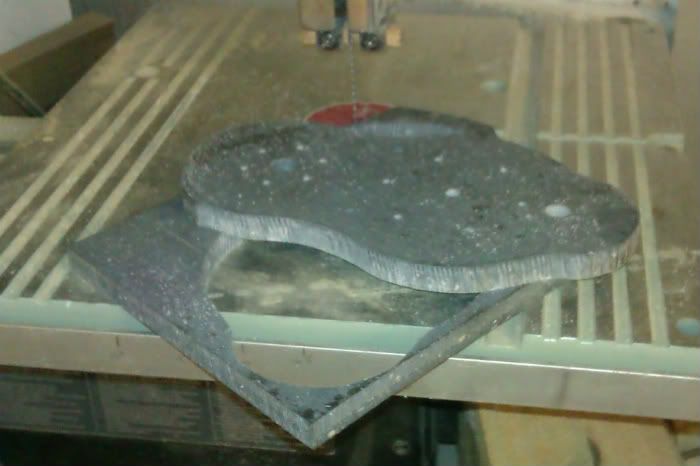
Next the router table was set up with a replaceable tip flush trimmer, the template pinned to the Corian using the centre holes and routed to the shape of the template.
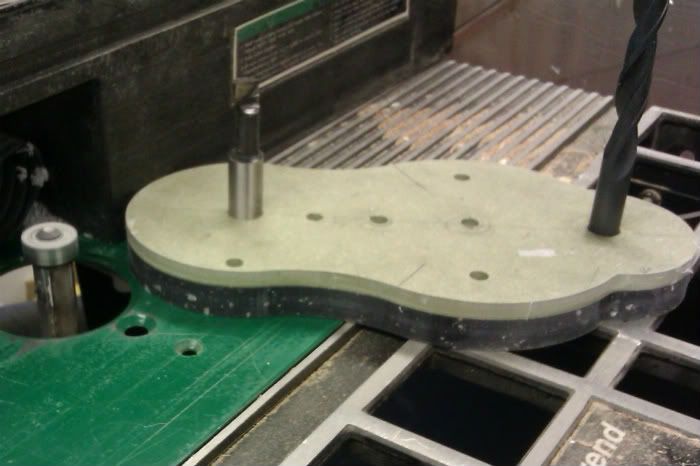
The trimming bit was then changed to a 1/8 rad roundover bit with small bearing to give a 1/16 quirk and the moulded edge run.
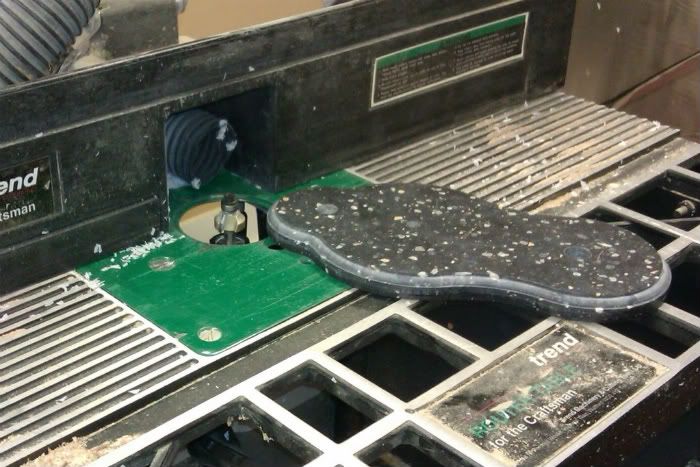
The only downside with routing Corian is that the swarf comes off like confetti and being a plastic sticks to everything due to static even when using dust extraction
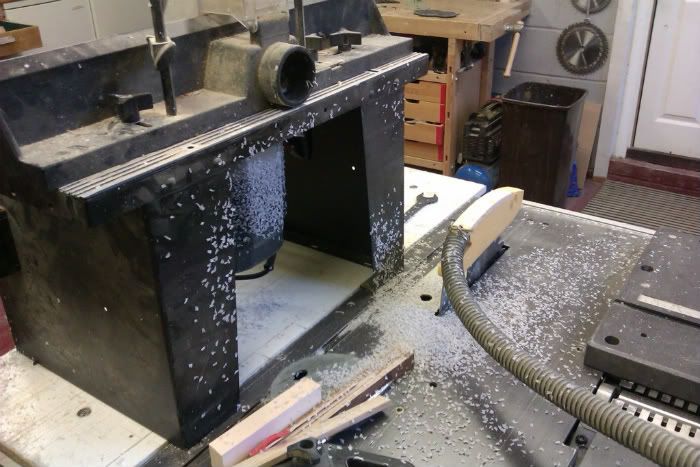
And here it is done together with from left to right the cylinder base, column base and another section from the bottom of the column.
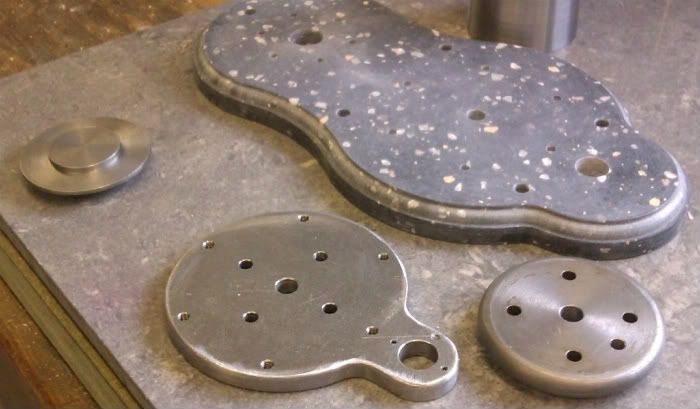
Next up is the column, AM has this drilled right through and uses a M8 stud to hold it to the base and keep the entablature in place but I opted to make it from 4 sections held together with CSK socket screws and then use the actual flange bolts to hold things together. By having the top and bottoms as separate parts the main column could come out of a 6 length of 1 .75 steel. Here it is having one end drilled & tapped for the CSK screws
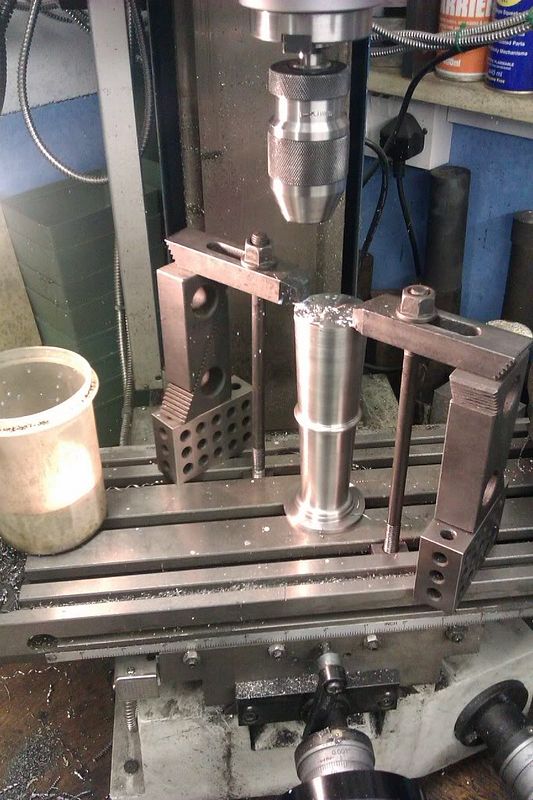
And with it all assembled the flat for the piston rod guide milled and tapped, the base was still rectangular at this stage so I could clock the whole thing true. The toolmakers clamps are just to take out any flex, there are two hold downs on the back left angle plate that take the load.
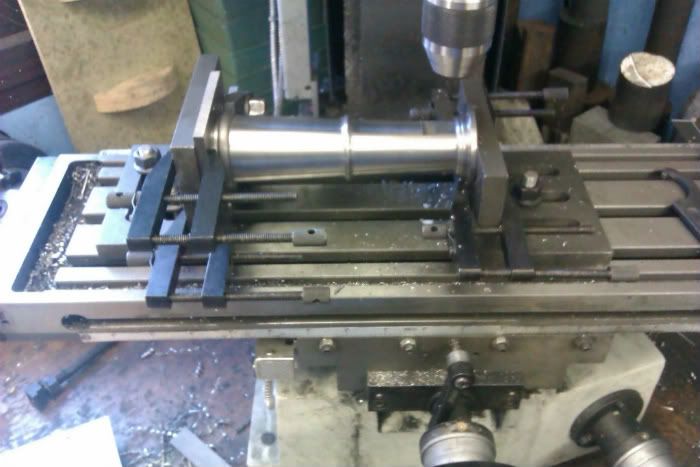
And a view from above showing the screws and how I used a spigot/hole on all parts to keep things concentric
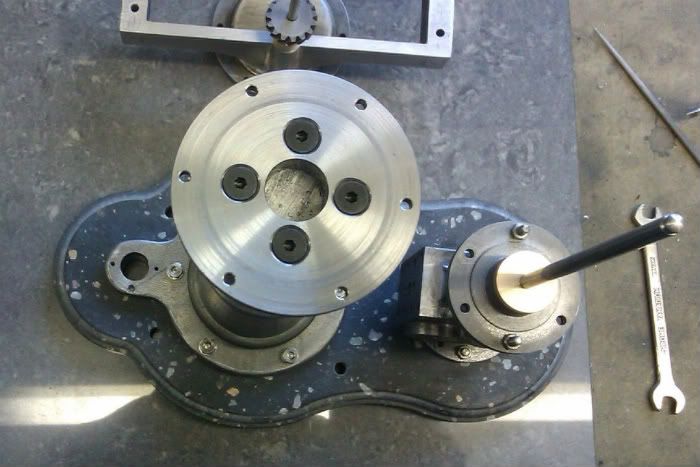
Next up its the Entablature
Jason