xlchainsaw
Well-Known Member
- Joined
- Apr 22, 2008
- Messages
- 98
- Reaction score
- 3
ive been a bit busy casting these 4 inch brackets for lineshafts.
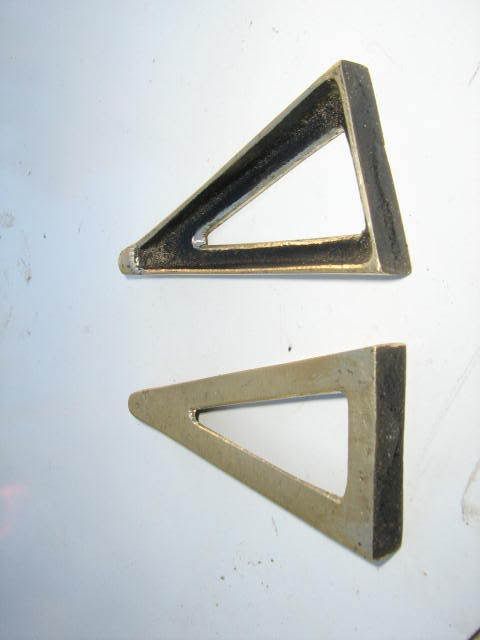
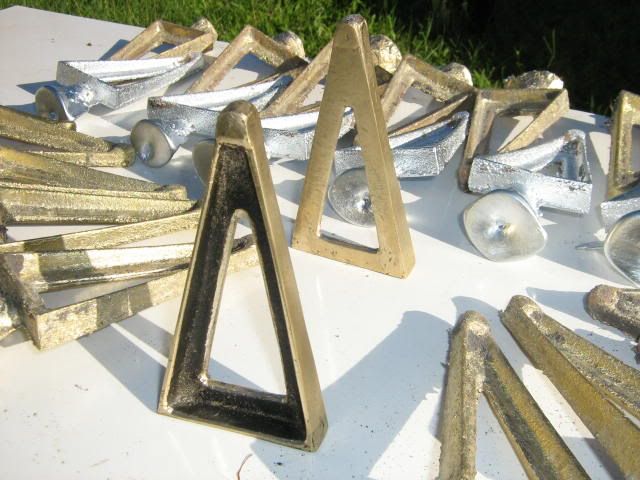
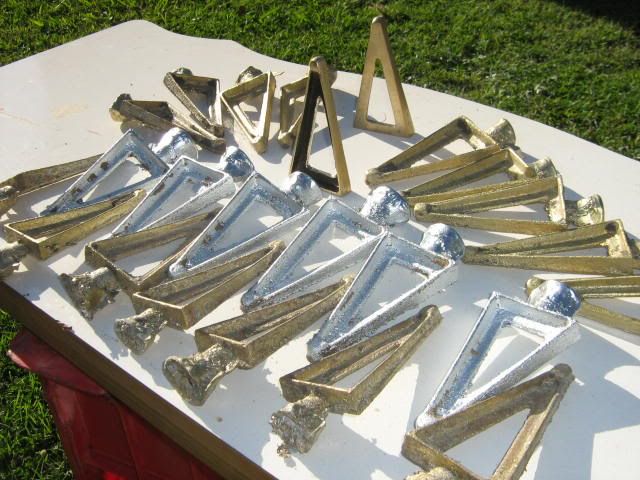
glad to hear you are getting started. im not an expert with brass as yet. please dont put aluminium into the brass!!!!!!!!!!!under the right conditions you will end up with a thermite reaction and that will just melt through every thing.! dont use any flux!! at first i put it in and that was a big mistake.if you put zinc in with red brass it is suppose to make yellow brass. my experiments failed on this.... but!!the brass shown was red brass??????? and now its yellow brass with nothing added?????? i even poured some 1/4 inch square7/32 and 3/16 and twisted it without annealling or shearing it??????im awaiting an opion from a qualified source at the moment but i did the first pour by accident!! then i repeated it three more times with the same result. there is nothing new in foundry work only dark secrets.Mike N said:Nice work!
I am just getting started in the foundry fun! I have poured a few brass ingots from brass wire EDM scraps, I get about 30% slag when I melt it down initially. I have been scrounging yellow & red brass castings from our local scrap dealers, I plan to melt some of this down this weekend. Do I need to add anything to make the brass more pourable? I do have some flux that I purchased. I have a flask ready & a pattern made to test out the process. I was told that throwing in a piece of Aluminum would help to make the brass more liquid??
brass is very interesting and there are so many different recipes. with special testing gear its beyond the home caster to know exactly whats in it. i have a mate who works in a foundry all day pouring brass, he knows all about commercial foundry work,products mold making ect. but!!!! he doesnt know exactly whats in the pot! first they melt the copper and then add zinc and a bit of this and a bit of that.!Bernd said:Hey xl,
On that brass casting, do you add zinc before the pour? Do you use scrap brass or buy ingots?
Was just wondering. I'd like to try brass someday. have done aluminum.
Bernd
thanks bigal. brass sure has expanded my modeling ideas.bigal2749 said:Great Work
Always interested in what you're up to.
Al
cfellows said:Hey, XL, nice work. What process are you using? Lost Wax or what?
Thx...
Chuck
Enter your email address to join: