EDIT: File re-uploaded... should work now
-----
After a few hours of work, I've come up with two 3D designs in Google's SketchUp. One uses dovetails and a similar adjustment configuration to the Criterion heads I've seen pictures of. If made in multiple pieces, a dovetail cutter isn't needed.
The other uses a sort of I-beam configuration and an adjustable gib.
The main horizontal hole is 1/2", and the vertical holes allow for both 1/2" and 3/8" boring bars. I figure the horizontal could be used with a 3/8" bar with an adapter sleeve.
Note that some of the fasteners and holes may not be standard or perfectly placed at this point. If there's enough interest, I can fix this as well as do a bit of a write-up.
Since I've never actually used, or even held a boring head, I was wondering if you folks out there could add your two cents on these designs... the pros, cons, suggestions, preference for one or the other - both for construction and use.
I've included some pictures here, and the SketchUp files attached. Feel free to use the design. I figure there are a bunch of patents on this stuff, so I'm unlikely to make any money on it. The only thing I ask is that you drop me an email to say "thanks".
-Sparky
View attachment BoringHead.zip
-----
After a few hours of work, I've come up with two 3D designs in Google's SketchUp. One uses dovetails and a similar adjustment configuration to the Criterion heads I've seen pictures of. If made in multiple pieces, a dovetail cutter isn't needed.
The other uses a sort of I-beam configuration and an adjustable gib.
The main horizontal hole is 1/2", and the vertical holes allow for both 1/2" and 3/8" boring bars. I figure the horizontal could be used with a 3/8" bar with an adapter sleeve.
Note that some of the fasteners and holes may not be standard or perfectly placed at this point. If there's enough interest, I can fix this as well as do a bit of a write-up.
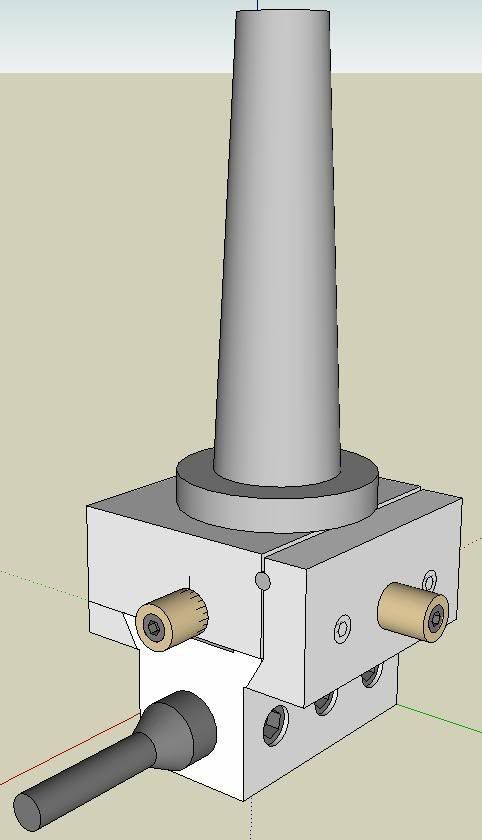
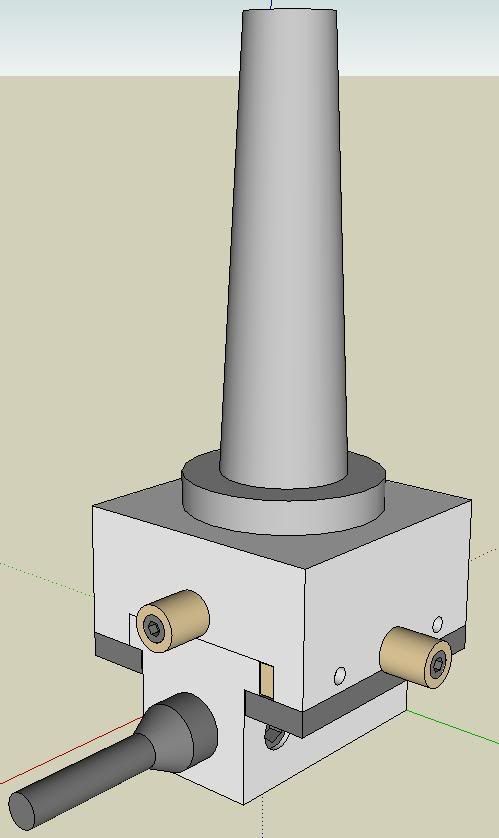
Since I've never actually used, or even held a boring head, I was wondering if you folks out there could add your two cents on these designs... the pros, cons, suggestions, preference for one or the other - both for construction and use.
I've included some pictures here, and the SketchUp files attached. Feel free to use the design. I figure there are a bunch of patents on this stuff, so I'm unlikely to make any money on it. The only thing I ask is that you drop me an email to say "thanks".
-Sparky
View attachment BoringHead.zip