rake60
Well-Known Member
- Joined
- Jul 8, 2007
- Messages
- 4,756
- Reaction score
- 124
Another thread here mentioned the PB Blaster penetrating oil.
It's the best penetrating oil on the market in my opinion.
If you have air tools such as burr guns, die grinders sanders, etc
you see the warning embossed in the housing that reads:
Oil Daily
Do you do that?
Neither do I...
Blaster has a great product for the air tools as well!
Here's a link to the page about their Air Tool Conditioner.
One little tip from experience, Know where the air exhausts from the tool
and have it pointed away from you when pulling the trigger the first time
after filling it up with the ATC!
Rick
It's the best penetrating oil on the market in my opinion.
If you have air tools such as burr guns, die grinders sanders, etc
you see the warning embossed in the housing that reads:
Oil Daily
Do you do that?
Neither do I...
Blaster has a great product for the air tools as well!
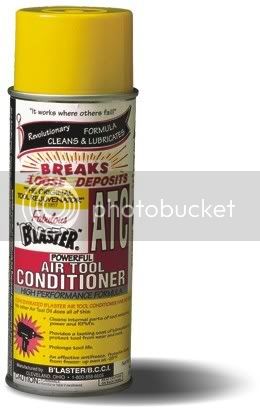
Here's a link to the page about their Air Tool Conditioner.
One little tip from experience, Know where the air exhausts from the tool
and have it pointed away from you when pulling the trigger the first time
after filling it up with the ATC!
Rick