BobWarfield
Well-Known Member
- Joined
- Dec 27, 2007
- Messages
- 1,151
- Reaction score
- 1
I just cut the slots on the supports for my disc sander table:
I was reminded of a "trick" I use that seems to work really well: I avoid plunging the cutter straight down. Instead, I lower it slightly and then start cranking the X or Y (Y in the photo) in the direction I want to cut. At the same time, I turn the quill handwheel so the cutter is both lowering and moving along the slot. This seems to let me cut radically faster and more smoothly. Someone here probably knows the reason, but I just picked it up watching CNC machines which never seem to go straight in--they'll spiral or do some other manuever to get to depth.
You'd be amazed at how much faster you can go this way. I was doing a couple other things when cutting that slot. First I had put a good shot of Tap Magic, my preferred aluminum lube. Second, while cutting, once I got to desired depth and had a hand free, I hit the trailing edge of the cutter with a continuous shot of compressed air to keep the chips moving. Lastly, I left about 1/8" on each end of the desired slot until the end. When the cutter was all the way through and cutting full thickness, I picked up the ends.
This process seems to work pretty well for me. The pros probably have further refinements. I would have preferred a 2-flute, but the 4 was all I had in 3/8".
Best,
BW
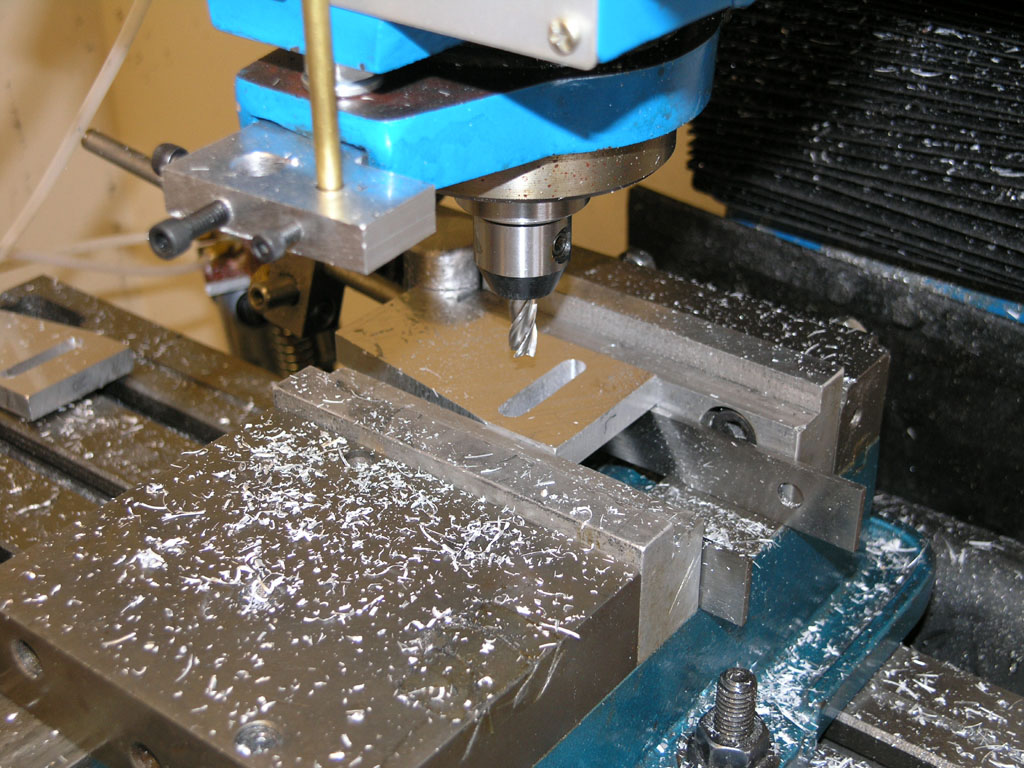
I was reminded of a "trick" I use that seems to work really well: I avoid plunging the cutter straight down. Instead, I lower it slightly and then start cranking the X or Y (Y in the photo) in the direction I want to cut. At the same time, I turn the quill handwheel so the cutter is both lowering and moving along the slot. This seems to let me cut radically faster and more smoothly. Someone here probably knows the reason, but I just picked it up watching CNC machines which never seem to go straight in--they'll spiral or do some other manuever to get to depth.
You'd be amazed at how much faster you can go this way. I was doing a couple other things when cutting that slot. First I had put a good shot of Tap Magic, my preferred aluminum lube. Second, while cutting, once I got to desired depth and had a hand free, I hit the trailing edge of the cutter with a continuous shot of compressed air to keep the chips moving. Lastly, I left about 1/8" on each end of the desired slot until the end. When the cutter was all the way through and cutting full thickness, I picked up the ends.
This process seems to work pretty well for me. The pros probably have further refinements. I would have preferred a 2-flute, but the 4 was all I had in 3/8".
Best,
BW