BobWarfield
Well-Known Member
- Joined
- Dec 27, 2007
- Messages
- 1,151
- Reaction score
- 1
Fly cutters are great tools for the mill. They're relatively cheap, and they cut a nice wide swath. In fact, while I have a multiple insert face mill that I use when I need to remove a lot of material, I still return to the flycutter for some operations. Namely, when I have to face a big plate, I want the widest cutter possible, because that leaves me the best finish.
Recently, I was working on the table for my disc grinder. I'll publish pix when the grinder is done, or you can follow along on my site: http://www.cnccookbook.com/CCDiscSander.htm
What I wanted to pass along here is a little comparison work on two popular fly cutters:
I know you must have seen the one on the right, or its like. They seem to be the most common. I got the one on the left off eBay when I went looking for a really big flycutter for facing larger plates. You can make one two. I believe Widigitmaster has plans for one over on CNCZone somewhere.
Here is a sample cut with the smaller flycutter for my grinder table:
It's not bad, but I hate that ugly line making two passes leaves.
Now here is the result from the larger flycutter:
That's a much happier result. It isn't as good as ground, and I won't claim a mirror finish, but it is flat, which is what I was looking for.
One more thing to notice for newcomers:
That's a closeup from the first flycutter. Note how you can see a Moire sort of pattern? The circular tool marks go both ways, indicating both sides of the plane of the cut were engaging. They're not quite even though, indicating the head of my mill was slightly out of tram (i.e. not square). The bigger the flycutter, the more sensitive it is to tram. Note on the pic from the big cutter (the one with the 1-2-3 block on the surface) you only see one set of marks? With the arm so long, the difference in cutting depths at the two sides of the cutting plane is now enough that you can clearly see the out of tram condition.
The tram hardly matters for this operation, but if I need to cut something accurately, I'll have to get out my Indicol and tram that head!
You'll also note some irregularity around the edges. That indicates flexure. Too much overhang from that vise. Ideally, I would have supported the plate at the ends with some machinist's jacks to help that situation. Again, it hardly matters for my grinder table, but I want to pass along such tips if you need more precision.
Cheers,
BW
Recently, I was working on the table for my disc grinder. I'll publish pix when the grinder is done, or you can follow along on my site: http://www.cnccookbook.com/CCDiscSander.htm
What I wanted to pass along here is a little comparison work on two popular fly cutters:
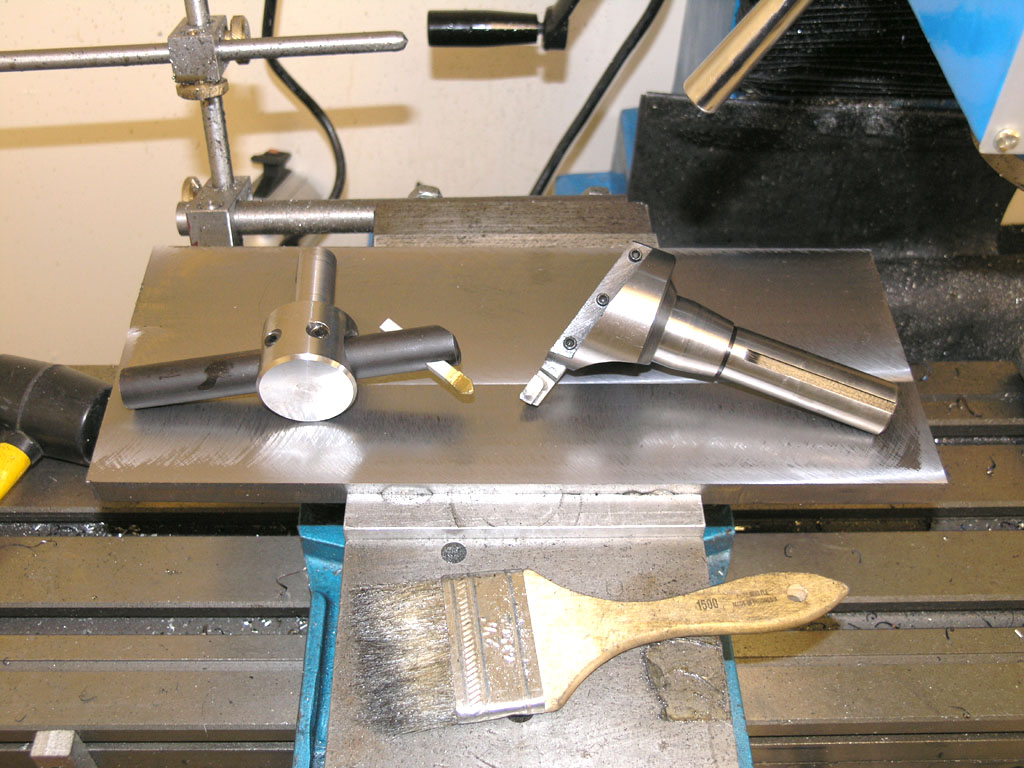
I know you must have seen the one on the right, or its like. They seem to be the most common. I got the one on the left off eBay when I went looking for a really big flycutter for facing larger plates. You can make one two. I believe Widigitmaster has plans for one over on CNCZone somewhere.
Here is a sample cut with the smaller flycutter for my grinder table:
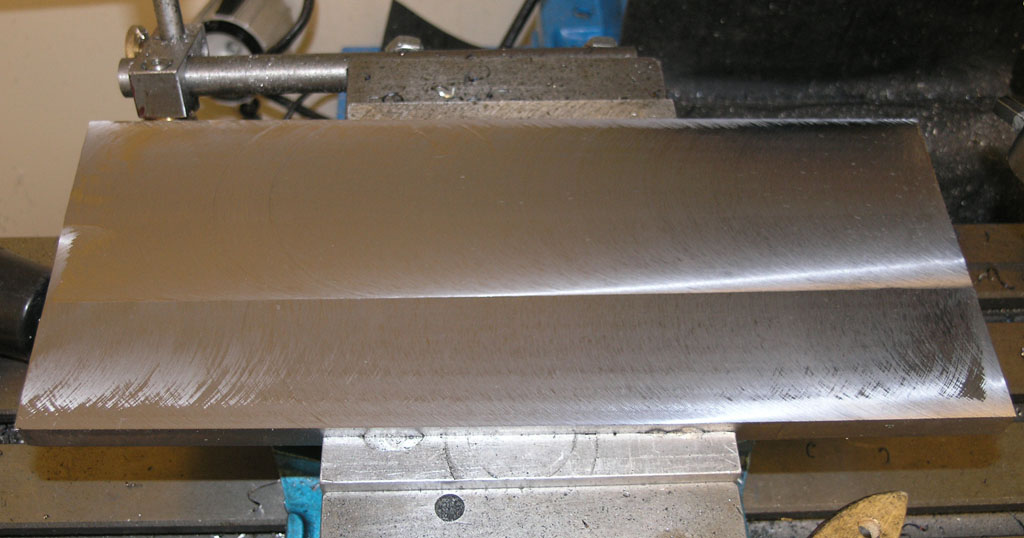
It's not bad, but I hate that ugly line making two passes leaves.
Now here is the result from the larger flycutter:
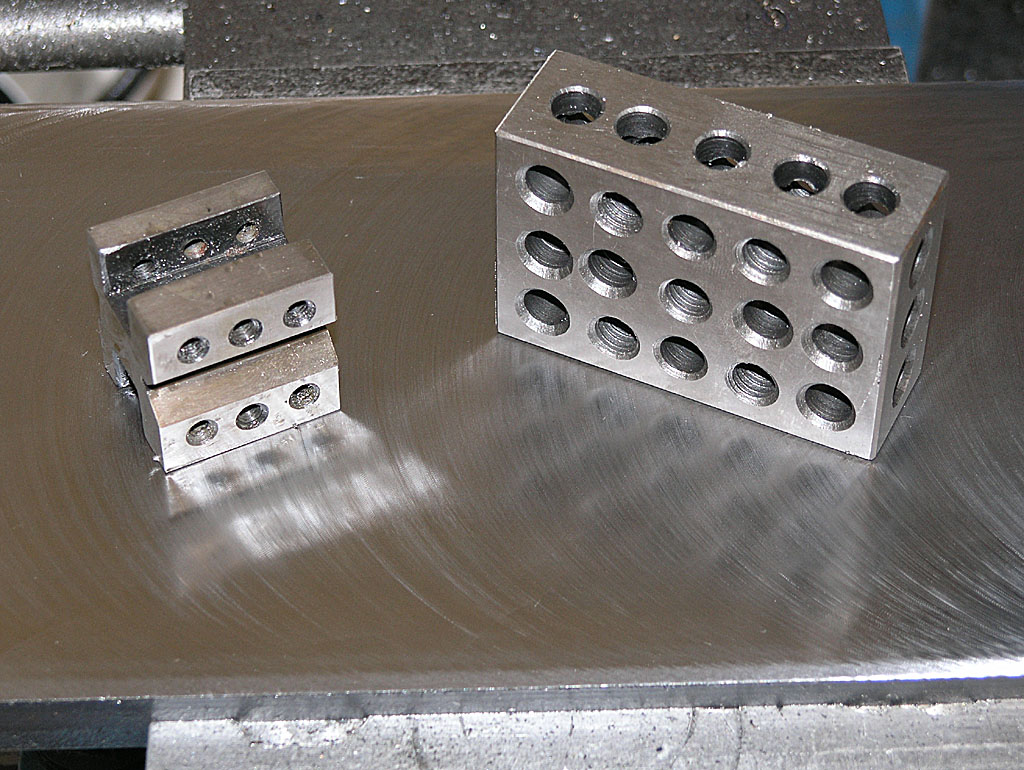
That's a much happier result. It isn't as good as ground, and I won't claim a mirror finish, but it is flat, which is what I was looking for.
One more thing to notice for newcomers:
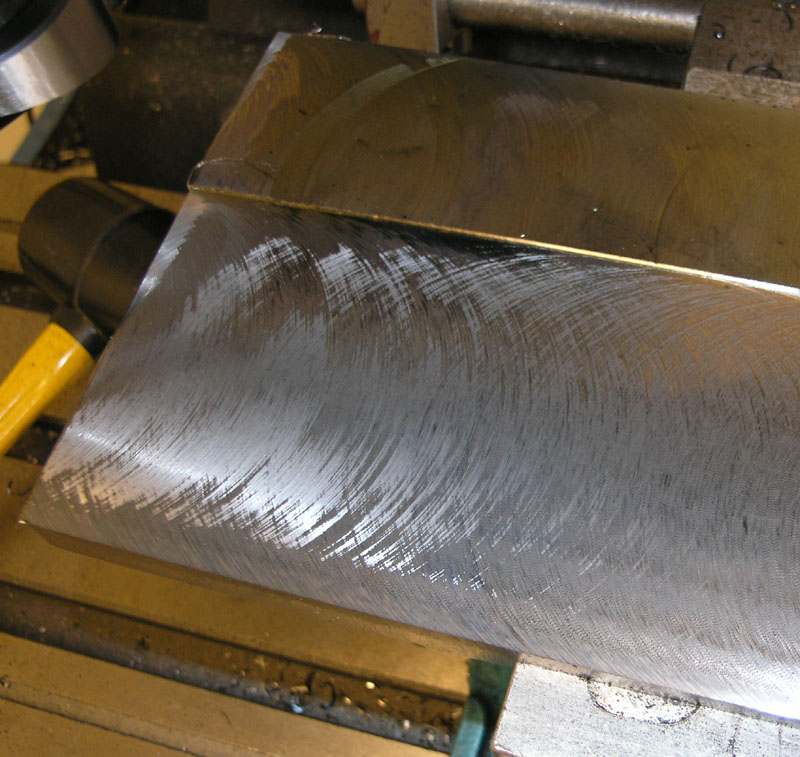
That's a closeup from the first flycutter. Note how you can see a Moire sort of pattern? The circular tool marks go both ways, indicating both sides of the plane of the cut were engaging. They're not quite even though, indicating the head of my mill was slightly out of tram (i.e. not square). The bigger the flycutter, the more sensitive it is to tram. Note on the pic from the big cutter (the one with the 1-2-3 block on the surface) you only see one set of marks? With the arm so long, the difference in cutting depths at the two sides of the cutting plane is now enough that you can clearly see the out of tram condition.
The tram hardly matters for this operation, but if I need to cut something accurately, I'll have to get out my Indicol and tram that head!
You'll also note some irregularity around the edges. That indicates flexure. Too much overhang from that vise. Ideally, I would have supported the plate at the ends with some machinist's jacks to help that situation. Again, it hardly matters for my grinder table, but I want to pass along such tips if you need more precision.
Cheers,
BW