The model is of the 5hp Galloway round rod hit and miss engine to 1/3rd scale so its quite a big old lump.
Originally made by Richard Shelley the Galloway kits are now done by
Linley Machine under the Minicastings range and are available in a number of different scales. You can also get them via Forrest Classics in the UK.
So lets start at the bottom. The kit is supplied with a sub-base and on the larger scale castings the four mounting lugs have to be added as it makes it easier to cast the base without them. These started off as a length of 5/8" hot rolled.
These were cleaned up all round with a fly cutter, cut and milled to length and a hole drilled through each.
I then set up the vice on top of the rotary table with a stop and rounded the two ends.
The last job was to machine these to the correct height which got rid of the piece that was in the vice and therfore not rounded off.
I then spent some time shimming up the base with packers and feeler gauges to ensure that when the underside was machined it would sit true when turned upright
You may be able to see a darker shiny area in the corner, this is where the thin extremities of the casting have cooled quickly and "chilled" the iron, luckily I was using a carbide tipped cutter as these hard chilled spots will take the edge straight off HSS tooling.
It was then a simple job to clamp the casting the right way up to machine the top surface
The sockets for the mounting lugs were roughed out with a drill and then finished with a 5/8" milling cutter
Not a bad fit, these will now be bonded with JB Weld which will also be used to fillet the internal corners.
I also took a pass off the ends to remove some of the excess draught angle
All that work and this piece may not get used, it all depends on how I mount the engine when finished.
J
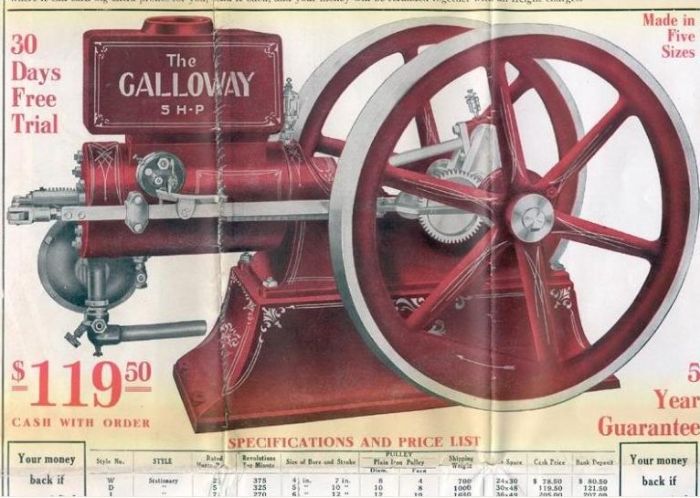
Originally made by Richard Shelley the Galloway kits are now done by
Linley Machine under the Minicastings range and are available in a number of different scales. You can also get them via Forrest Classics in the UK.
So lets start at the bottom. The kit is supplied with a sub-base and on the larger scale castings the four mounting lugs have to be added as it makes it easier to cast the base without them. These started off as a length of 5/8" hot rolled.
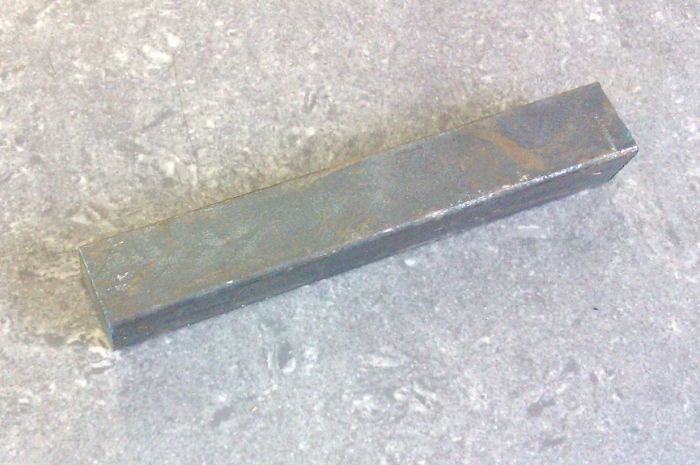
These were cleaned up all round with a fly cutter, cut and milled to length and a hole drilled through each.
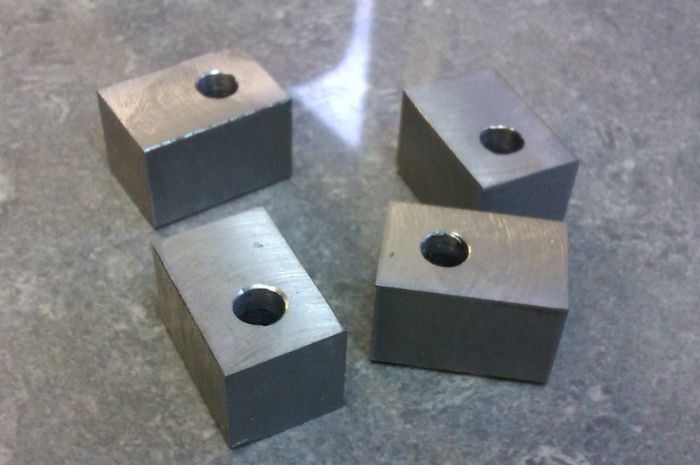
I then set up the vice on top of the rotary table with a stop and rounded the two ends.
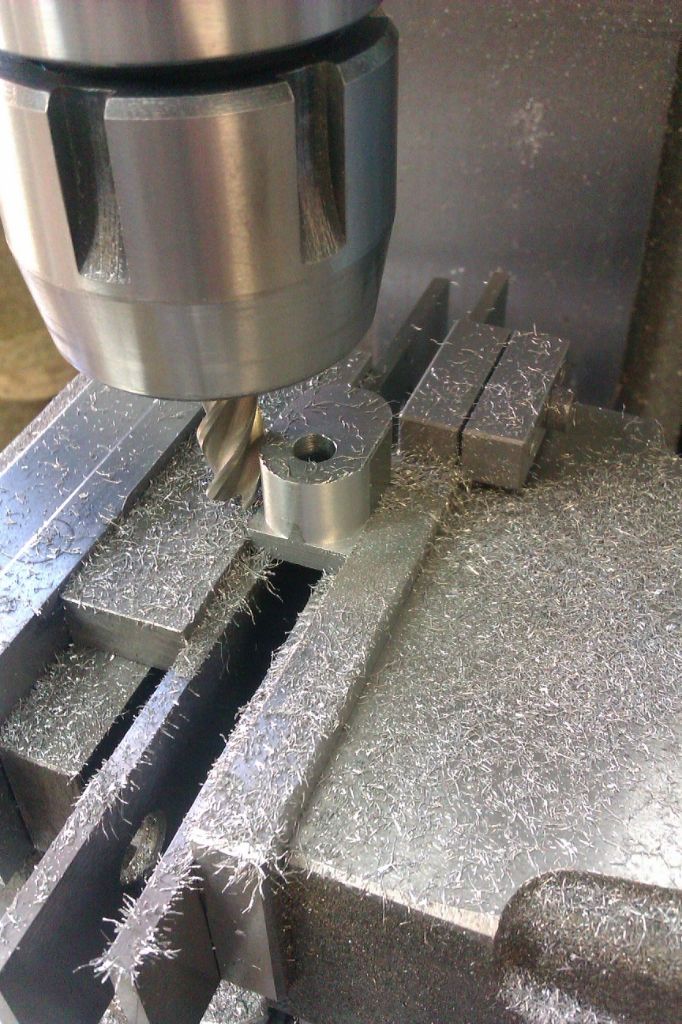
The last job was to machine these to the correct height which got rid of the piece that was in the vice and therfore not rounded off.
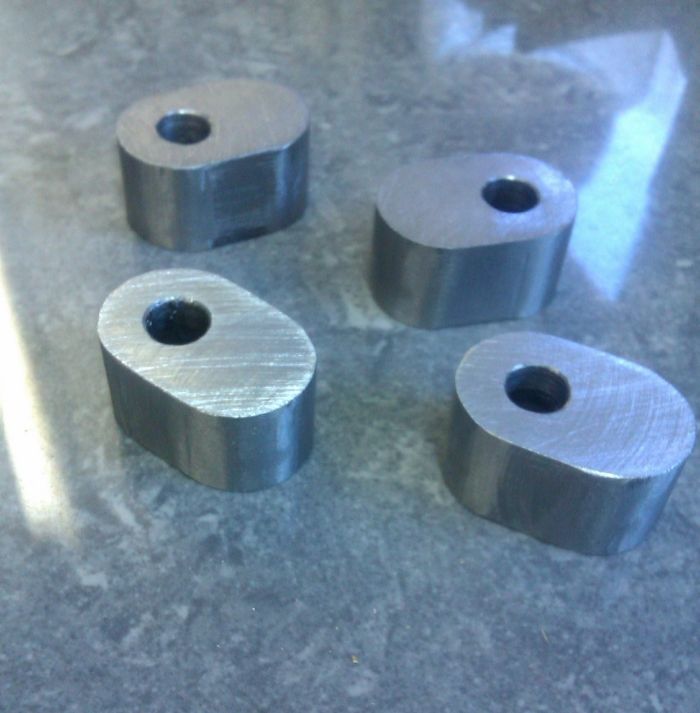
I then spent some time shimming up the base with packers and feeler gauges to ensure that when the underside was machined it would sit true when turned upright
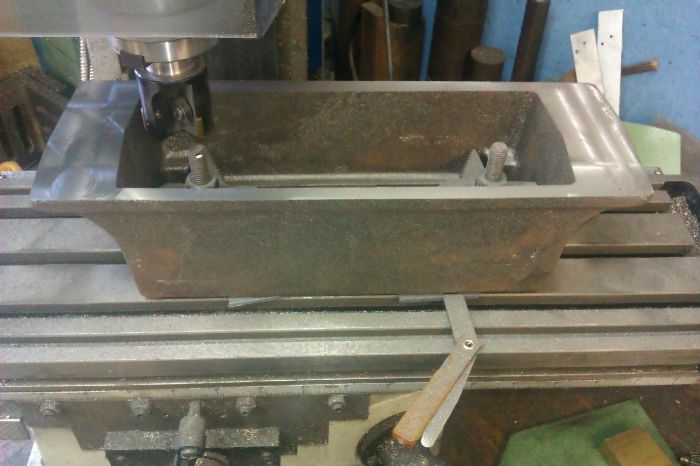
You may be able to see a darker shiny area in the corner, this is where the thin extremities of the casting have cooled quickly and "chilled" the iron, luckily I was using a carbide tipped cutter as these hard chilled spots will take the edge straight off HSS tooling.
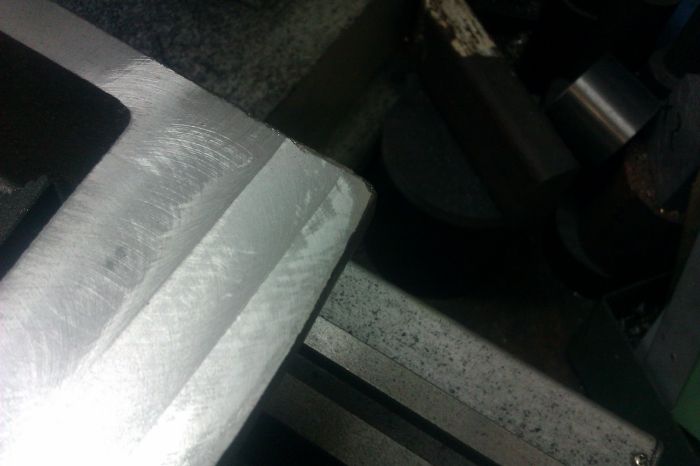
It was then a simple job to clamp the casting the right way up to machine the top surface
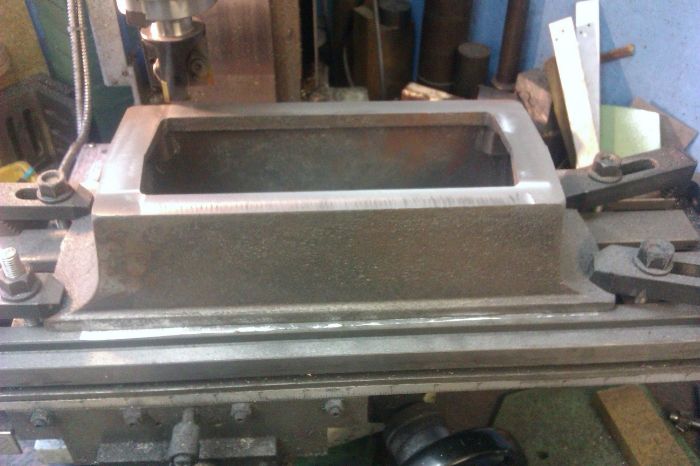
The sockets for the mounting lugs were roughed out with a drill and then finished with a 5/8" milling cutter
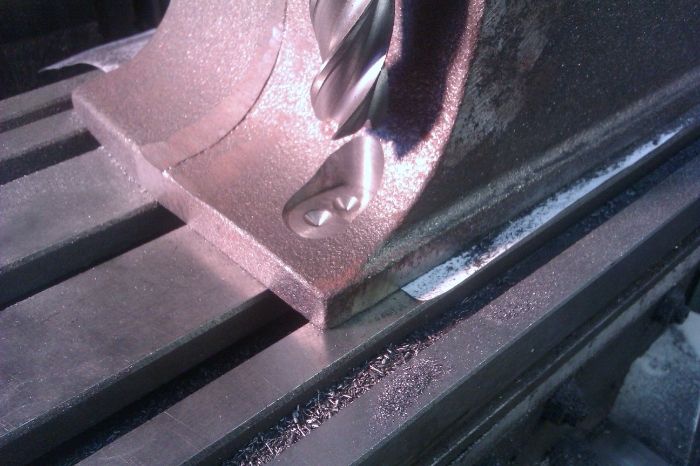
Not a bad fit, these will now be bonded with JB Weld which will also be used to fillet the internal corners.
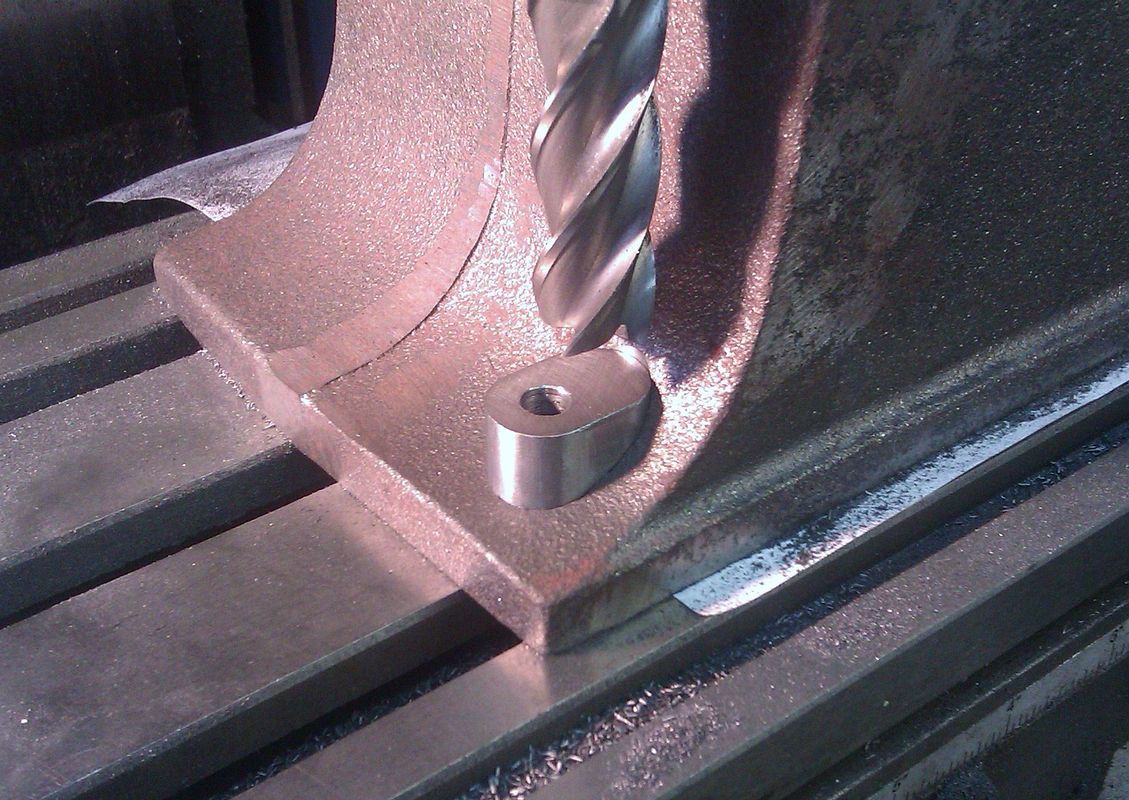
I also took a pass off the ends to remove some of the excess draught angle
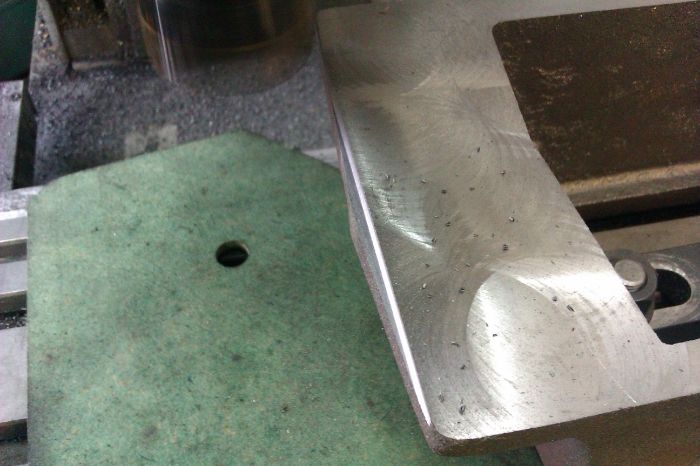
All that work and this piece may not get used, it all depends on how I mount the engine when finished.
J