So there we have it. A gear reducer mount, in all its splendor!!! (even with a collection of funky bolts holding things together.) I think that was the hardest part to do, and mill troubles aside, it was actually quite easy.
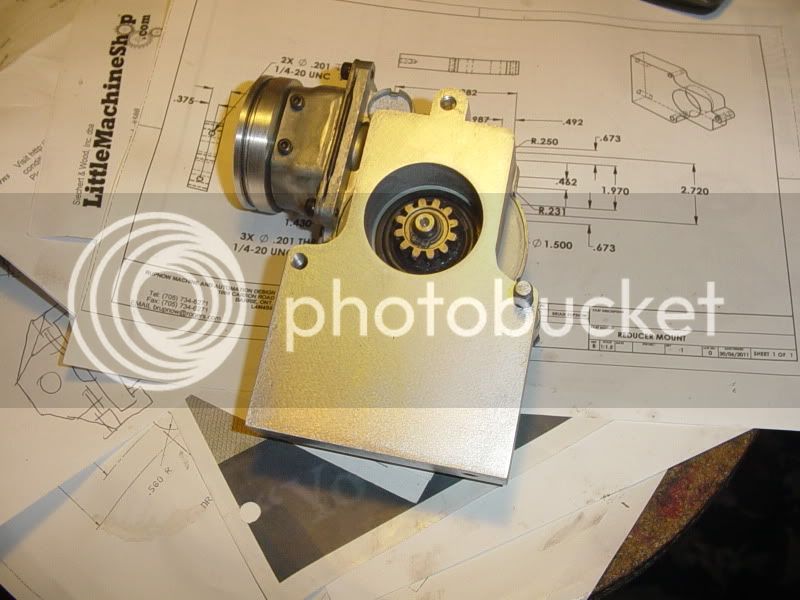
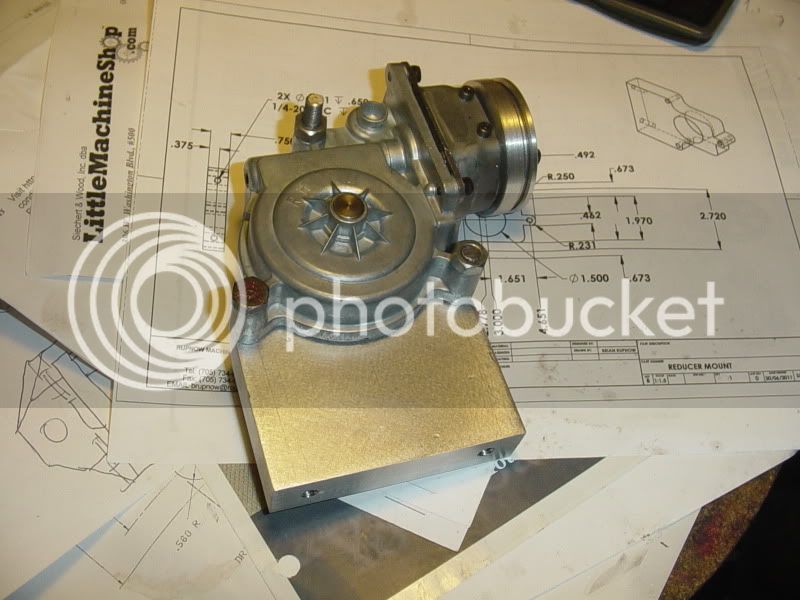
"People also liked the Pumpjack oil pumping model which I designed, built, and posted.(although I haven't seen anyone else build one)."
deadin said:Brian,
re your
Here's one complete with your Horizontal Twin powering it.. :bow:
http://www.youtube.com/user/deadin391#p/a/u/0/6sygYpkqju0
tel said:
Noitoen said:The magnet going down next to that brass plate is going to slow down the pile due to eddy currents. Try to drop a magnet in a non ferrous pipe and you will see the effect.
The magnet next to the brass plate will be going up!!! Thats what lifts the pile-driver head. After the magnet passes over the sprocket to the other side, gravity will pull the pile driver head down in free fall.Noitoen said:The magnet going down next to that brass plate is going to slow down the pile due to eddy currents. Try to drop a magnet in a non ferrous pipe and you will see the effect.
Enter your email address to join: