DICKEYBIRD
Well-Known Member
- Joined
- Sep 27, 2007
- Messages
- 653
- Reaction score
- 46
All this ball-turner talk got me into gear to build another one. I had made a mount to clamp on a die-grinder for the QCTP a while back to use as TP grinder but chickened out and decided not to use it. (Abrasive damage worries.)
I couldn't let all that work go to waste so I used the parts to cobble up a ball-turner using a 2" R-8 shanked boring head. I didn't have any bronze to make the bushings with so I rooted around and found some plastic stuff I think is HDPE.
I turned 2 bushings, using the compound set over to match the R-8 taper for the front one.
The stuff actually works great and the clamp setup allows adjustment of the amount of friction.
I added a simple knurled disc & locknut for a height adjuster and turned a toolholder reamed to fit a 1/4" round HSS toolbit. I used the 1st ball it made on the handle of the tool that made it.
It clamps up nicely and is pretty rigid. The 10-32 bit grub screw is going to replaced by a setscrew to give more clearance when I can get one. Almost hit the chuck with it which would have been a disaster.
It makes nice balls so I'm happy with it.
The
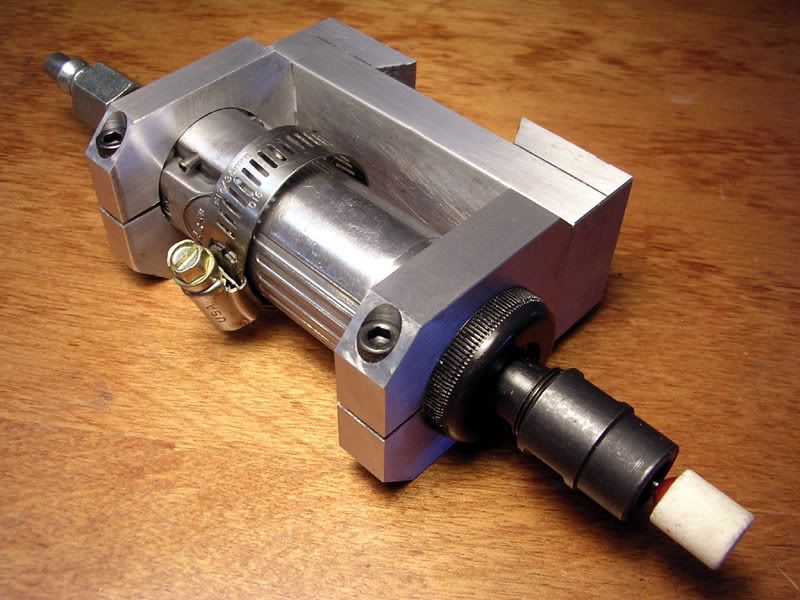
I couldn't let all that work go to waste so I used the parts to cobble up a ball-turner using a 2" R-8 shanked boring head. I didn't have any bronze to make the bushings with so I rooted around and found some plastic stuff I think is HDPE.
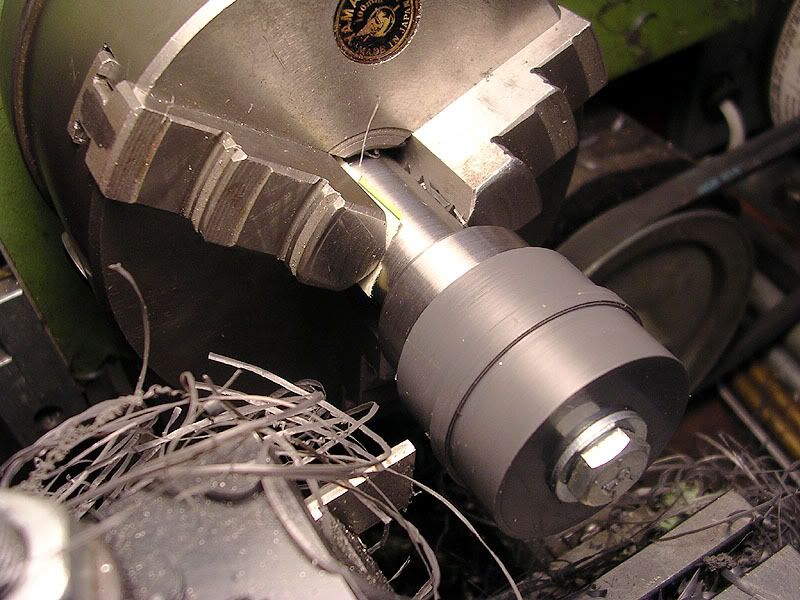
I turned 2 bushings, using the compound set over to match the R-8 taper for the front one.
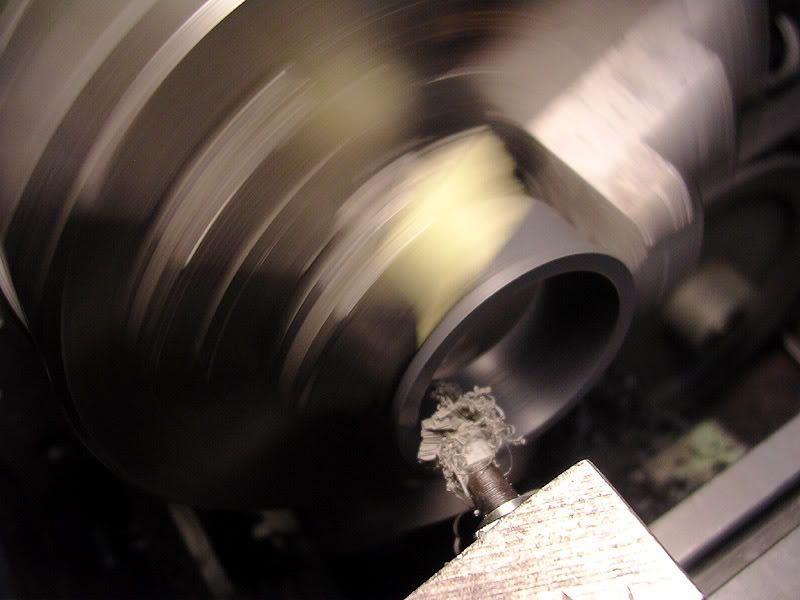
The stuff actually works great and the clamp setup allows adjustment of the amount of friction.
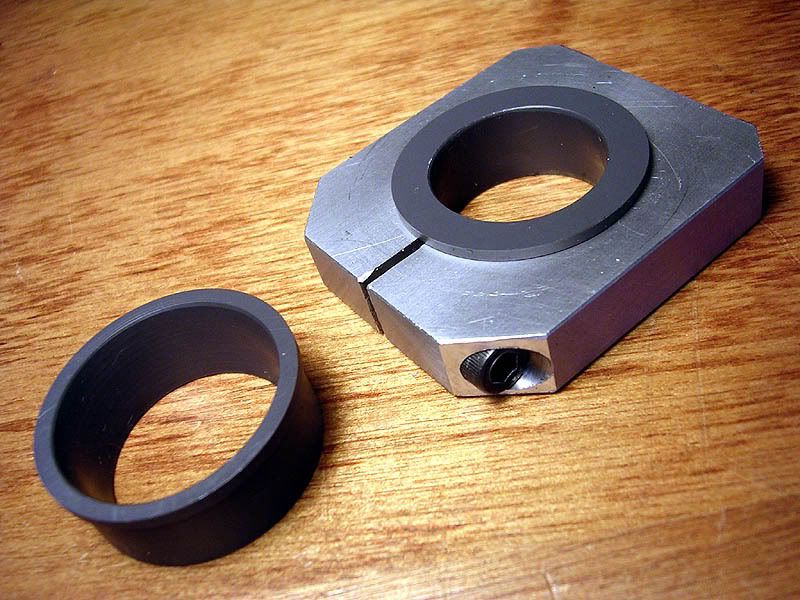
I added a simple knurled disc & locknut for a height adjuster and turned a toolholder reamed to fit a 1/4" round HSS toolbit. I used the 1st ball it made on the handle of the tool that made it.
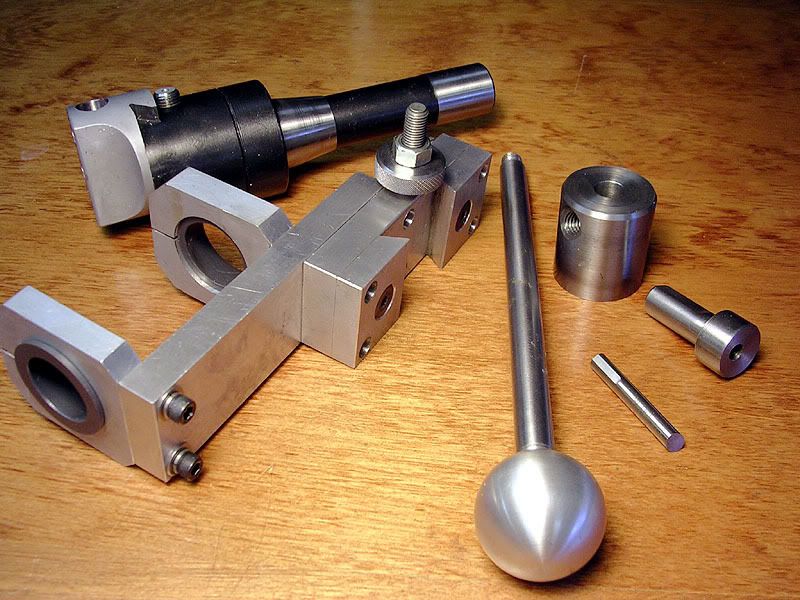
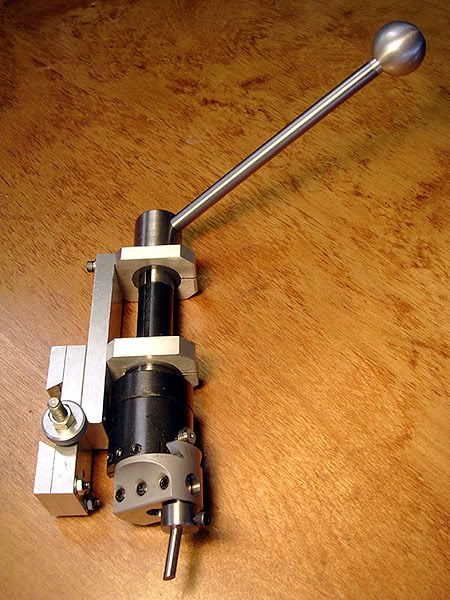
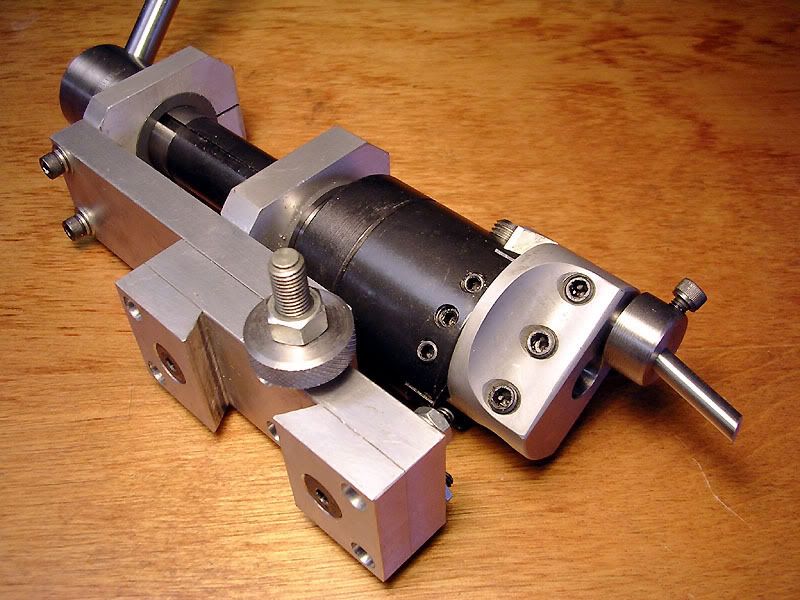
It clamps up nicely and is pretty rigid. The 10-32 bit grub screw is going to replaced by a setscrew to give more clearance when I can get one. Almost hit the chuck with it which would have been a disaster.
It makes nice balls so I'm happy with it.
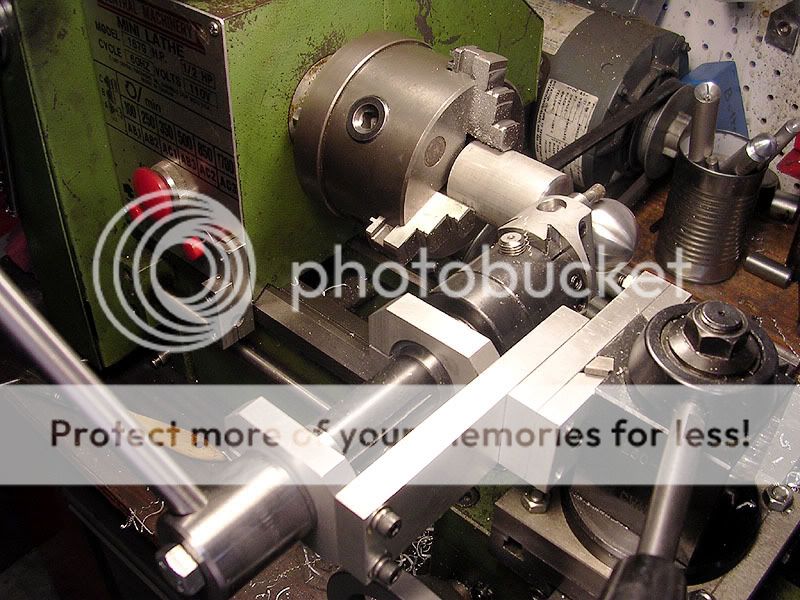
The