J
jpowersny2
Guest
Progress is going a little slower than hoped or anticipated, but that's alright. It's fun making parts twice
.
The bearings that I'm using are 0.500 in diameter. I made a plate that accepts them. I used a 1/2" endmill. It's nearly a perfect fit...the keyword being "nearly". There is a very small amount of play that I'm not happy with. I'd rather press fit the bearings in so that there is no play at all. My plan is to make a new plate open up the recess by boring it on the lathe. But, what diameter should the recess be for a snug fit...steel into aluminum?
Here's what I have so far:
prev. thread: http://www.homemodelenginemachinist.com/index.php?topic=968.0
The bearings that I'm using are 0.500 in diameter. I made a plate that accepts them. I used a 1/2" endmill. It's nearly a perfect fit...the keyword being "nearly". There is a very small amount of play that I'm not happy with. I'd rather press fit the bearings in so that there is no play at all. My plan is to make a new plate open up the recess by boring it on the lathe. But, what diameter should the recess be for a snug fit...steel into aluminum?
Here's what I have so far:
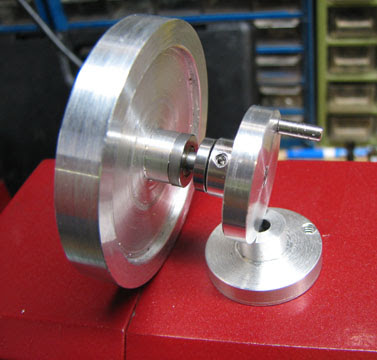
prev. thread: http://www.homemodelenginemachinist.com/index.php?topic=968.0