Oldmechthings
Well-Known Member
- Joined
- Jan 10, 2008
- Messages
- 153
- Reaction score
- 12
How do you machine triangular lobed cams for one of Elmer Verburg's Paddle Wheel Engines? Well, first you clamp a bar of metal in a wobble fixture and machine it skiwompus.
Then you put it in a regular three jaw chuck, and drill and ream the bore, turn the shoulder for the hub, and part it off.
Here are the finished cams, just 5/8" across, nestled in their respective cam followers. The shape provides a quick action to the steam valve at each end of the piston stroke. The unique thing about them is that they maintain contact with both sides of the follower through out their rotation. (With a couple thousands clearance taken into consideration)
For something that out of round, that is pretty amazing if you ask me. But nobody asked me.
Birk
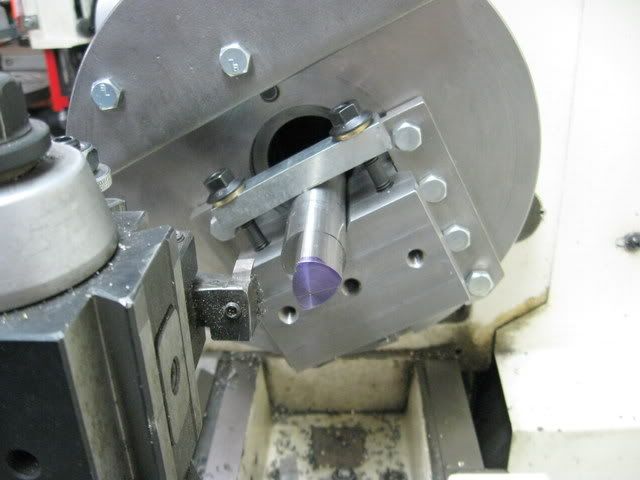
Then you put it in a regular three jaw chuck, and drill and ream the bore, turn the shoulder for the hub, and part it off.
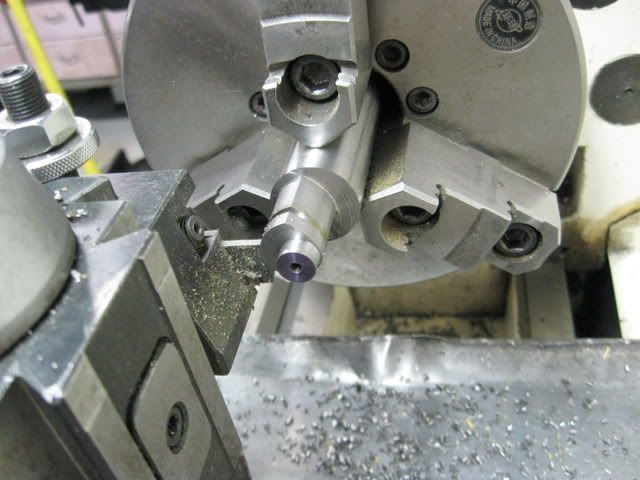
Here are the finished cams, just 5/8" across, nestled in their respective cam followers. The shape provides a quick action to the steam valve at each end of the piston stroke. The unique thing about them is that they maintain contact with both sides of the follower through out their rotation. (With a couple thousands clearance taken into consideration)
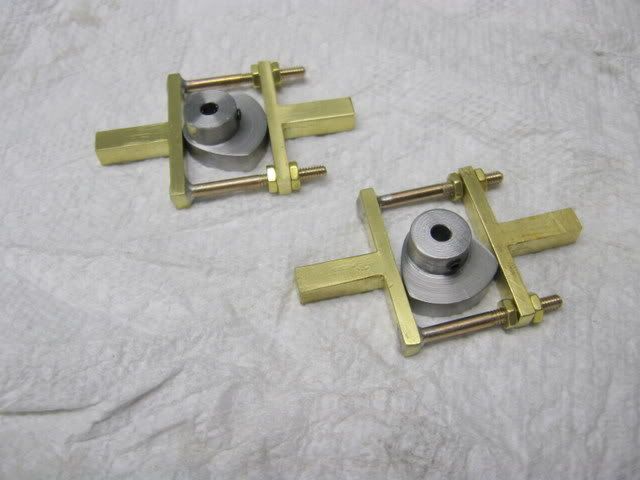
For something that out of round, that is pretty amazing if you ask me. But nobody asked me.
Birk