- Joined
- Jan 17, 2009
- Messages
- 887
- Reaction score
- 81
Hi Chaps
I've just finished building a tool post grinder, in the UK they are scarce as rocking horse s***, I've been on the look out for one for ages in the end I decided to make my own.
This is a sketch of the spindle
Turning the centre shaft betwen centres
Screw cutting the housing for the end caps
Completed spindle
Boring out the mounting brackets
Milling the 3/16 dia groove for the belting in the pulley
My first idea was to use a sewing machine motor to drive it but it just didn't have enough humph.
Then a friend gave me an unwanted router with a 850w variable speed motor 12000 rpm to 26000rpm.
This is it mounted for use
Grinding up some centre punches
And the result, nice and sharp with a cracking finish, this will be a real handy bit of kit.
Cheers
Stew
I've just finished building a tool post grinder, in the UK they are scarce as rocking horse s***, I've been on the look out for one for ages in the end I decided to make my own.
This is a sketch of the spindle
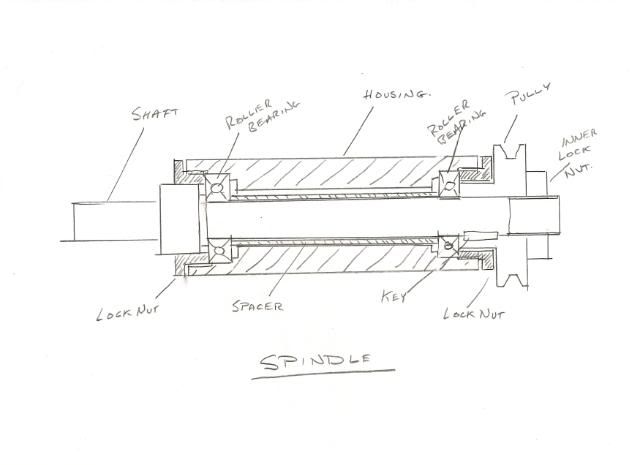
Turning the centre shaft betwen centres
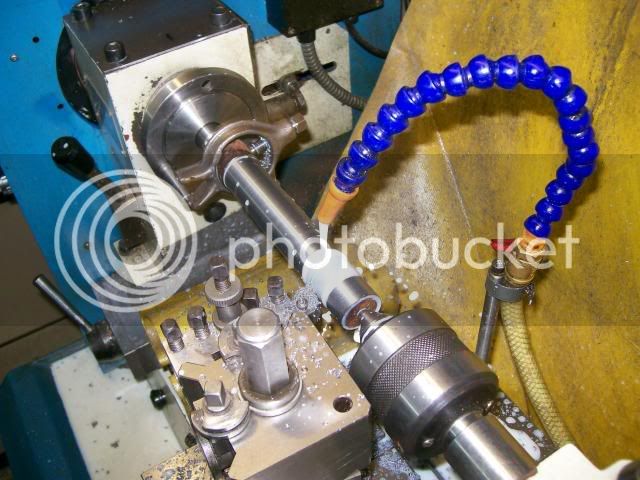
Screw cutting the housing for the end caps
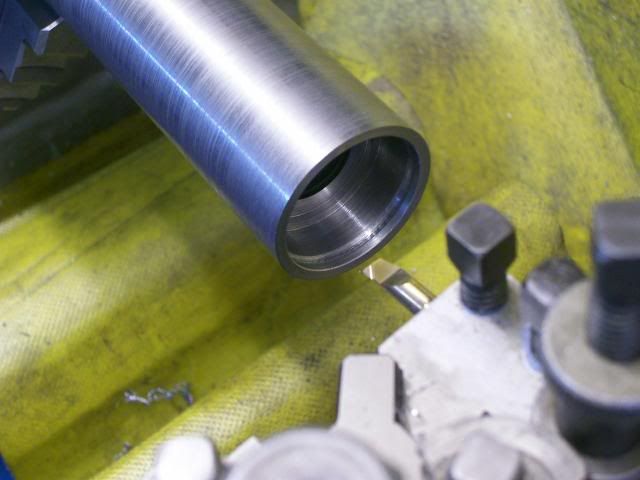
Completed spindle
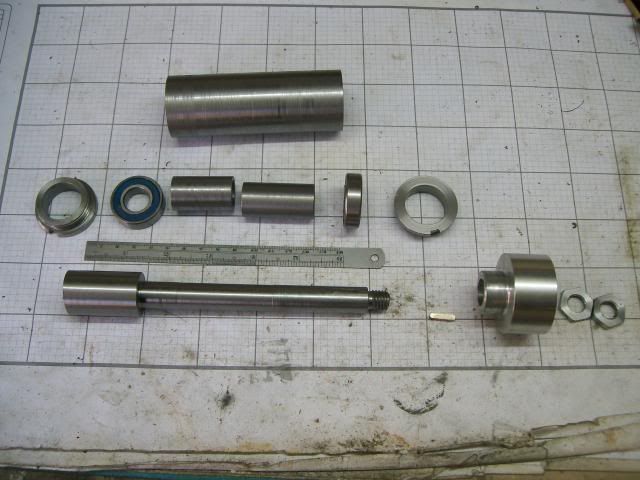
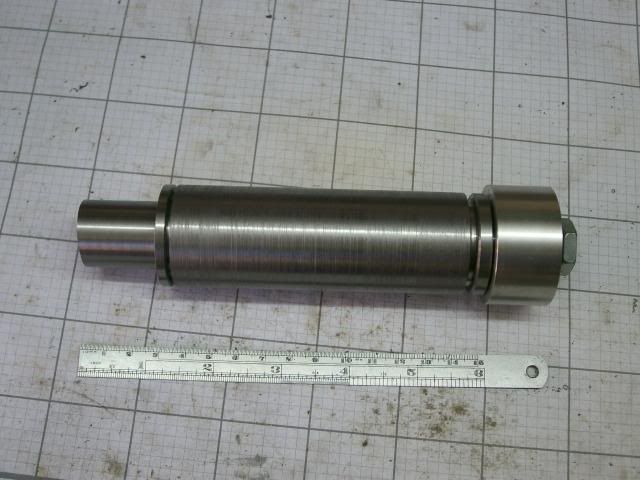
Boring out the mounting brackets
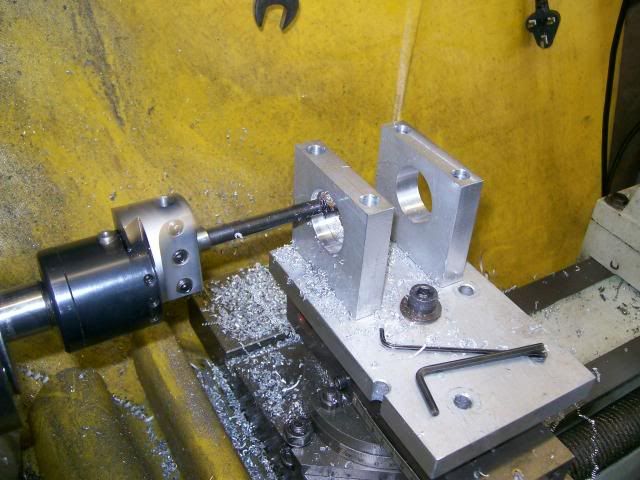
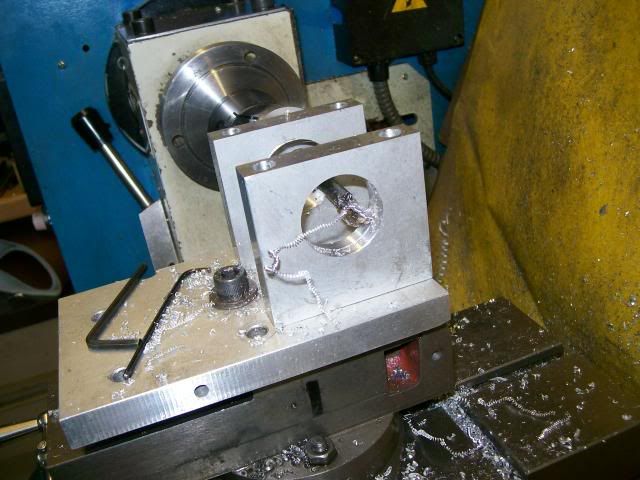
Milling the 3/16 dia groove for the belting in the pulley
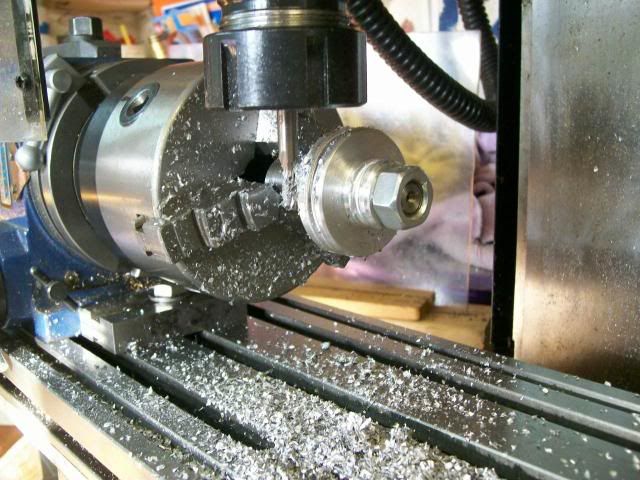
My first idea was to use a sewing machine motor to drive it but it just didn't have enough humph.

Then a friend gave me an unwanted router with a 850w variable speed motor 12000 rpm to 26000rpm.
This is it mounted for use
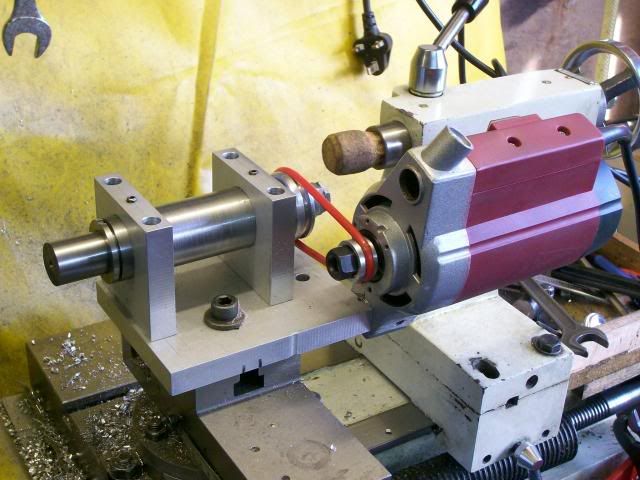
Grinding up some centre punches
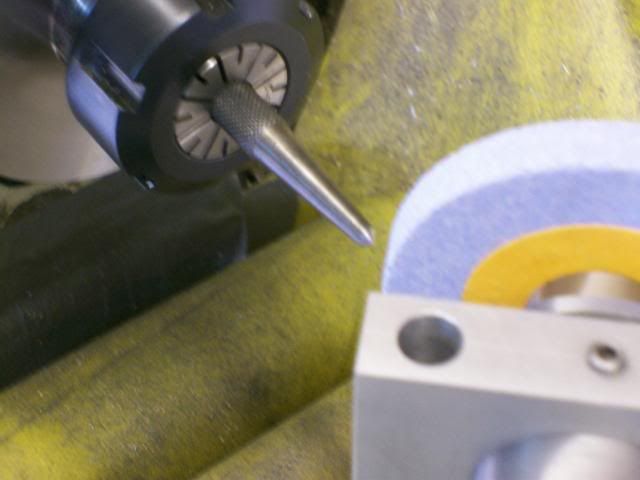
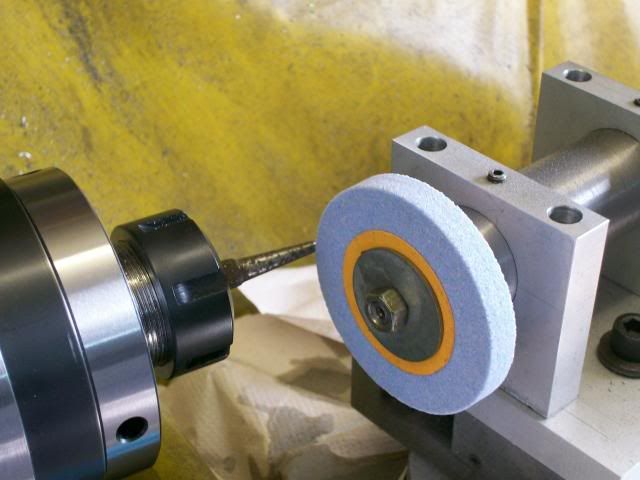
And the result, nice and sharp with a cracking finish, this will be a real handy bit of kit.
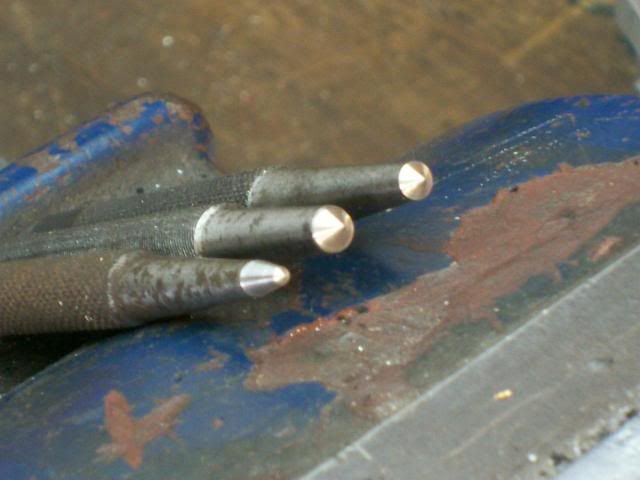
Cheers
Stew