- Joined
- Dec 5, 2009
- Messages
- 510
- Reaction score
- 47
Hi,
This is a nice forum to share our projects.
I've been into homeshop machining as a hobby, among many other hobbies, for around 7 years now.
I started out making all kinds of tooling and small repair parts, then about 2 years ago I got interested in designing and building mechanical projects.
So I looked on the inernet to see a animation of how a steam engine works, and after finding the concept, I got on my cad program and designed my own from scratch.
it is a double acting classic steam engine, it was a lot of learning experiance to get it wotking did a lot of reworking and rebuilding until I finally got it to work,
but once I did then the rest of the engines after became easier to get running on the first or second try.
I have a 7 x 10 mini lathe, and a Micro-mill drill, (harbor freight) and a 4x6 bandsaw and a small benchtop metal bandsaw. Benchtop grinder, and drill press. Among other tooling and such.
Here is the first one.
second one, this runs forward and reverse, depending on wich side air is intaked.
third one, this one is not the steam engine concept, but works with valves and rocker arms, pushrods, still a steam (compressed air engine) just a inter comb. engine concept.
This is a poor design for the intake valve, due to high pressure intake, causes the intake valve to remain pushed down into the cykinder, that's why a heavy valve spring on the one side and a lite spring on the exhaust.
Works good just can't over work the air intake.
Fourth engine, learned from my mistake with the intake valve and designed a intake valve system that does not enter into the cylinder, but the air is routed around it when depressed in it's own compartment, this is the best running yet, it is self starting when air is applied, even has a throttle.
another view.
And this one I am currently working on on weekends,
it is a horizontal 4 cyl. engine, an aircrafty type concept.
Thankyou.
For letting me share.
and
Merry Christmas
God Bless...
This is a nice forum to share our projects.
I've been into homeshop machining as a hobby, among many other hobbies, for around 7 years now.
I started out making all kinds of tooling and small repair parts, then about 2 years ago I got interested in designing and building mechanical projects.
So I looked on the inernet to see a animation of how a steam engine works, and after finding the concept, I got on my cad program and designed my own from scratch.
it is a double acting classic steam engine, it was a lot of learning experiance to get it wotking did a lot of reworking and rebuilding until I finally got it to work,
but once I did then the rest of the engines after became easier to get running on the first or second try.
I have a 7 x 10 mini lathe, and a Micro-mill drill, (harbor freight) and a 4x6 bandsaw and a small benchtop metal bandsaw. Benchtop grinder, and drill press. Among other tooling and such.
Here is the first one.
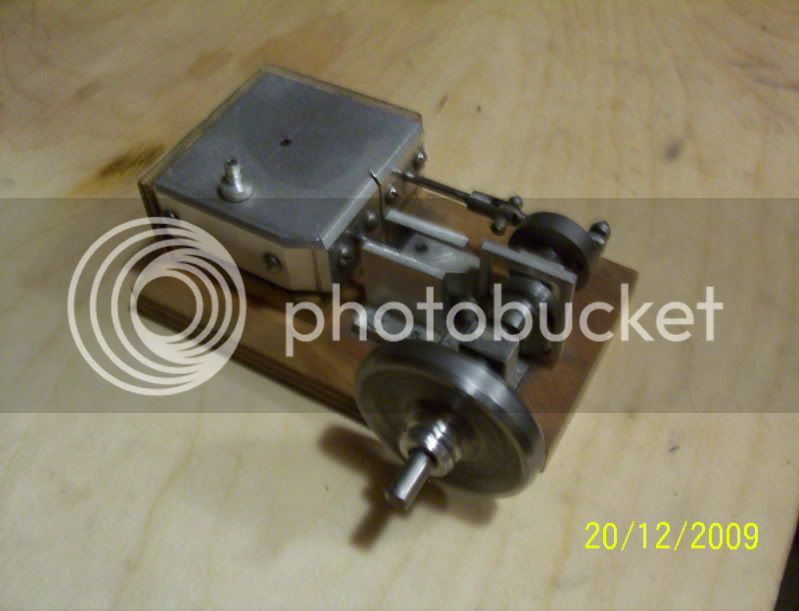
second one, this runs forward and reverse, depending on wich side air is intaked.
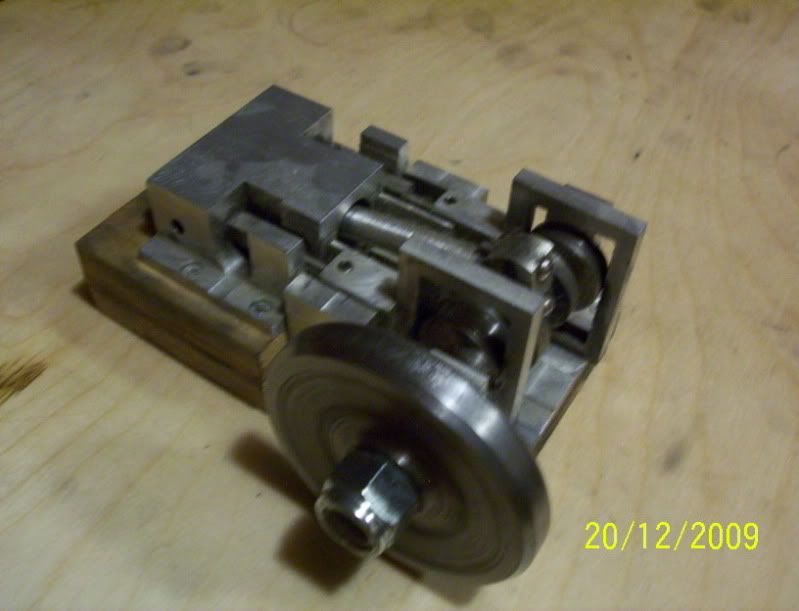
third one, this one is not the steam engine concept, but works with valves and rocker arms, pushrods, still a steam (compressed air engine) just a inter comb. engine concept.
This is a poor design for the intake valve, due to high pressure intake, causes the intake valve to remain pushed down into the cykinder, that's why a heavy valve spring on the one side and a lite spring on the exhaust.
Works good just can't over work the air intake.
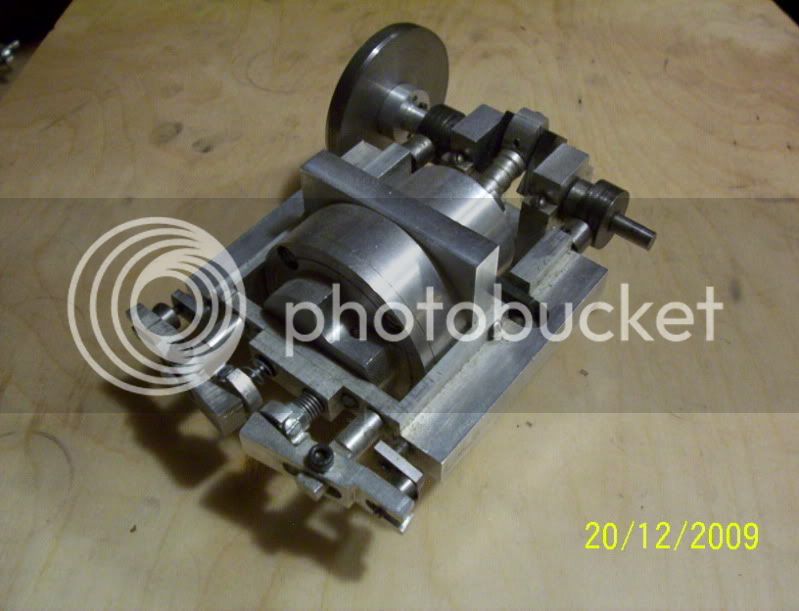
Fourth engine, learned from my mistake with the intake valve and designed a intake valve system that does not enter into the cylinder, but the air is routed around it when depressed in it's own compartment, this is the best running yet, it is self starting when air is applied, even has a throttle.
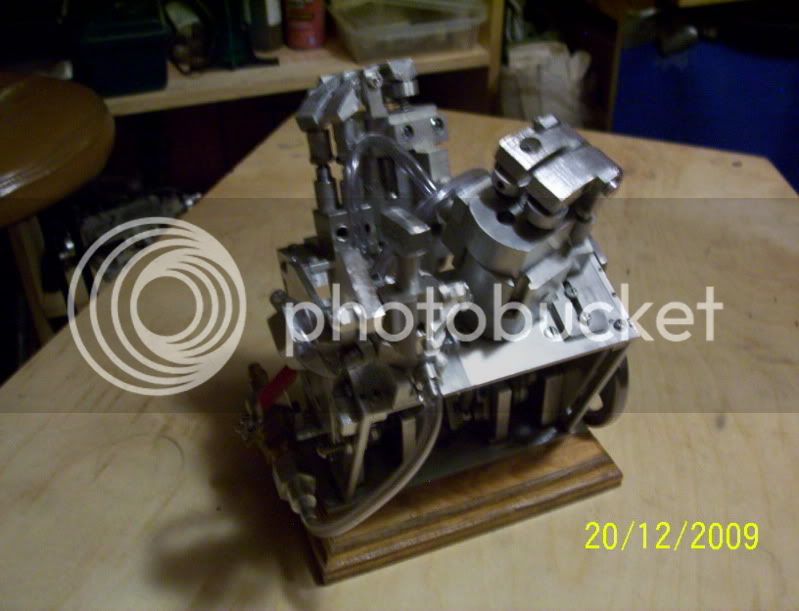
another view.
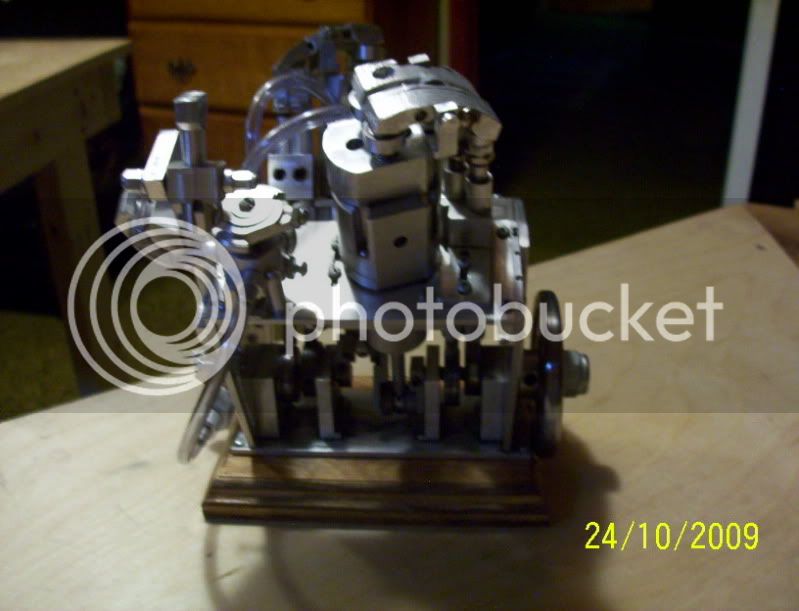
And this one I am currently working on on weekends,
it is a horizontal 4 cyl. engine, an aircrafty type concept.
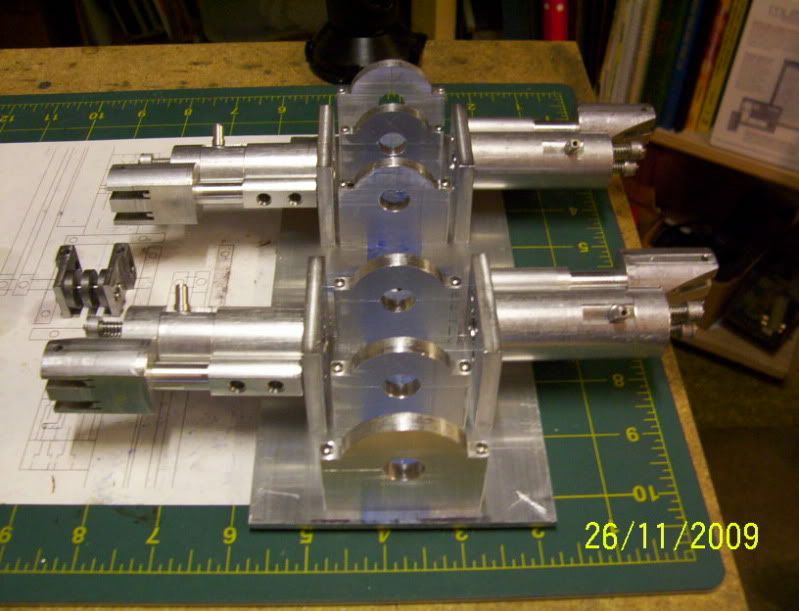
Thankyou.
For letting me share.
and
Merry Christmas
God Bless...