Kaleb
Senior Member
- Joined
- Jan 3, 2010
- Messages
- 272
- Reaction score
- 27
I've decided it's time to tackle building an engine from castings. So when this set came up on eBay, I thought it was just the thing to start with. Well, after waiting around 6 weeks, it finally showed up.
The designer's impression
The raw castings
A list of all the parts
A view of the cylinder dimensions on the plans. 7/16" (approx. 11.1mm) bore and stroke.
Since the Jacob's chuck I have for my lathe can only take up to a 7mm drill, there won't be much room for a boring bar in there. So I bought this exquisite little Micro 100 from John Buckley. Paid a good $50, that's quality tooling for you!
This one should beep me busy for a good while, but hopefully it will be a little ripper of an engine if all goes to plan.
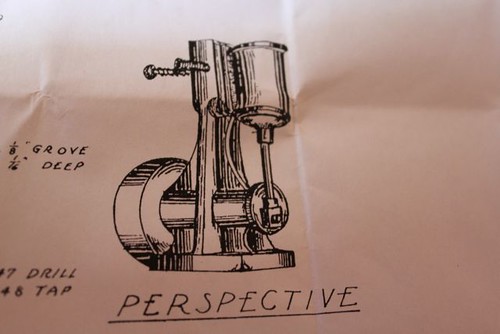
The designer's impression
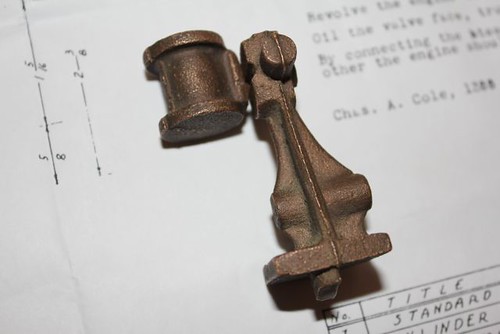
The raw castings
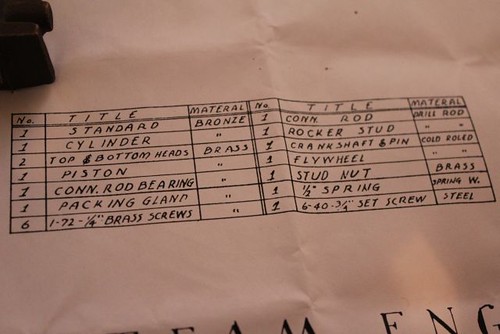
A list of all the parts
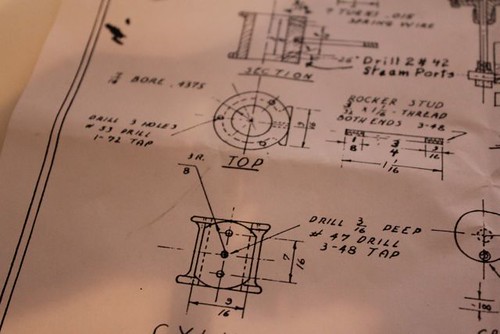
A view of the cylinder dimensions on the plans. 7/16" (approx. 11.1mm) bore and stroke.

Since the Jacob's chuck I have for my lathe can only take up to a 7mm drill, there won't be much room for a boring bar in there. So I bought this exquisite little Micro 100 from John Buckley. Paid a good $50, that's quality tooling for you!
This one should beep me busy for a good while, but hopefully it will be a little ripper of an engine if all goes to plan.