rake60
Well-Known Member
- Joined
- Jul 8, 2007
- Messages
- 4,756
- Reaction score
- 124
It had been a while since I cut a thread on the lathe so I decided to play
a bit. On the way down to the shop I got to thinking about trying to
see how small a thread I might be able to cut. My threading tool was too
big for anything too small, so I ground a smaller tool.
I started with a 10-32 on brass. The tool cut fairly well on its first attempt.
The fact that the 10-32 nut screwed on with very little slop was an encouragement.
I have a feeling this will keep me entertained for a while trying to see just
how small I can get it to go.
In my experience a cut thread is almost always cleaner than any die can make, but
speed that tool is moving toward the chuck on the small parts is a little unnerving.
Rick
a bit. On the way down to the shop I got to thinking about trying to
see how small a thread I might be able to cut. My threading tool was too
big for anything too small, so I ground a smaller tool.
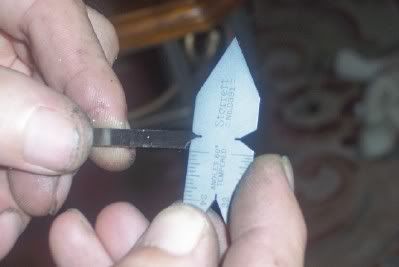
I started with a 10-32 on brass. The tool cut fairly well on its first attempt.
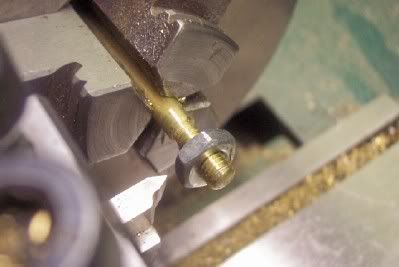
The fact that the 10-32 nut screwed on with very little slop was an encouragement.
I have a feeling this will keep me entertained for a while trying to see just
how small I can get it to go.
In my experience a cut thread is almost always cleaner than any die can make, but
speed that tool is moving toward the chuck on the small parts is a little unnerving.
Rick