arnoldb said:a libation of Namibia's finest should add to the mollifying effect.
Three in fact Arnold.
Just get back on the horse........
Finished the the distributor axles.
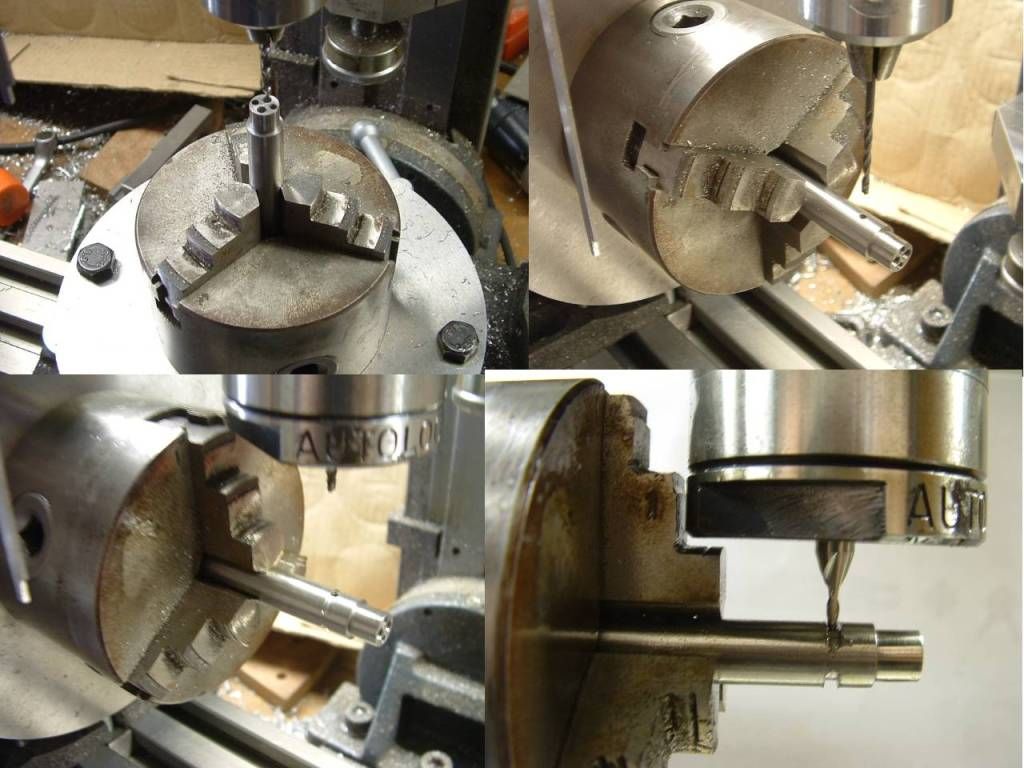
Top left - drilling the ports & M3 mounting holes.
Then stand the RT upright without removing the part to retain angular alignment - a PITB as you have two parts to do but definately the safest way.
Top right drilling the port cross hole.
Bottom left machining the annulus groove 120° either side.
Bottom right - plan ahead. I have done this before where after meticulously clocking up the work etc. you then find you can't gain access with the cutter - lesson learned.
The finished axle(s).
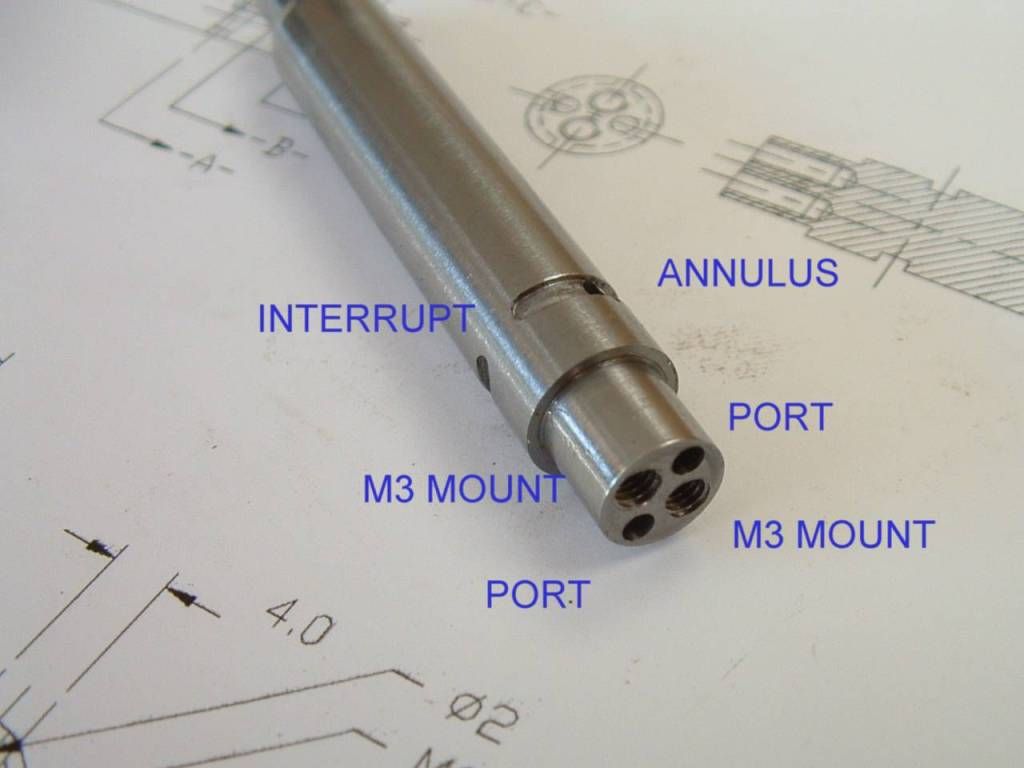
Trial assembly of the cylinders - its starting to look like an elbow engine.
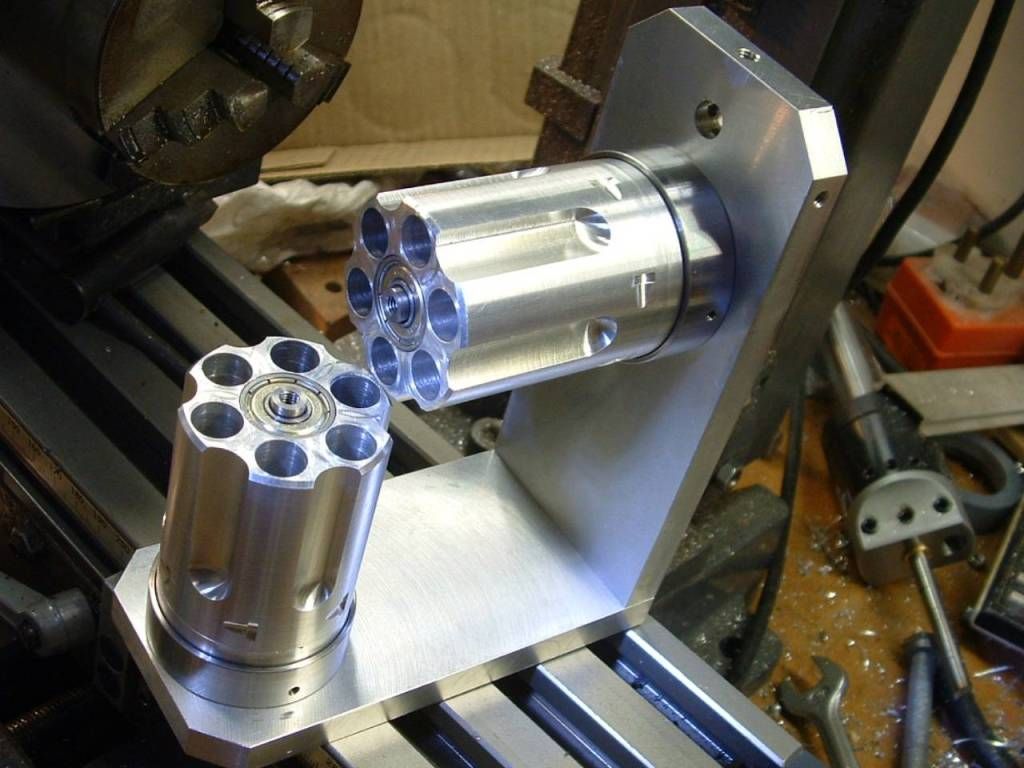
So far so good now for the stiffener bracket.
For some reason I've been putting off the "production run" of 12 pistons, 12 elbow axles, 12 elbow shoulders and 6 elbow assemblies - likely to get monotonous.
I've got an ER collet chuck on order which will help - should arive Thursday so I'll probably do the pistons over the weekend.
Ken