Captain, its 10mm bore by 30mm stroke (the PCD).
Here's the design as I'm probably going to build it.
I have incorporated seals for the axle and "O" ring grooves for the pistons. I'll build it without the seals initially to get everything sorted out first - then we'll see if the engine can handle the friction of all those seals.
If it all works the only places it can leak is out the exhaust (anulus interrupt bypass) and up the 4mm diameter x 30mm long "bearing" portion of the elbow that the piston turns on - this should be very little and lube sealed.
The axle seal is not a pressure seal but should handle 100 psi easilly enough (I once in an act of wishfull thinking subjected one of these to 2000 psi - it failed after a couple of hours use - I expected it would turn inside out instantly).
I'm going to go with 2mm spring steel elbows silver soldered into the piston "axles" - I'll be making a jig to hold both axles in the correct position during soldering - so with a bit of luck they should come out spot on - the flex and torsion in the spring steel wire should be more than ample to drive the motor but light enough to accomodate any errors without undue side loading friction.
Noitoen - if that doesn't work I'll definately try PTFE pistons.
Here's the design as I'm probably going to build it.
I have incorporated seals for the axle and "O" ring grooves for the pistons. I'll build it without the seals initially to get everything sorted out first - then we'll see if the engine can handle the friction of all those seals.
If it all works the only places it can leak is out the exhaust (anulus interrupt bypass) and up the 4mm diameter x 30mm long "bearing" portion of the elbow that the piston turns on - this should be very little and lube sealed.
The axle seal is not a pressure seal but should handle 100 psi easilly enough (I once in an act of wishfull thinking subjected one of these to 2000 psi - it failed after a couple of hours use - I expected it would turn inside out instantly).
I'm going to go with 2mm spring steel elbows silver soldered into the piston "axles" - I'll be making a jig to hold both axles in the correct position during soldering - so with a bit of luck they should come out spot on - the flex and torsion in the spring steel wire should be more than ample to drive the motor but light enough to accomodate any errors without undue side loading friction.
Noitoen - if that doesn't work I'll definately try PTFE pistons.
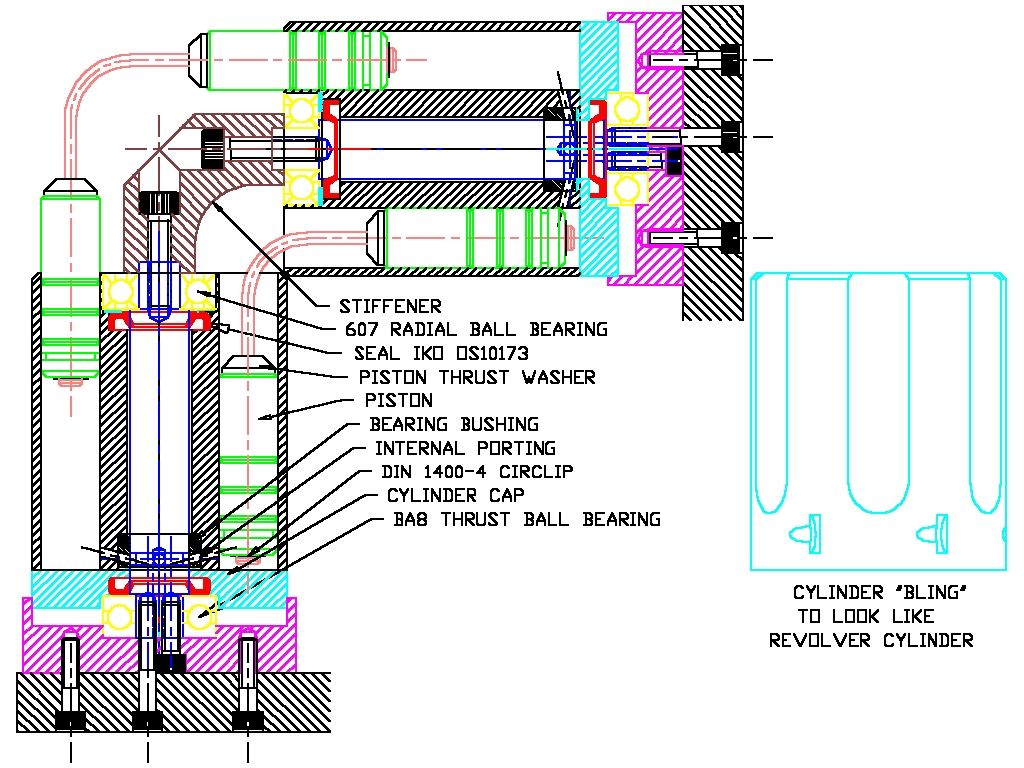