I have a Sieg X2 Mill, which has given me great pleasure.
After purchasing, I have added belt-drive and some cheap DRO. Also changed one of the bearings on the spindle, but have some fine tuning to go before the machine is deadon,- too much runout on the spindle.
However, there is another problem. Sometimes, the motor will not start when turning the button. Sometimes I will spend as much as 10 minutes before it starts. I have tried to clean/change the brushes, and also done some research on the net. It seems that the motor-controller might be the defective part. However, sometimes the motor will start and run just fine. On other occasions it will have hiccups, meaning varying RPM. But most of the times when it has started, it will run just fine.
From the other writeups on the net, I have found detailed instructions on how to perform tests to locate the faulty part. However, I have not been able to find documentation on a board identical to mine. If someone could offer a hint to where I could find specific information on my board, or how to test which components, that would be most appreciated. I have very limited skills on electronical devices, but have built my own transmitters, and similar, from kits.
The machine during maintenance(why do pictures rotate 90* during internet-travel ???)
The motor-controller
Thx in advance,
Ed
After purchasing, I have added belt-drive and some cheap DRO. Also changed one of the bearings on the spindle, but have some fine tuning to go before the machine is deadon,- too much runout on the spindle.
However, there is another problem. Sometimes, the motor will not start when turning the button. Sometimes I will spend as much as 10 minutes before it starts. I have tried to clean/change the brushes, and also done some research on the net. It seems that the motor-controller might be the defective part. However, sometimes the motor will start and run just fine. On other occasions it will have hiccups, meaning varying RPM. But most of the times when it has started, it will run just fine.
From the other writeups on the net, I have found detailed instructions on how to perform tests to locate the faulty part. However, I have not been able to find documentation on a board identical to mine. If someone could offer a hint to where I could find specific information on my board, or how to test which components, that would be most appreciated. I have very limited skills on electronical devices, but have built my own transmitters, and similar, from kits.
The machine during maintenance(why do pictures rotate 90* during internet-travel ???)
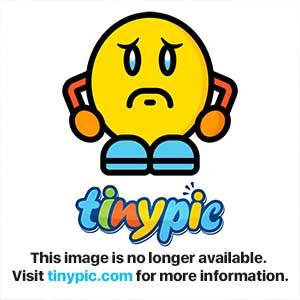
The motor-controller
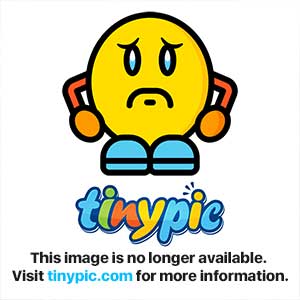
Thx in advance,
Ed