- Joined
- Dec 2, 2008
- Messages
- 971
- Reaction score
- 8
I haven't been in the shop for weeks but today I had a few free hours so I went to the shop intent on making the D-valve for the vertical overcrank engine. I got a piece of cast iron cut down to size and milled the valve cavity with no problems. Then I turned the part over in the vice with the intention of milling two 1/8" slots across the top for the valve rod and the nut. I was using a 1/8" 4 flute solid carbide end mill and after I got centered on the coordinates for the first slot, I backed the cutter away fro the edge, lowered the bit below the top edge and brought it up close to check the depth of cut, locked the X-axis and turned on the mill.
SNAP!
I had brought the cutter too close to the edge and that was that. I yell " No...wait" but I was to late, the end mill was toast. My last 1/8" cutter, broken clean at the top of the flutes. I had another free hour, not enough time to start another job, and I was THAT! close to finishing this one.
:noidea: How about grinding a new end mill out of the broken stub? Using a diamond wheel, I ground the end flat and then ground a diagonal flat, just like a D-bit reamer. I hadn't moved the setup so it took just a few seconds to remount the cutter, and set a .010" DOC and start the cut. To my great surprise, the cut was free and easy, with no pounding and no chatter. I still had about .250" to go so I increased the DOC to .020 and the second pass was as easy as the first. I didn't increase the DOC any more, for fear of breaking my new cutter. I just made repeated passes at about .020 to reach final depth. I then set up on the Y-coordinate and locked the X to make the slot for the nut. Ten more passes and the job was done.
I hadn't thought about taking a picture during the process but I did get a finished picture of the part and the bit. Here it is poor focus and bad lighting but you can get the idea.
The cast iron was salvaged from a piece of scrap that had two tapped holes in a location that does not affect the function of the part and will be cleaned up with a file later. That's all I had time for.
Jerry
SNAP!
I had brought the cutter too close to the edge and that was that. I yell " No...wait" but I was to late, the end mill was toast. My last 1/8" cutter, broken clean at the top of the flutes. I had another free hour, not enough time to start another job, and I was THAT! close to finishing this one.
:noidea: How about grinding a new end mill out of the broken stub? Using a diamond wheel, I ground the end flat and then ground a diagonal flat, just like a D-bit reamer. I hadn't moved the setup so it took just a few seconds to remount the cutter, and set a .010" DOC and start the cut. To my great surprise, the cut was free and easy, with no pounding and no chatter. I still had about .250" to go so I increased the DOC to .020 and the second pass was as easy as the first. I didn't increase the DOC any more, for fear of breaking my new cutter. I just made repeated passes at about .020 to reach final depth. I then set up on the Y-coordinate and locked the X to make the slot for the nut. Ten more passes and the job was done.
I hadn't thought about taking a picture during the process but I did get a finished picture of the part and the bit. Here it is poor focus and bad lighting but you can get the idea.
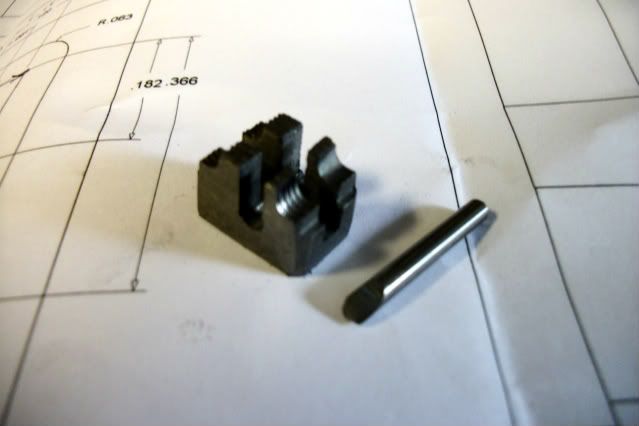
The cast iron was salvaged from a piece of scrap that had two tapped holes in a location that does not affect the function of the part and will be cleaned up with a file later. That's all I had time for.
Jerry