Hello all. I am beginning my first engine build and have decided to share it with everyone on the forum. I first became interested because of my long standing interest in Stirling Engines. The decision was made to start James R. Senft's "Tapper". For those unfamiliar, it is a Ringbom style Stirling engine. The plans are featured in Senft's book shown below.

Some basics about the engine: 1.75" diameter flywheel, 1/2" piston diameter, 5/8" piston stroke, 2cc piston swept volume. I began by making the piston and cylinder. Next I made the flywheel. I have shown pictures of the parts so far.
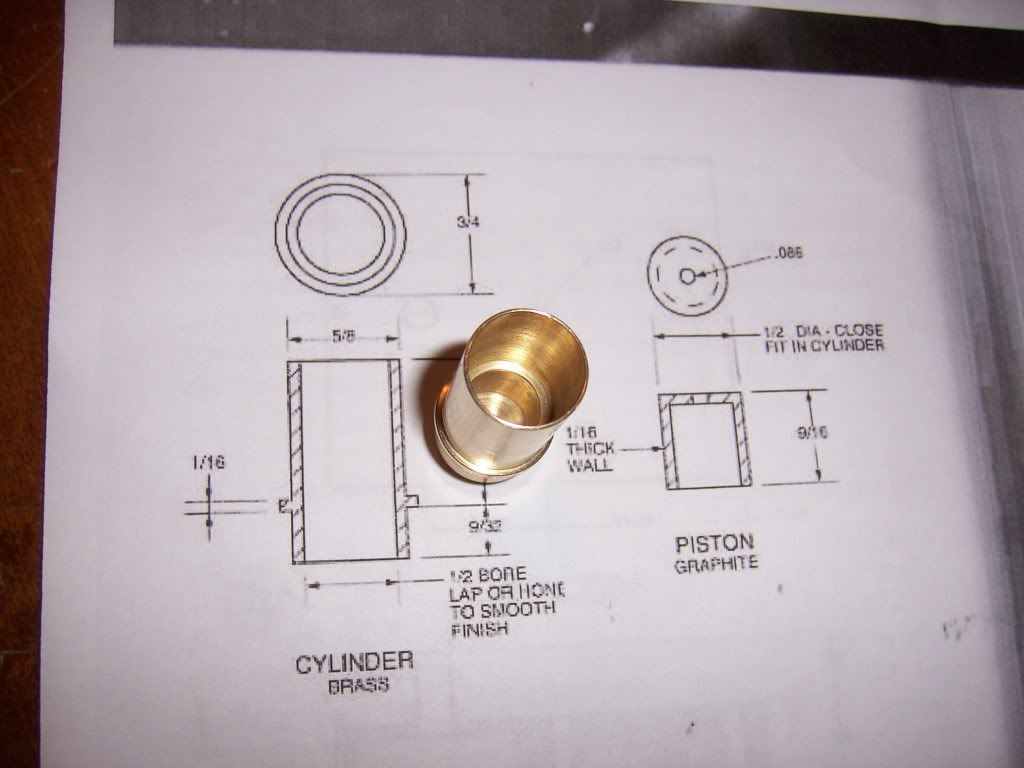
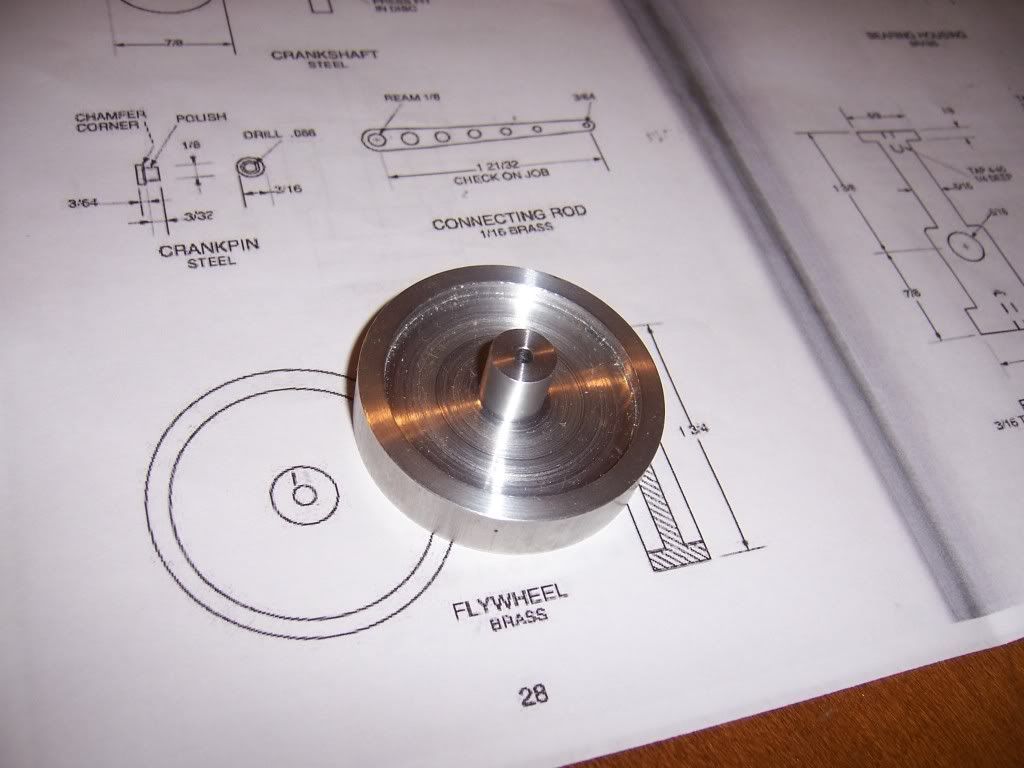
Lastly, I have included a video of the testing of my piston cylinder set. I have read that it is important that the piston fall through the cylinder by it's own weight; however, when one end is sealed, the piston must be reasonably air tight. In order to test this I put a puddle of water on the counter. Next, I place the cylinder in the puddle creating an air seal. When the piston is placed in the cylinder it does not move. When the cylinder is lifted, the seal is broken and the piston falls through to the bottom.
[youtube=425,350]<object width="425" height="344"><param name="movie" value="http://www.youtube.com/v/fwStIOO33i8&hl=en_US&fs=1&"></param><param name="allowFullScreen" value="true"></param><param name="allowscriptaccess" value="always"></param><embed src="http://www.youtube.com/v/fwStIOO33i8&hl=en_US&fs=1&" type="application/x-shockwave-flash" allowscriptaccess="always" allowfullscreen="true" width="425" height="344"></embed></object>[/youtube]
Next Time: Bearing Housing, Cylinder Cap, Cylinder Retaining Ring.