Generatorgus
Senior Member
- Joined
- Feb 25, 2010
- Messages
- 362
- Reaction score
- 166
This is a drive gear for my camper jack power unit. Evidently a lousy press fit, as the pinion spins inside the larger gear. I had no problem separating them. My first though was to silver solder, as they are both made of steel, but I'm thinking the heat might ruin things. Second thought is a straight knurl and repress it, or maybe pin it.
The company, Rieco, say they don't sell parts and will only sell a new power head at the tune of $315 plus shipping.
The unit is 3 months out of warranty.
The large gear is about 3" dia. and is identical both sides. The pinion shaft is about 3/8", that's a guess, I didn't measure them.
The large gear is driven by the motor unit, the pinion drives another gear linked to the worm drive of the jack. The jacks are rated for 2500 lb., this particular jack was on the rear of my truck camper and only lifts about700 lb. or so. Oddly enough it started slipping as I was lowering the camper.
GUS
The company, Rieco, say they don't sell parts and will only sell a new power head at the tune of $315 plus shipping.
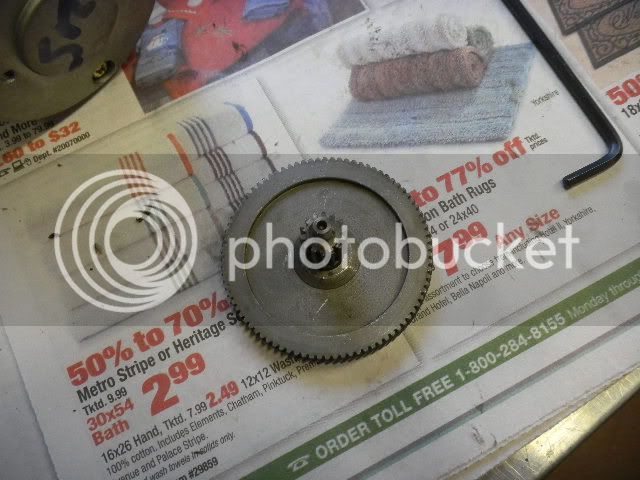
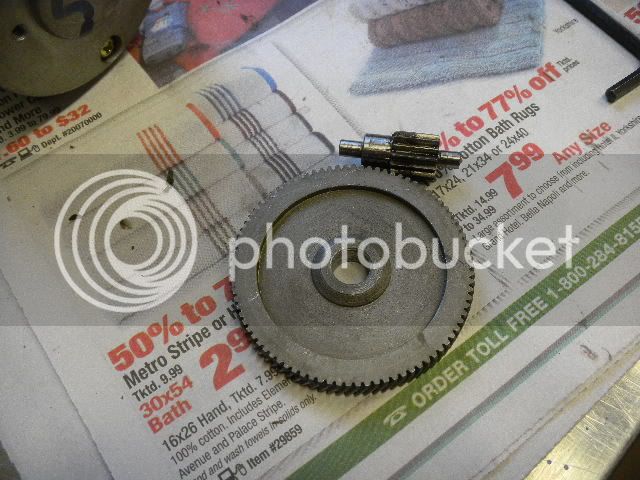
The large gear is about 3" dia. and is identical both sides. The pinion shaft is about 3/8", that's a guess, I didn't measure them.
The large gear is driven by the motor unit, the pinion drives another gear linked to the worm drive of the jack. The jacks are rated for 2500 lb., this particular jack was on the rear of my truck camper and only lifts about700 lb. or so. Oddly enough it started slipping as I was lowering the camper.
GUS