While ago I snapped the lathe spindle, being a tad to aggressive with this little hobbly lathe (AA109)
Not being the first time I've bent or broke a part I set out to see if the lathe was big enough to make its own spindle. Just enough room, so down goes a hunk of 1144 to resemble a spindle shaft.
This thing is only .550 in dia and the 109 is awfull about tapers so much tapping on the tailstock was in order till the point was reached to which this last skim left me with a shaft that measured .550 along its length.
A little 600 grit paper polish and it fit just fine in the headstock. Now to cut the threads for the chuck itself. Brought to size the nose at 0.750", set the change gears for the 16tpi required and made a scratch cut to ensure clearance. So far so good,
Somewhere the mind went on vacation. Rather than feed the bit in a little, make the cut, stop machine, back out cutter, reverse machine (not enough room to use Thread Dial) I made a cut, stopped machine and just flipped the tumbler reverse. Well . . . just doesnt work that way to well
Glad I got a 3 foot hunk of that 1144.
Robert
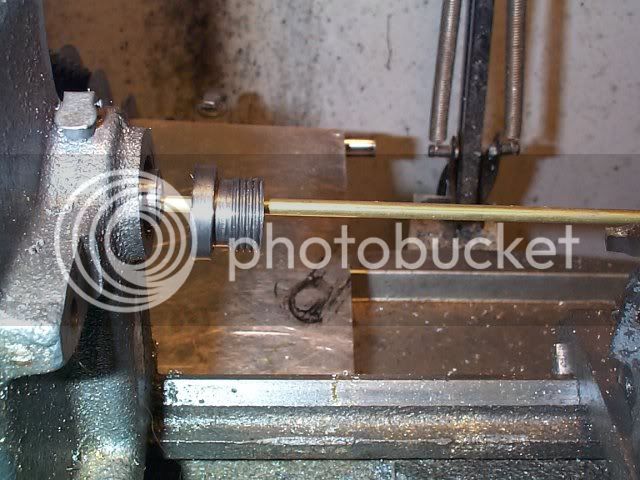
Not being the first time I've bent or broke a part I set out to see if the lathe was big enough to make its own spindle. Just enough room, so down goes a hunk of 1144 to resemble a spindle shaft.
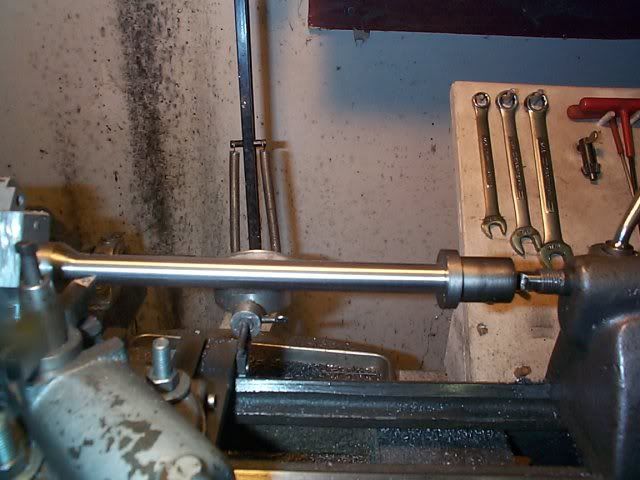
This thing is only .550 in dia and the 109 is awfull about tapers so much tapping on the tailstock was in order till the point was reached to which this last skim left me with a shaft that measured .550 along its length.
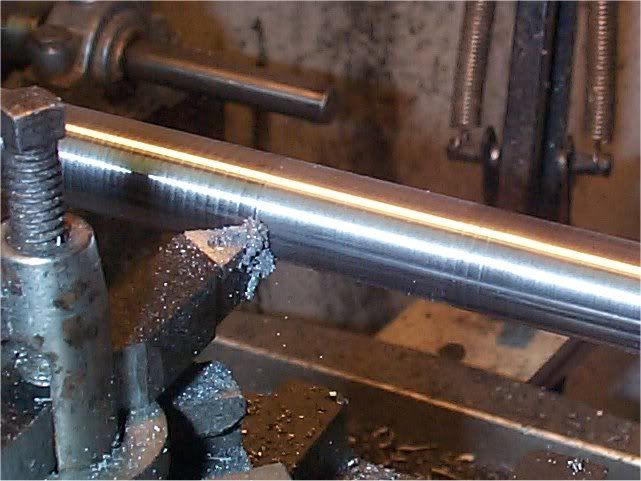
A little 600 grit paper polish and it fit just fine in the headstock. Now to cut the threads for the chuck itself. Brought to size the nose at 0.750", set the change gears for the 16tpi required and made a scratch cut to ensure clearance. So far so good,
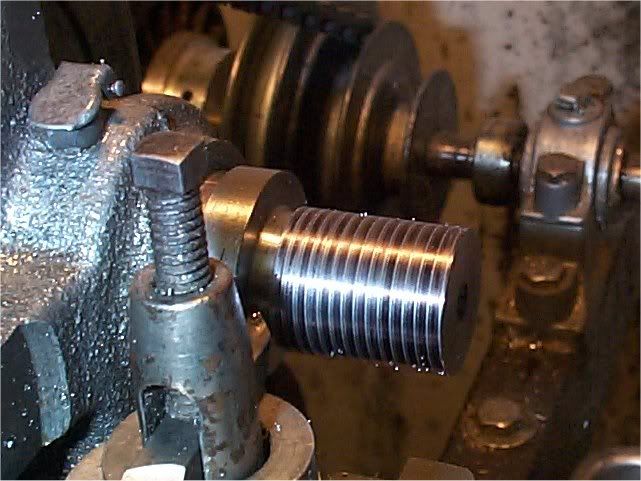
Somewhere the mind went on vacation. Rather than feed the bit in a little, make the cut, stop machine, back out cutter, reverse machine (not enough room to use Thread Dial) I made a cut, stopped machine and just flipped the tumbler reverse. Well . . . just doesnt work that way to well
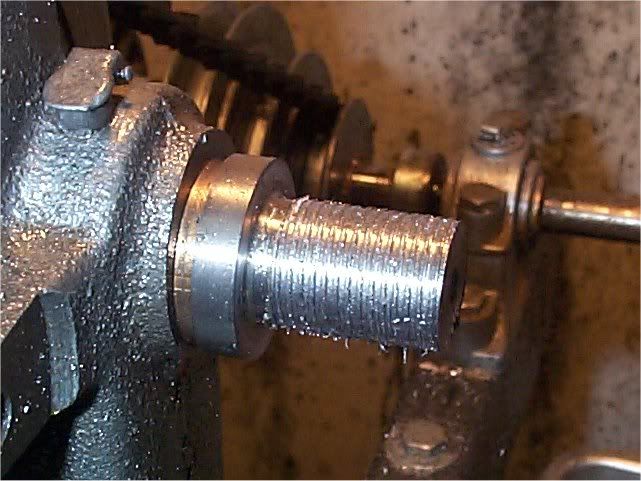
Glad I got a 3 foot hunk of that 1144.
Robert