As you all probably know, I have been thrashing away for the last couple of months on an i.c. engine. I thought it would be very clever to "stretch" my machining capabilities and make my own carburetor and sparkplug as well. The sparkplug is a failure. It did work on the bench, and it did fire the engine a few times, but the Corian is so fragile that it fractures if you look at it hard. I won't build my own sparkplug again. I have however, had fair success with the carburetor, except for making the needle valve. My plan to drill through a #2-56 brass screw and insert a sewing needle has fallen by the wayside, due to the fact that #1---my machinery isn't up to this accurate of work, and #2----Neither am I. However---I HAVE A NEW PLAN!!! My new plan involves grinding a needle shaped end on a steel #2-56 screw. Again, my Chinese lathe isn't up to it, but this is the method I have come up with. The dark blue part is the spindle in my mill, with a chuck on the spindle, and a 4" "fine" emery wheel and stub shaft in the chuck. The passion pink part is a smaller chuck and partial arbor that I salvaged out of an old power drill with a #2-56 x 3/4" long steel shcs in the jaws (the head has been cut off). (I really like this second chuck, because the jaws will close enough to hold a 1/32" diameter drill). The green part is a peice of 1" x 1/2" aluminum bar with a hole in it bored to be a "good rotating fit" on the stub arbor.---It is held in the jaws of my millling vice which is not shown. Here's how I see it working---I set the angle I want by tilting the green peice in my vice to whatever angle I want the needle valve to be and lock the vice there. I rotate the stub arbor and chuck with my fingers, slowly, and I raise the quill of the mill to advance the drill chuck and grinding wheel vertically---I have a fine finger control knob to do this with on my mill. This SHOULD give me very fine control, and should allow me to turn a quite accurate and concentric needle end on the screw. I will then make a small brass finger wheel and solder it to the other end of the screw. I'll let you know how it works out. I should have lots of peices to practice on. Nobody in town had this size of screw, so I had to order a box of 100 to get one. Sure hope I have better luck with the carburetor than I did with the sparkplug!!!
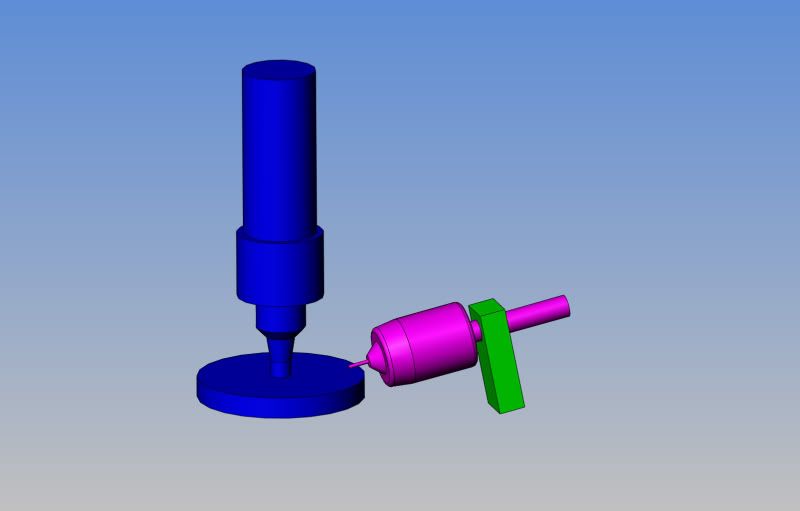