bigrigbri
Well-Known Member
- Joined
- Aug 20, 2011
- Messages
- 46
- Reaction score
- 4
For the people that requested pics of the tire mould.
The letters were stamped in on a rotating jig mounted to the centre boss and used 3/8" tool steel ground to shape on the end and then punched in.
Aferwards I lightly skimmed the rofile again usind an old ground file and using "wood carving" teq` I had again a smooth surface.
Oh yeh the small divits around the edge of the circumference on the side plates.
These were done individually and epoxied in 60 off!!!!!!!!!!!
The letters were stamped in on a rotating jig mounted to the centre boss and used 3/8" tool steel ground to shape on the end and then punched in.
Aferwards I lightly skimmed the rofile again usind an old ground file and using "wood carving" teq` I had again a smooth surface.
Oh yeh the small divits around the edge of the circumference on the side plates.
These were done individually and epoxied in 60 off!!!!!!!!!!!
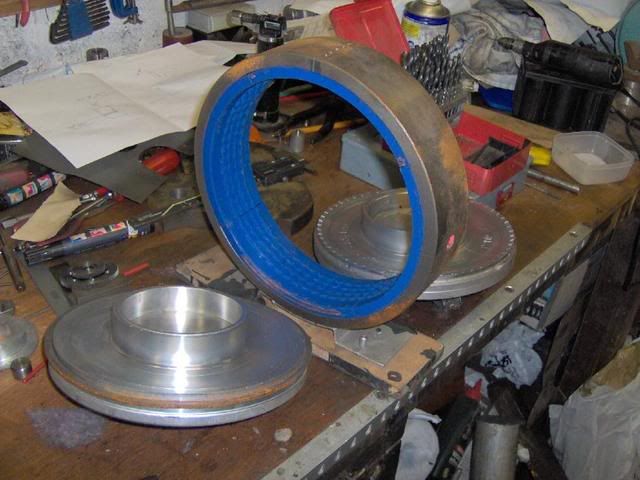
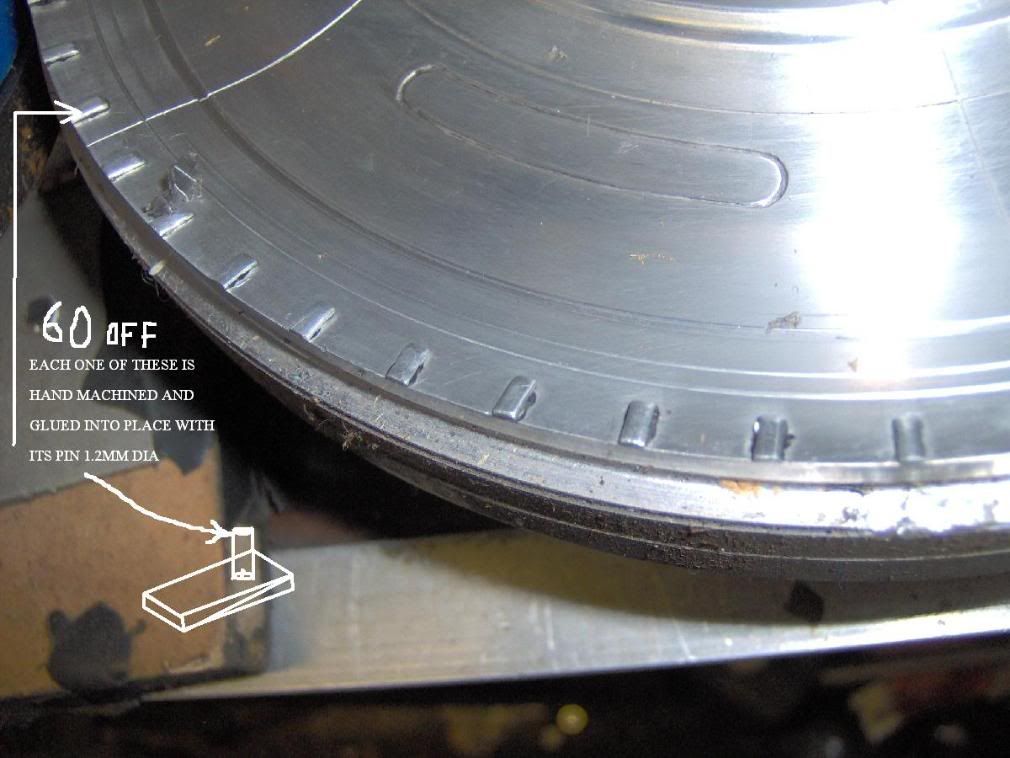
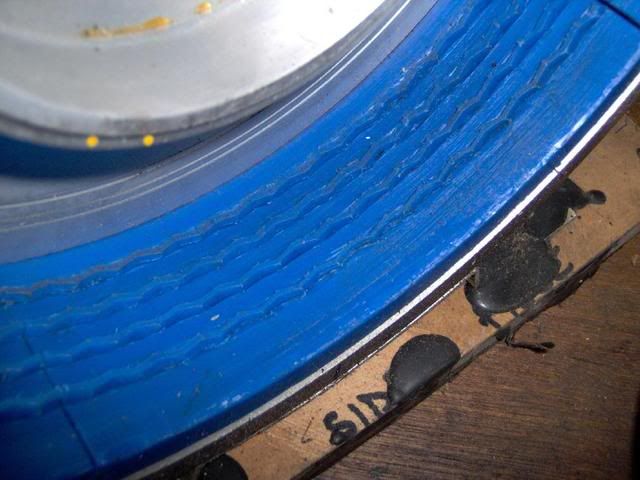
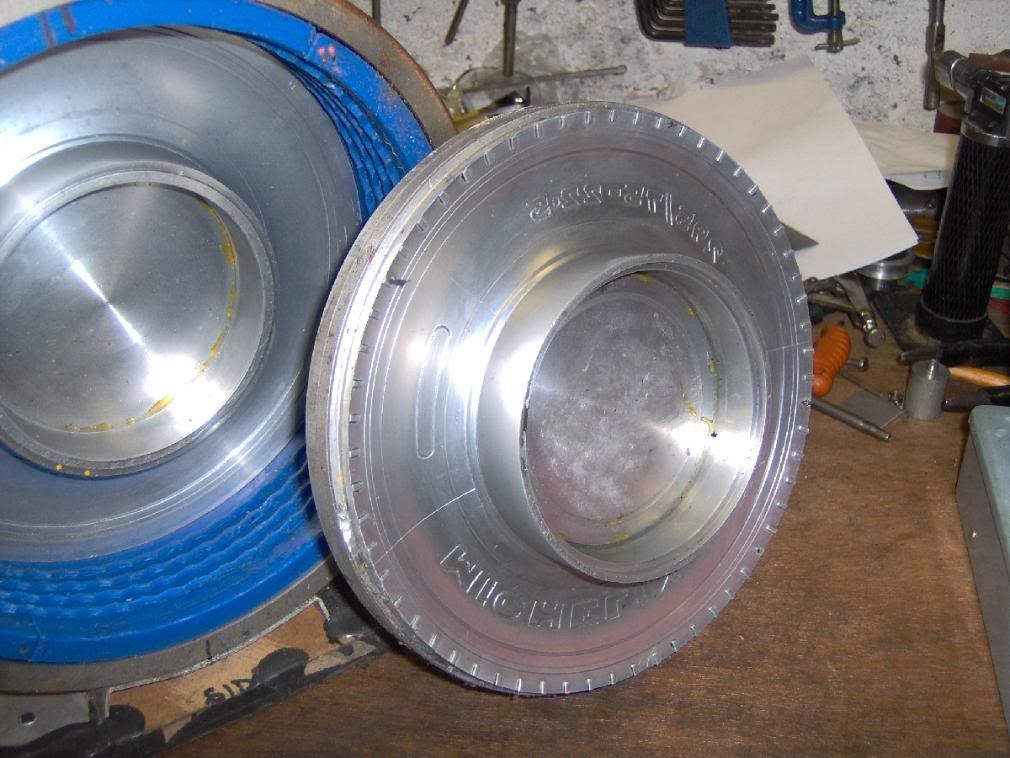
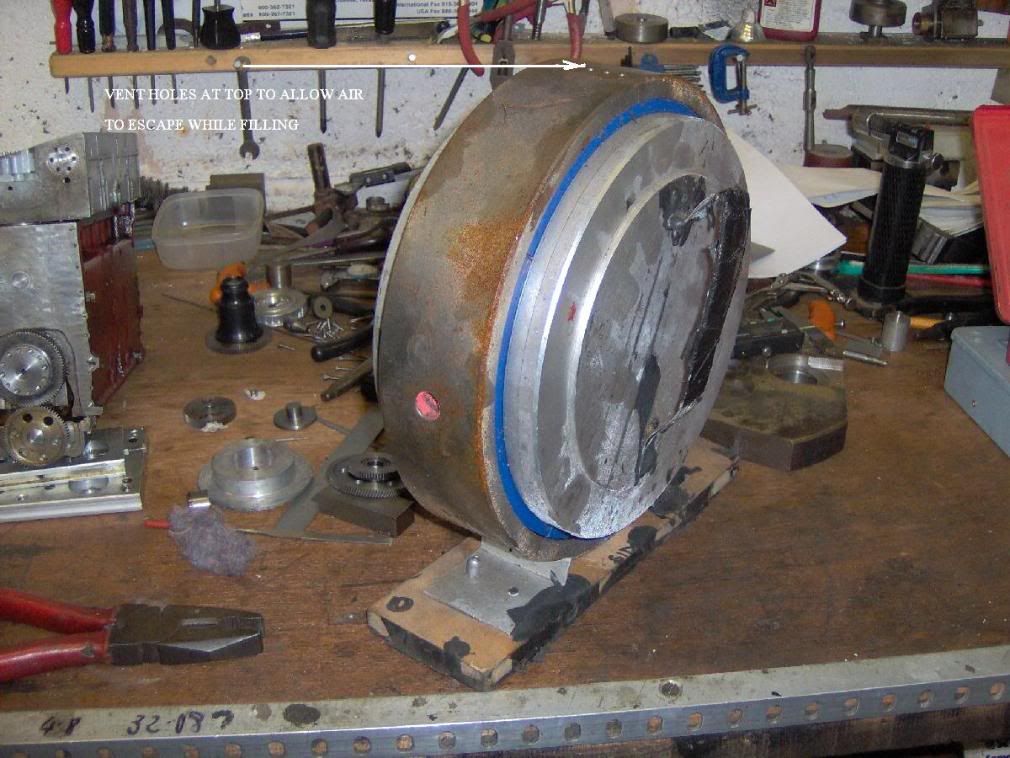