BobWarfield
Well-Known Member
- Joined
- Dec 27, 2007
- Messages
- 1,151
- Reaction score
- 1
;D
A nice big piece of eBay aluminum plate arrived late yesterday, so this fine Saturday morning I wanted to get started making chips out of it. Can't stand to leave a good piece of metal alone! My first task was to cut it down to size. I am building a 12" disc sander, so I wanted a piece that was about 12 1/2" square to make life easier. Several ways I could have gone about cutting out the plate. It's too big for my Multicutter, but I could have used an air cut-off tool, a sabre saw with a metal cutting blade, or the mighty Milwaukee Sawzall that lurks in one corner of the garage. Feeling a bit playful this morning, I dragged out my plasma cutter instead:
This is another of my many eBay deals. Industrial grade heavy capacity ESAB Powercut 1500 plasma purchased for an embarassingly low price. Cool looking unit isn't it? It will cut 1" aluminum and I think 1.5" steel.
It will take longer to set up a fence to guide the plasma torch than to make the cut. A big piece of stock and a couple of Kant-Twist clamps plus calibrated eyeballs will do. You'll soon see the plasma isn't all that accurate, so my eyeballs are good enough for layout!
Sorry, was by myself, so no action shots.
You can see that edge is a bit gnarly. No matter. I'm going to fit the hub I machined in the center and then spin that square plate on my rotab on the mill to make the disc round.
FWIW, that nasty slaggy cut is all me. A plasma being run at optimal feed speeds, fed smoothly and precisely, with good torch height control, and the right amperage (phew!) can make a very clean cut. Since I had no idea the right parameters and poor ability to execute them if I did, I cranked the amps and tried to keep the torch moving fairly quickly and smoothly. I think I was too slow! Miller says for 1/4" aluminum you need to be moving at 100" per minute: not quite 2" per second. I was definitely not moving that quickly.
Before this cutter I had a 110V little Hobart plasma. I sold it to an artist lady. She came over to try it and she was getting smooth flowing cuts freehand first try. It was so annoying! I'll never get that, but I do intend to build a CNC plasma table at some point.
Cheers,
BW
A nice big piece of eBay aluminum plate arrived late yesterday, so this fine Saturday morning I wanted to get started making chips out of it. Can't stand to leave a good piece of metal alone! My first task was to cut it down to size. I am building a 12" disc sander, so I wanted a piece that was about 12 1/2" square to make life easier. Several ways I could have gone about cutting out the plate. It's too big for my Multicutter, but I could have used an air cut-off tool, a sabre saw with a metal cutting blade, or the mighty Milwaukee Sawzall that lurks in one corner of the garage. Feeling a bit playful this morning, I dragged out my plasma cutter instead:
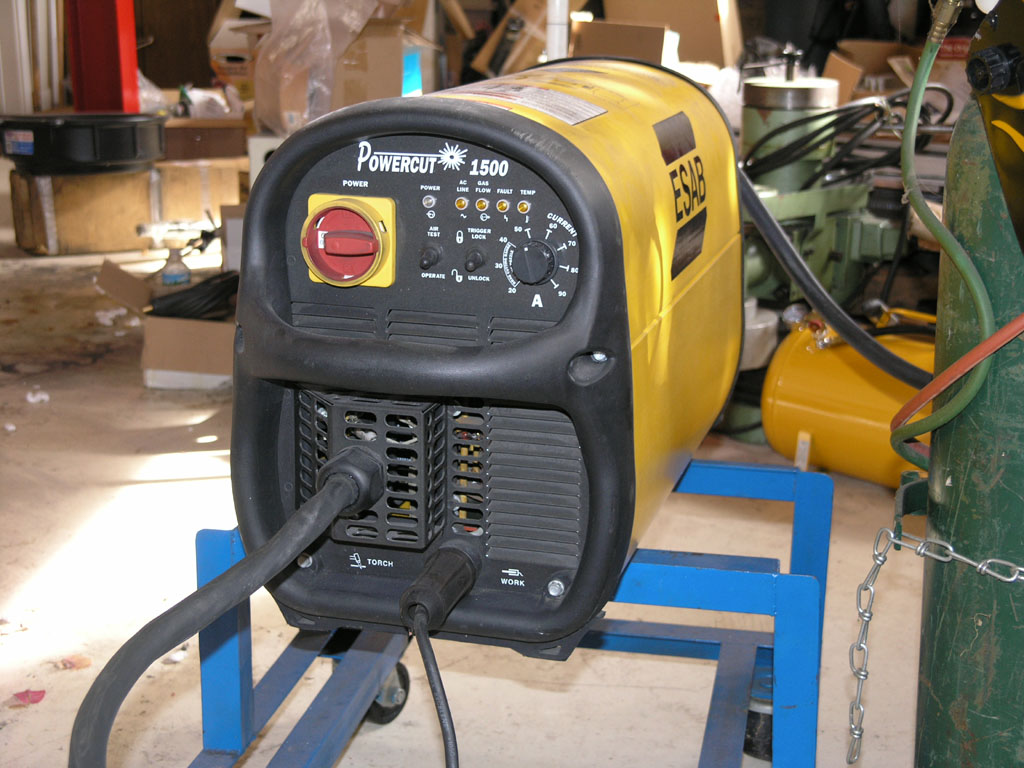
This is another of my many eBay deals. Industrial grade heavy capacity ESAB Powercut 1500 plasma purchased for an embarassingly low price. Cool looking unit isn't it? It will cut 1" aluminum and I think 1.5" steel.
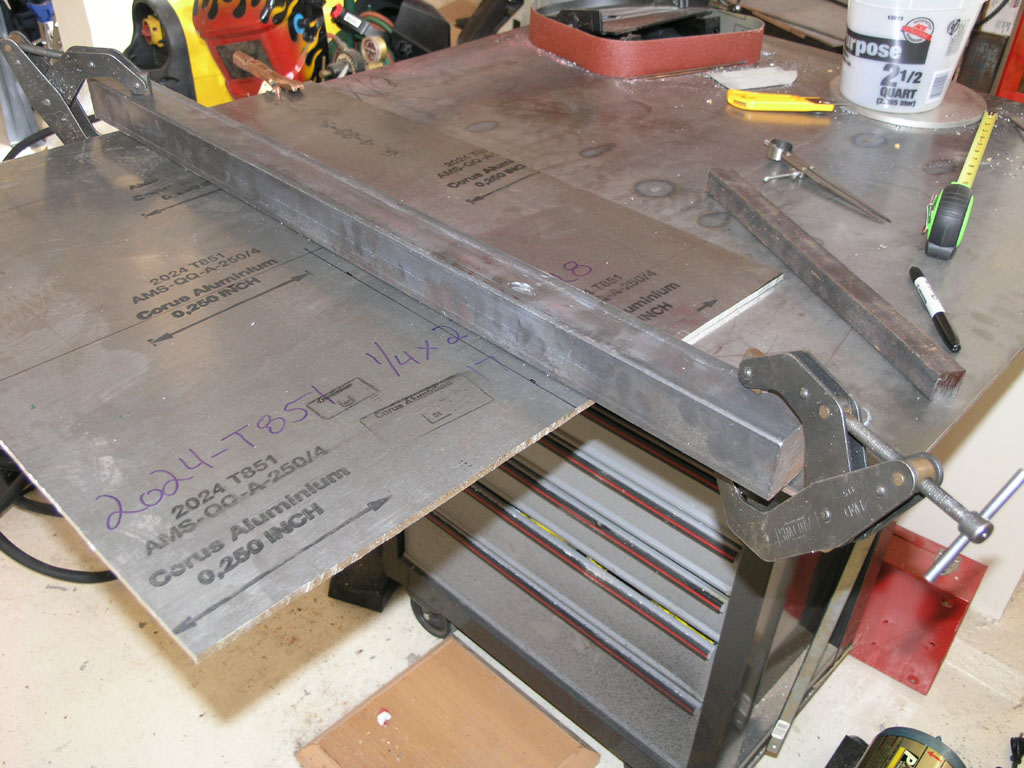
It will take longer to set up a fence to guide the plasma torch than to make the cut. A big piece of stock and a couple of Kant-Twist clamps plus calibrated eyeballs will do. You'll soon see the plasma isn't all that accurate, so my eyeballs are good enough for layout!
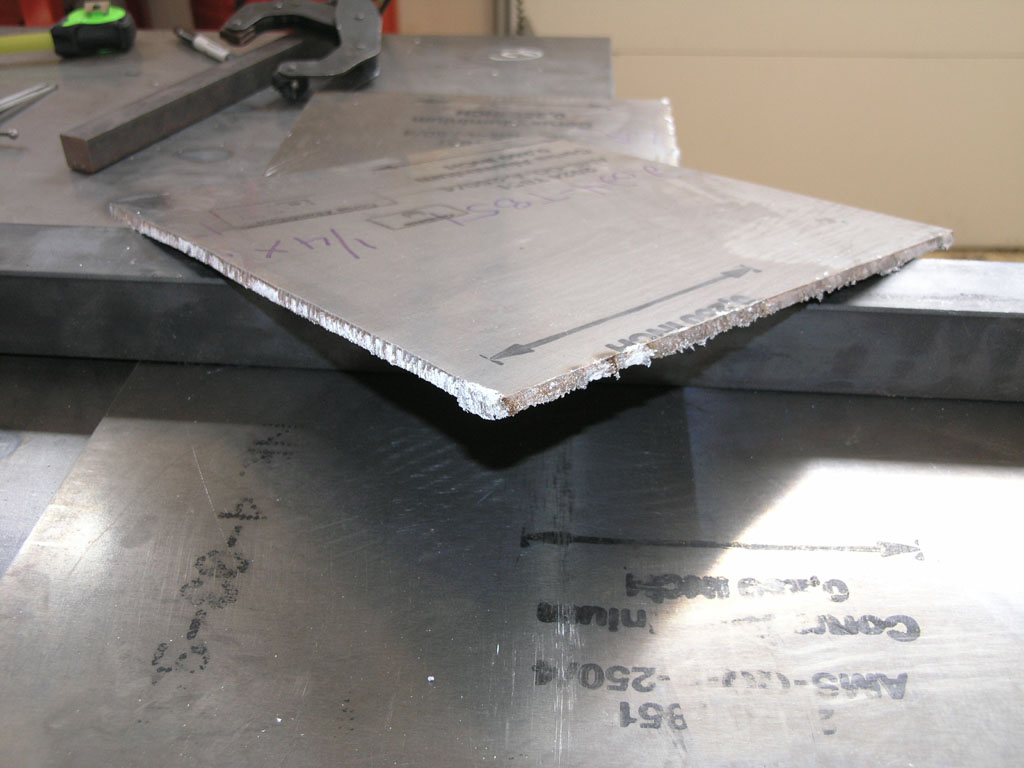
Sorry, was by myself, so no action shots.
You can see that edge is a bit gnarly. No matter. I'm going to fit the hub I machined in the center and then spin that square plate on my rotab on the mill to make the disc round.
FWIW, that nasty slaggy cut is all me. A plasma being run at optimal feed speeds, fed smoothly and precisely, with good torch height control, and the right amperage (phew!) can make a very clean cut. Since I had no idea the right parameters and poor ability to execute them if I did, I cranked the amps and tried to keep the torch moving fairly quickly and smoothly. I think I was too slow! Miller says for 1/4" aluminum you need to be moving at 100" per minute: not quite 2" per second. I was definitely not moving that quickly.
Before this cutter I had a 110V little Hobart plasma. I sold it to an artist lady. She came over to try it and she was getting smooth flowing cuts freehand first try. It was so annoying! I'll never get that, but I do intend to build a CNC plasma table at some point.
Cheers,
BW